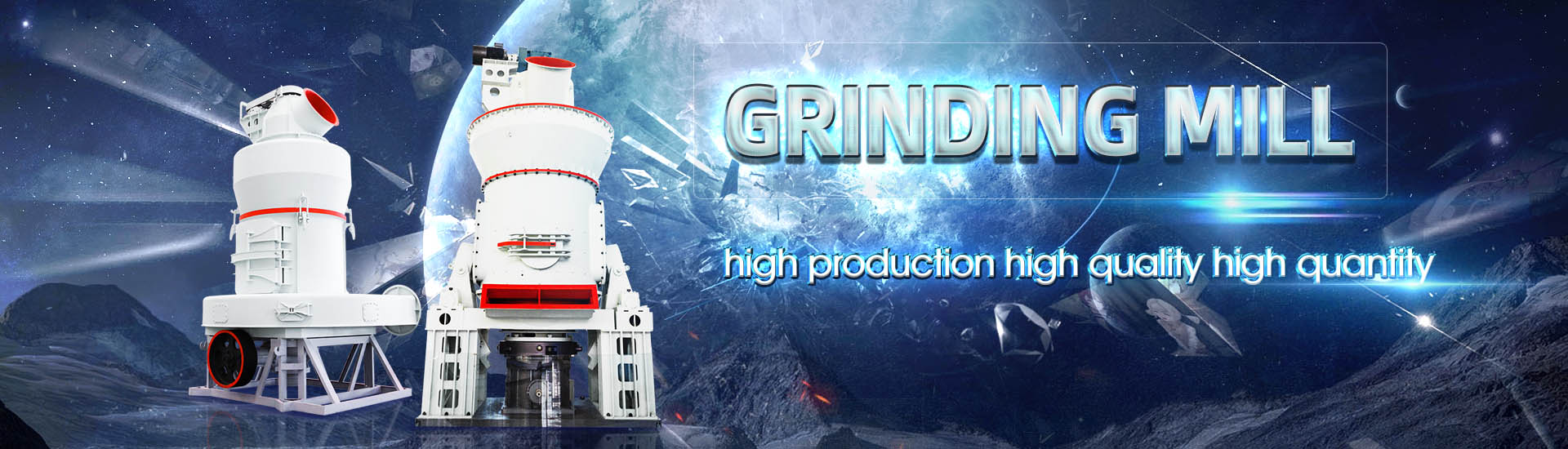
Ball mill driving shaft
.jpg)
Ball Mill Drives Crushing Grinding Drives David
Designed to deliver exceptional levels of performance and value, David Brown Santasalo ball mill drives are optimised for primary and secondary grinding applicationsFlexible drive solutions for use in ball mills A ball mill is a horizontal cylinder filled with steel balls or the like This cylinder rotates around its axis and transmits the rotating effect to the balls The material fed through the mill is crushed by the Industrial gear unit drive solution for ball mills SEW A: Large concrete surface at mill drive end, Fig 2A, with increased tendency towards cracking Shaft position shst, impairment of tooth contact, and risk of wearGIRTH GEAR Artec MachineLarger ball and SAG mills, with higher installed power ratings relative to the mill diameter, offer higher efficiency and throughput, roundtheclock reliability and the opportunity to mine in remote areas This makes low ore grades economical to grind ABB has delivered some of the world's largest GMDs: • 22 MW GMD for 28’ ball millGearless mill drives ABB
.jpg)
Products and solutions Drive systems for all grinding ABB
The ABB gearless mill drive is the most powerful mill drive system on the market It provides highest availability, longterm reliability, flexibility and efficiency at competitive cost This is achieved by eliminating all mechanical components of a conventional mill drive system (ringgear, pinion, gearbox, coupling, motor shaft and motor The Metso QdX4TM Mill Drive was developed in close collaboration with both CMD and Ferry Capitain Engineering as a solution for the mining industry for large mill drives The Metso QdX4TM Mill Drive features internal torque splitting capability transmitting motor input power to the pinion shaft and equally dividing into two mill pinions This Metso QdX4 Mill Drive systemABB’s GMD is the most powerful mill drive system in the market to power semiautogenous (SAG), ball and autogenous (AG) mills, This ’workhorse’ for grinding operations combines a robust, servicefriendly and fit for purpose Gearless mill drives Grinding ABBBall mills and rotary kilns are most challenging applications that demand a big deal from the drive system High performance and reliability are very important When it comes to milling of iron ore, limestone and clinker large axial and radial forces occur Singlepinion drives must be able to withstand the acting forces permanentlySingle pinion drive Gear Units Products Flender
.jpg)
Gearless mill drives Grinding ABB
Our GMD eliminates all mechanical components of a conventional mill drive system, such as ringgear, pinion, gearbox, coupling, motor shaft and motor bearings: By mounting the rotor poles directly onto the mill, the mill itself Ball mills can be used for dry or wet grinding of various ores and other grindable materials and also has a driving part, such as a motor, and transmission gears, pulleys, Vbelts, etc 1 the hollow shaft is made of cast steel, Ball Mill SBM Ultrafine Powder TechnologyFine Grinding and Mill Cooling PROBLEM Insufficient mill cooling lead to material agglomeration on balls and liners The grinding is not any more done by balls against material but by material against material SOLUTION Adapted mill cooling, playing with:Clinker temperatureMill ventilationWater injectionEVERY COMPONENT OF BALL MILL DETAILED EXPLAINEDBall mill 9000 HP Motor speed 990 rpm Mill speed 14 rpm R/L ill diameter 5 m etary gear driving a cement mill B : The equivalent onepart internally toothed annulus in the transmission train, Shaft position shift, impairment of tooth contact, and risk of wear B: GIRTH GEAR Artec Machine
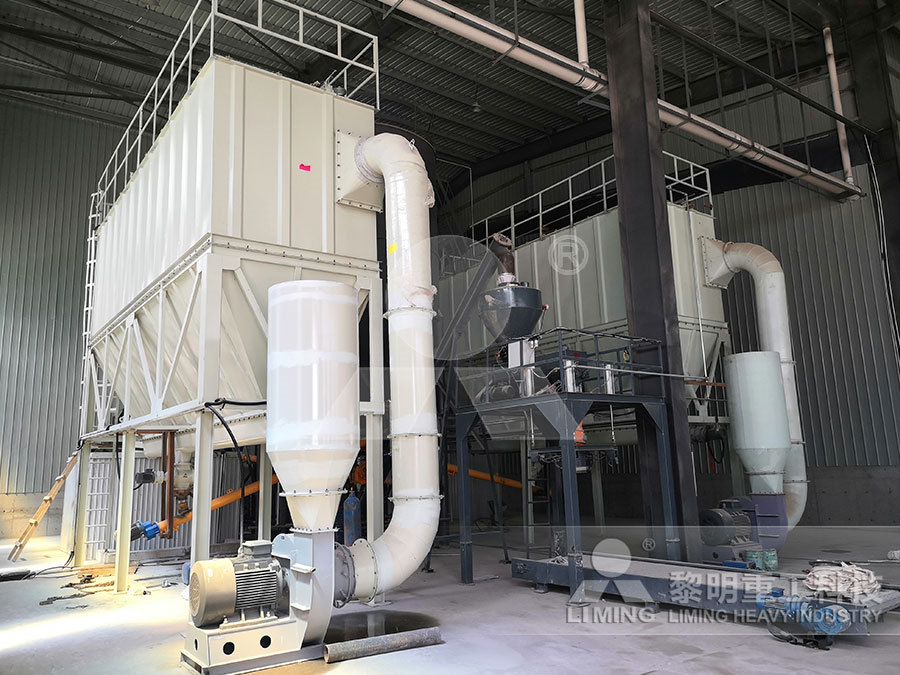
Ball mill PPT SlideShare
2015年4月24日 2 Ball mill consist of a hollow cylindrical shell rotating about its axis Axis of the shell horizontal or at small angle to the horizontal It is partially filled with balls made up of Steel,Stainless steel or rubber Inner surface of the shell is lined with abrasion resistant materials such as Manganese,Steel or rubber Length of the mill is approximately equal to its diameter Horizontal Ball Mill Drives We can provide all elements of a mill drive system as a fully optimised solution to suit your process exactly, or individual components as required Book an appointment Gear cases machined from rigid housings to ensure optimum shaft alignment, Horizontal Ball Mill Drives dbsantasaloThe invention relates to a cooling water jacket of a bearing sleeve of a driving shaft of a vibrating ball mill Two ends of the bearing sleeve are provided with round bosses; the middle of the bearing sleeve forms a circularannular water jacket, and two half water jacket rings matched with the circularannular water jacket are welded on the inner sides of the round bosses at two CNA Cooling water jacket of bearing sleeve of driving shaft 2016年10月23日 The pinion shaft is double ended so it is also reversible All ball Mill gearing is designed in accordance with sound engineering principles and at the same time with consideration given to the long range economics involved Extremes such as excessively high ratios or a very low number of teeth in the pinion are always avoidedBall Mill Gear 911Metallurgist
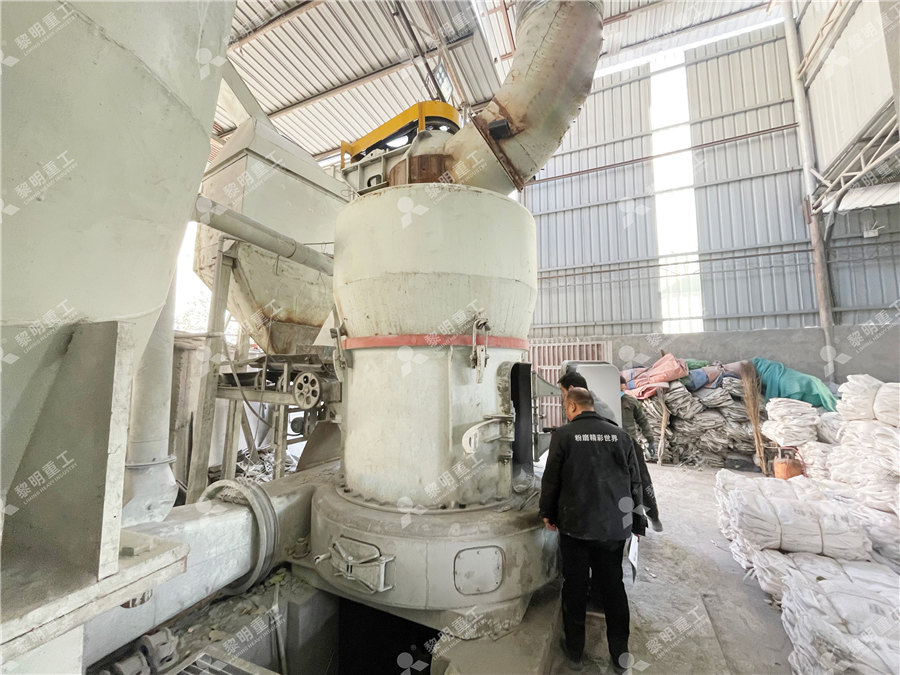
The Ultimate Guide to Ball Mills Miningpedia
2019年8月14日 During the operation,the hollow shaft in the center of the ball mill drives the mill body to rotate under the driving of the power system • Edge driving ball mill: the motor drives the gear on the edge of the cylinder through the reducer to drive the cylinder movement 62017年2月13日 The apparent difference in capacities between grinding mills (listed as being the same size) is due to the fact that there is no uniform method of designating the size of a mill, for example: a 5′ x 5′ Ball Mill has a working Ball Mills 911Metallurgist2022年1月1日 Ball mill is the size curtailment technique, which maneuver materials in the rotating cum cylindrical boudoir to mill the materials into a splendid powder Driving gear is attached to the main shaft attached from electrical motor to the driven gearsDesign and simulation of gear box for stone crushing ball millThe Metso QdX4TM Mill Drive was developed in close collaboration with both CMD and Ferry Capitain Engineering as a solution for the mining industry for large mill drives The Metso QdX4TM Mill Drive features internal torque splitting capability transmitting motor input power to the pinion shaft and equally dividing into two mill pinionsMetso QdX4 Mill Drive system
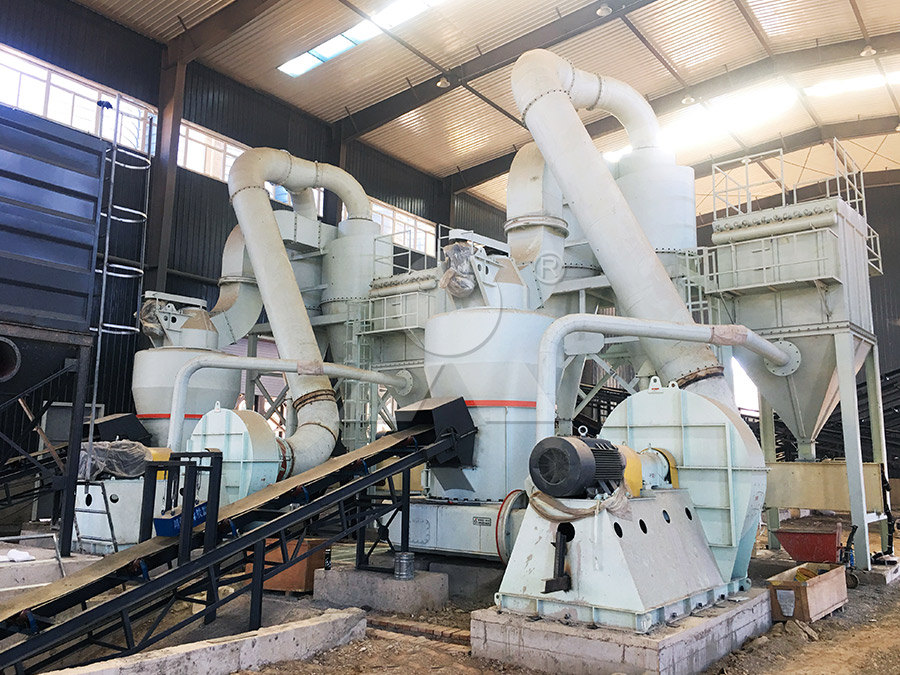
Increasing availability through advanced Gearless Drive Technology
timetaking grinding out of the ball mill Ball mills with Energy savings typically up to 750,000 USD per annum for a 20 MW SAG mill considering a power supply price of 11 US Cents per kWh Erection and commissioning works on site are reduced by using a completely installed, wired and precommissioned Ehouse2021年2月26日 One method for increasing the energy efficiency of ball mills is The mass of the drum without the grinding media is 84 Mg The drum is set in rotational motion by driving a ring gear mounted on the drive side The ring gear is engaged with a pinion gear In versions with lowspeed motors, the pinion is set on a shaft directly Energy Efficiency Analysis of Copper Ore Ball Mill Drive synchronous motor driven ball mill The Benshaw variable frequency drive powers the 4160 volt 3500HP synchronous ball mill motor during positioning to smoothly rotate the ball mill and bring it to the proper position for maintenance The customer’s previous system utilized multiple DC contactors and a motorized cam switch to position the millBall Mill Positioning Benshaw IncOur durable and resilient drive solutions ensure a reliable ball mill operation Drive packages from a single source: industrial gear units and segmented girth gears Large girth gears are installed around the cylinder to rotate the horizontal ball mill cylinders A pinion connects these directly to the industrial gear unitIndustrial gear unit drive solution for ball mills SEWEURODRIVE
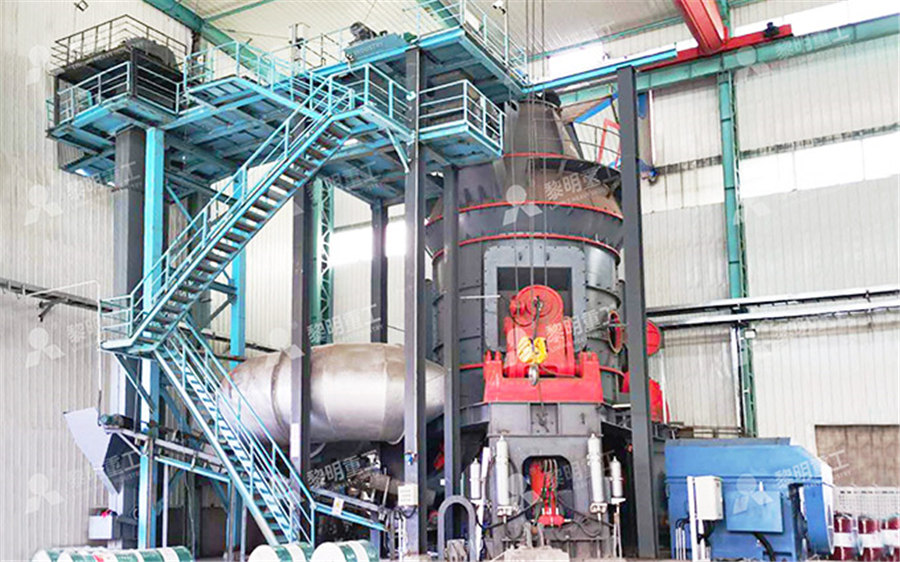
Ball Mill Maintenance Installation Procedure 911Metallurgist
2016年10月20日 Am sure your Ball Mill is considered the finest possible grinding mill available As such you will find it is designed and constructed according to heavy duty 911 Metallurgist is a trusted resource for practical insights, solutions, and support in mineral processing engineering, helping industry professionals succeed with proven expertise Ball Mill Maintenance Based on the MPT TITAN™ design, the Mills are girth gear dual pinion driven with selfaligned flanged motors, running on hydrodynamic oil lubricated bearings The TITAN design enables you to run full process load 40% Ball charge at 80% critical speed – Ball Mills – MechProTech MPT2015年7月28日 Ball Mill PINION SHAFT BEARINGS Pinion shaft bearings are of the SKF antifriction type mounted in a common twin bearing assembly Bearings are fixed in place so that the pinion shaft of the mill is always in alignment with the drive components Vbelt driven mills are furnished with an outboard bearing of similar constructionTrunnion Bearing Assembly Ball Mill Rod Mill 911MetallurgistThis document provides instructions for installing a 16x22ft, 2800kW ball mill It outlines 8 key steps: 1) Prepare the foundation and install the trunnion bearing sole plates 2) Assemble and mount the trunnion bearings onto the sole 16' X 22' Ball Mill Installation Manual PDF Scribd
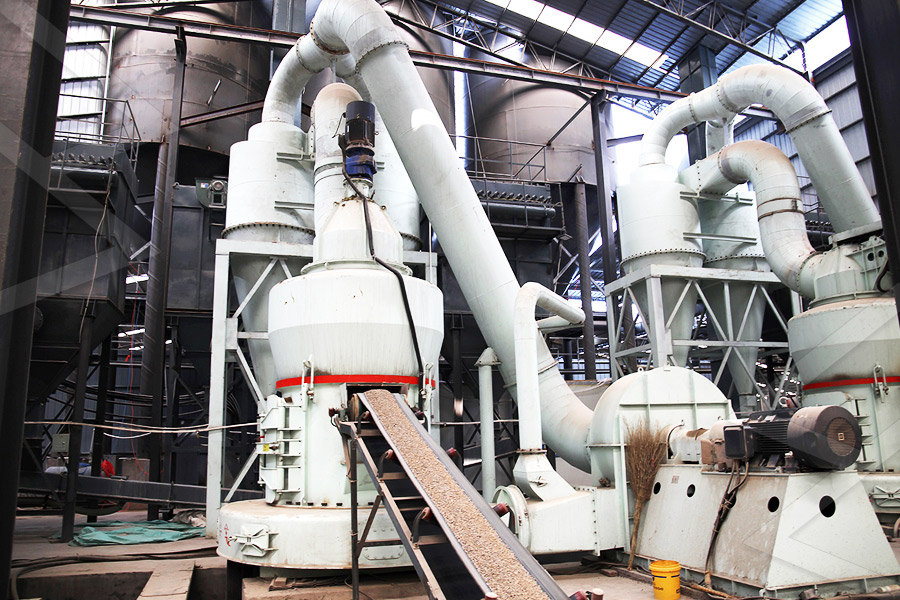
What is an inching drive? Motion Control Tips
2018年5月2日 An inching drive is used as an auxiliary system to the main drive for a large machine such as a ball mill, industrial kiln, conveyor, or elevator Its purpose is to turn the equipment at a speed slower than the normal operating 2013年4月1日 Ball mill hollow shaft diameter and ball mill cylinder clearance diameter is about 03~055 With the normal operating voltage, because the hollow shaft is la rger in size, so the(PDF) The Ball Mill Driving Device Fault and the Main The ball mill trunnion, also known as the hollow shaft is an important part of the ball mill that carries the rotation of the ball mill barrelIt is a special type of steel casting It mainly plays the role of supporting and connecting the cylinder in the whole Ball Mill Trunnion Hollow Shaft For Ball Mill Customization 2024年1月1日 According to the discharge methods of the ball mill, it can be divided into overflow ball mill, and discharge is through the hollow shaft Grate ball mill (Fig 3), the discharge end of the mill is set with a gratePeripheral discharge ball mill, and the products are discharged through the discharge port around the cylinderBall Mill SpringerLink

Inching drives – one way to improve mill safety Metso
2022年4月11日 They have their own lube units and are typically coupled to the mill pinion shaft Hydraulic inching drives typically deliver high torques (73 m) diameter ball mill charge typically weighs around 2 million lbs (907 tons) Semi Autogenous Grinding (SAG) mill charge can be equally as heavy2018年6月30日 STRESSSTRAIN STATE OF PNEUMATIC FLEXIBLE SHAFT COUPLING FOR BALL MILL DRIVES Mechanical system drives consist of driving machines and gearing mechanisms interconnected by shafts and couplingsSTRESSSTRAIN STATE OF PNEUMATIC FLEXIBLE SHAFT COUPLING FOR BALL MILL Rugby Cement ball mill drive shaft recovery Following a journal failure on a 40tonne/hour cement ball mill at RMC’s cement plant in Rugby, Metalock Engineering Group orbitally machined the badly scored shaft to clean up enabling a new white metal bearing to be fitted and the mill returned to production with minimum disruptionMetalock’s orbital machining expertise keeps ball mill in productionMill Shell: The foundation of the Center drive ball mill, the mill shell, is a cylindrical structure made of premiumgrade steelTongli heavy machinery is equipped with a large annealing furnace of 65x65x20m and a 65x65x20m large sandblasting room, which can conduct overall heat treatment and sandblasting on the ball mill to ensure the service life and appearance of the Center drive ball millBall millPRODUCTTongli Machinery

Mill Pinion Gears dbsantasalo
Our high torque, high precision integral and nonintegral mill pinions are used in SAG, horizontal ball mill and rotary kiln applications across the globe Book an appointment Mill pinions can be manufactured integral with the shaft or as bored pinions with separate shafts;Ball mills and rotary kilns are most challenging applications that demand a big deal from the drive system High performance and reliability are very important When it comes to milling of iron ore, limestone and clinker large axial and radial forces occur Singlepinion drives must be able to withstand the acting forces permanentlySingle pinion drive Gear Units Products FlenderOur GMD eliminates all mechanical components of a conventional mill drive system, such as ringgear, pinion, gearbox, coupling, motor shaft and motor bearings: By mounting the rotor poles directly onto the mill, the mill itself Gearless mill drives Grinding ABBBall mills can be used for dry or wet grinding of various ores and other grindable materials and also has a driving part, such as a motor, and transmission gears, pulleys, Vbelts, etc 1 the hollow shaft is made of cast steel, Ball Mill SBM Ultrafine Powder Technology
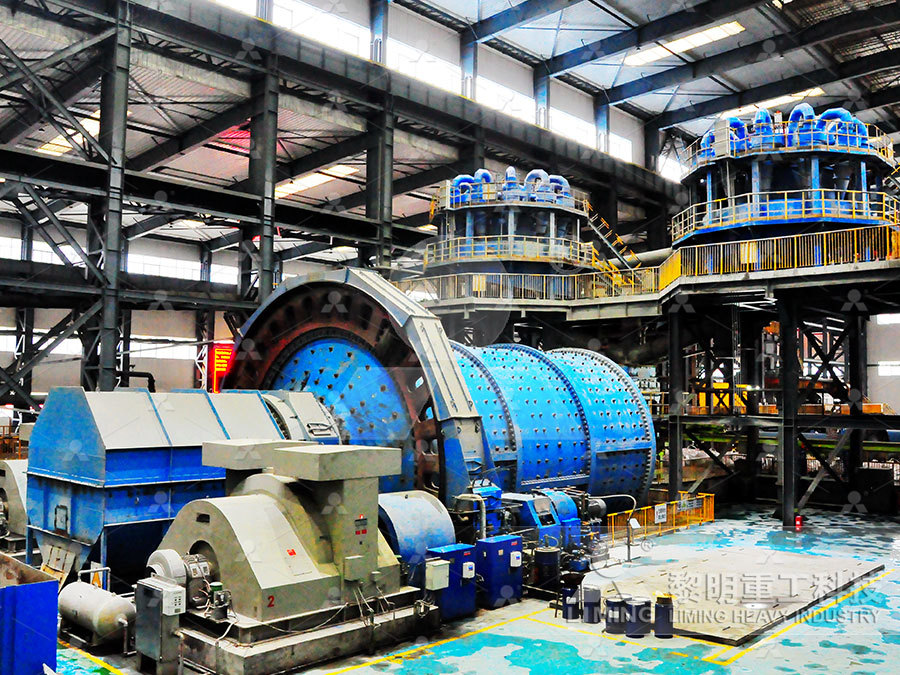
EVERY COMPONENT OF BALL MILL DETAILED EXPLAINED
Fine Grinding and Mill Cooling PROBLEM Insufficient mill cooling lead to material agglomeration on balls and liners The grinding is not any more done by balls against material but by material against material SOLUTION Adapted mill cooling, playing with:Clinker temperatureMill ventilationWater injectionBall mill 9000 HP Motor speed 990 rpm Mill speed 14 rpm R/L ill diameter 5 m etary gear driving a cement mill B : The equivalent onepart internally toothed annulus in the transmission train, Shaft position shift, impairment of tooth contact, and risk of wear B: GIRTH GEAR Artec Machine2015年4月24日 2 Ball mill consist of a hollow cylindrical shell rotating about its axis Axis of the shell horizontal or at small angle to the horizontal It is partially filled with balls made up of Steel,Stainless steel or rubber Inner surface of the shell is lined with abrasion resistant materials such as Manganese,Steel or rubber Length of the mill is approximately equal to its diameter Ball mill PPT SlideShareHorizontal Ball Mill Drives We can provide all elements of a mill drive system as a fully optimised solution to suit your process exactly, or individual components as required Book an appointment Gear cases machined from rigid housings to ensure optimum shaft alignment, Horizontal Ball Mill Drives dbsantasalo
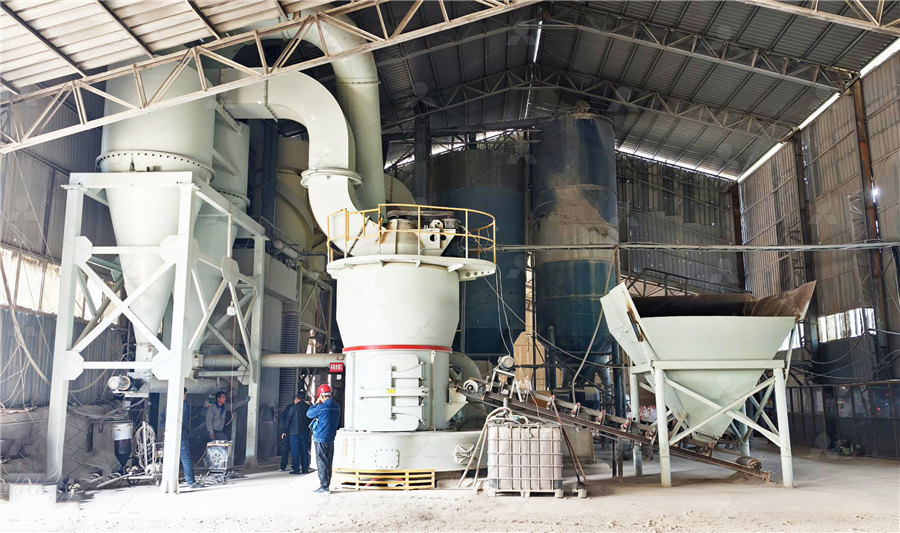
CNA Cooling water jacket of bearing sleeve of driving shaft
The invention relates to a cooling water jacket of a bearing sleeve of a driving shaft of a vibrating ball mill Two ends of the bearing sleeve are provided with round bosses; the middle of the bearing sleeve forms a circularannular water jacket, and two half water jacket rings matched with the circularannular water jacket are welded on the inner sides of the round bosses at two 2016年10月23日 The pinion shaft is double ended so it is also reversible All ball Mill gearing is designed in accordance with sound engineering principles and at the same time with consideration given to the long range economics involved Extremes such as excessively high ratios or a very low number of teeth in the pinion are always avoidedBall Mill Gear 911Metallurgist2019年8月14日 During the operation,the hollow shaft in the center of the ball mill drives the mill body to rotate under the driving of the power system • Edge driving ball mill: the motor drives the gear on the edge of the cylinder through the reducer to drive the cylinder movement 6The Ultimate Guide to Ball Mills Miningpedia