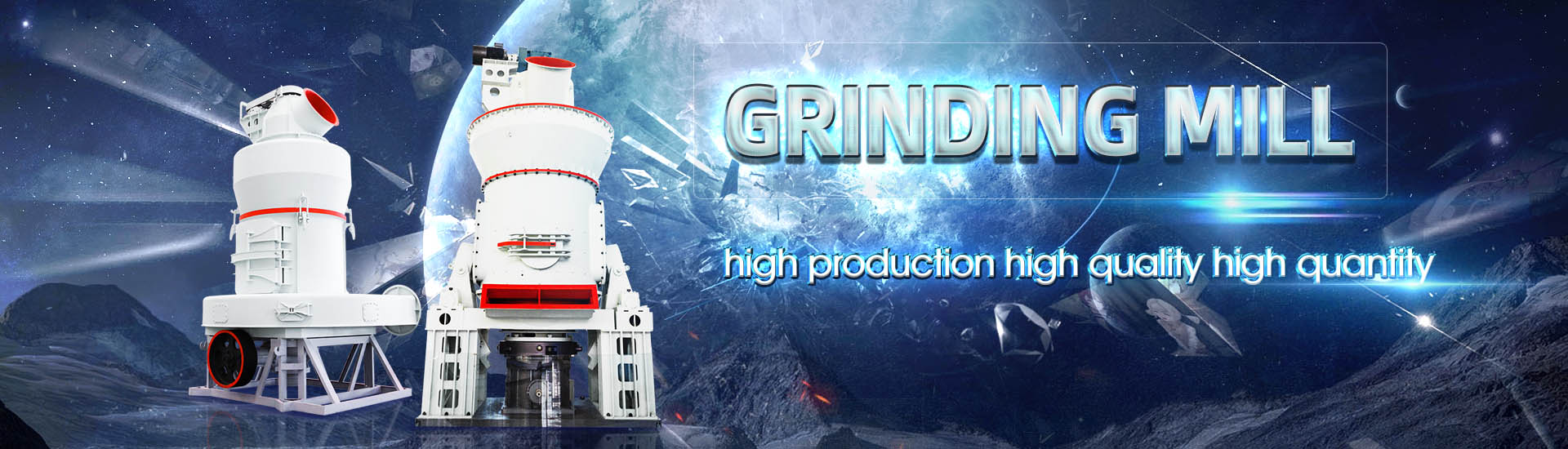
Ore powder making plant transfer
.jpg)
Development and Problems of Fluidized Bed Ironmaking Process:
2023年10月9日 Fluidized bed technology has become a crucial method used to process iron ore powder in nonblast furnace ironmaking, such as smelting reduction and direct reduction This paper introduces the working principle and several typical working states of fluidized bed (FB) Reasonable and efficient process flow: The production line usually adopts the process flow of “crushinggrindingore dressingsmelting”, and each link is carefully designed to ensure that Gold Ore Processing Production Line TAYMACHINERY2024年8月15日 A mineral processing plant is a place dedicated to processing ores, converting raw ores extracted from mines into highgrade mineral products or metals through a series of physical and chemical methodsMineral Processing Plants: What You Need to Know2018年7月11日 Iron ore and iron ore pellets are important sources of iron for manufacturing steel The iron ore production has significantly expanded in recent years, owing to increasing steel demands inIron Ore Pelletizing Process: An Overview ResearchGate
.jpg)
Iron Ore Sintering SpringerLink
2024年1月1日 Iron ore sintering is the iron ore powder agglomeration process that changes fine iron ore powder into the lumpy ironbearing raw material used for blast furnace ironmaking 2021年3月15日 Iron ore concentration typically involves comminution, separation, and agglomeration Comminution is the grinding of the ore to liberate the valuable ironbearing minerals from gangue materials (ofIron Ore Pelletization: Part I Fundamentals TaylorOne is the Flash Ironmaking Technology (FIT) and the other is a movingbed process for continuous ironmaking with gaseous reduction of iron ore concentrate (MBIT) These Making Iron Directly From Concentrate by Gaseous ReductionWhen ore is first processed (typically close to the mine) it is crushed to gravelsized chunks and then ground to a fine powder and the ore minerals are physically separated from the rest of the rock to make a concentrate82: Mining and Ore Processing Geosciences LibreTexts
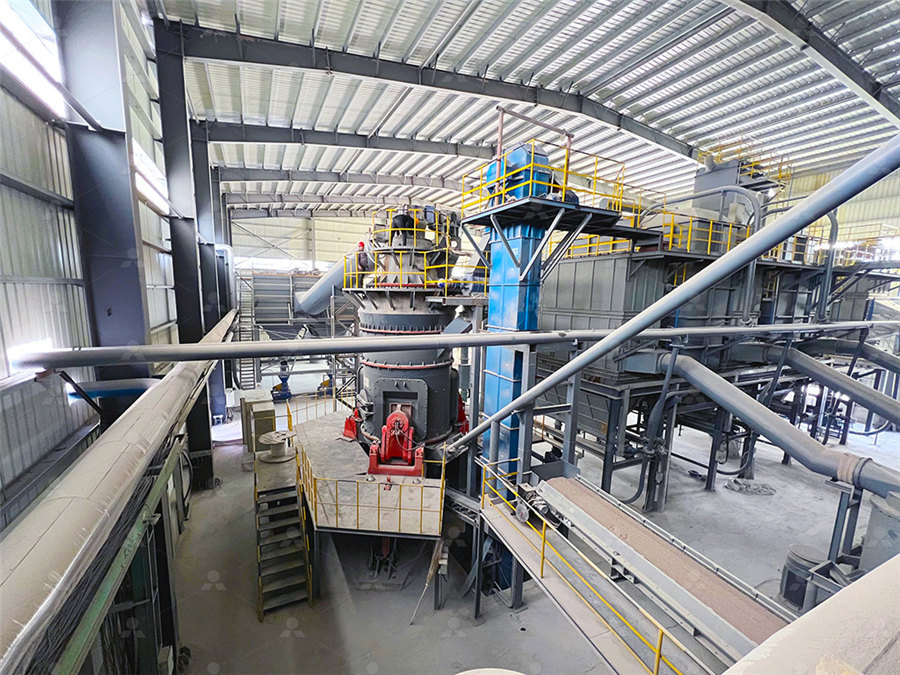
Study on the Basic Characteristics of Iron Ore Powder
2022年7月30日 In order to study in depth the differences in basic characteristics between iron ore fines commonly used by a steel company, and guide the sintering performance plant to choose the best ore allocation method, 4 天之前 Copper industrial minerals include: natural copper, chalcopyrite, chalcocite, tetrahedrite, azurite, malachite, etc Chalcopyrite (a compound of copper, sulfur, and iron) is mined mainly, followed by chalcocite and bornite If Copper Ore Processing Plants, Flow And Equipment2015年6月11日 Powder transfer via vacuum offers a solution by providing a contained environment for transport, thereby reducing explosion risk and cutting back on product waste Some vacuum conveying systems offer the additional Contained Powder Transfer: VacuumBased 2024年4月1日 As a typical nonblast furnace ironmaking method, fluidized ironmaking directly uses pulverized ore as raw material, which eliminates the process of pelletizing and sintering and helps to realize the efficient utilization of lowgrade complex iron ore [8]The direct reduction of iron ore in fluidized beds is a promising method for iron making because of its high heat and Direct reduction of ironore with hydrogen in fluidized beds: A
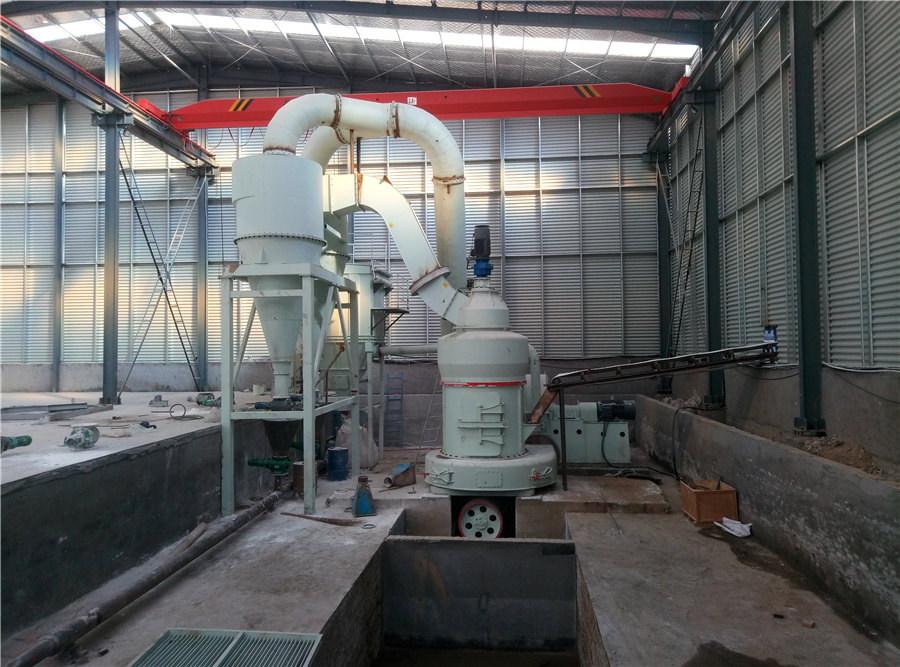
Sintered Ore an overview ScienceDirect Topics
2019年12月24日 Energy Resources, Its Role and Use in Metallurgical Industries RC Gupta, in Treatise on Process Metallurgy: Industrial Processes, 2014 423132 Sinter Making The iron ore fines (− 10 mm) are agglomerated using Dwight Lloyed sintering machine The iron ore fines and coke breeze fines mix with moisture is fed on the sinter bed which is ignited by a gas 2023年3月1日 Basu et al analyzed the breakage process of iron ore in transfer chute system using DEM and Tavares UFRJ model, and the breakage particle size of iron ore was calculated in different stage (Basu et al, 2023) The advantage of the Tavares UFRJ model is that it can directly calculate the particle size distribution of fragmentsModeling and simulation of mechanical degradation of iron ore Mix dry chrome powder, suitable binders (such as molasses) and lime powder Send the mixture into the chrome ore briquetting machine Finally, the entire chrome ore powder briquette production line feeds smoothly and evenly The workload of the briquetting machine is stable and the production efficiency is high, which solves the problem of the Iron Powder Briquetting Machine Fote Machinery2024年3月16日 The sintering process is an intricate system with a protracted process flow The steps in the manufacturing line are primarily composed of the ingredients and mixing process, the sintering operation process, and the treatment of the sintered ore [39, 40]22 Important parameters and characteristics of sintering process As shown in Fig 2, all variables affecting Application of deep learning in iron ore sintering process: a review
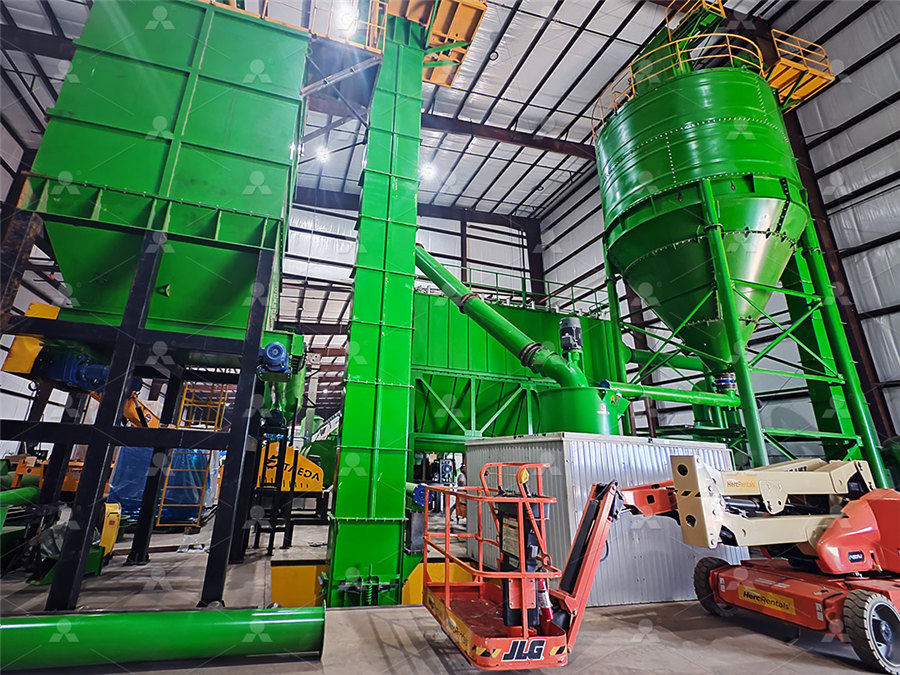
Iron Ore Beneficiation Plant, Iron Ore Magnetic Separation
1 The dump truck feeds the raw ore into the hopper and the vibrating feeder The vibrating feeder feeds evenly to the jaw crusher, which crushes large rocks to less than 200mm 2 The jaw crusher output is sent to the transfer bin through the belt conveyor, and an electromagnetic vibrating feeder is installed below it Convey the material less than 200mm to the first coarse Find innovative production technology for making powder and connect directly with worldleading specialists In manufacturing processes where precise and safe powder transfer is ess If your water treatment plant often facing difficulties with sewage sludge deposits, Powder Manufacturing Equipment Making2023年3月1日 Modeling and simulation of mechanical degradation of iron ore sinter in a complex transfer chute system using the discrete element model and a particle breakage model Author links open overlay panel Saprativ Basu a , Arijit Chakrabarty a , Samik Nag a , Pradeep Chaudhary a , Surajit Sinha a , Thrilok Jain b , Mohan S Nainegali b , Victor A Rodriguez c , Modeling and simulation of mechanical degradation of iron ore 2/97 Taconite Ore Processing 11231 1123 Taconite Ore Processing 11231 General1 The taconite ore processing industry produces usable concentrations of ironbearing material by removing nonferrous rock (gangue) from lowgrade ore The sixdigit Source Classification Code (SCC) for taconite ore processing is 3030231123 Taconite Ore Processing
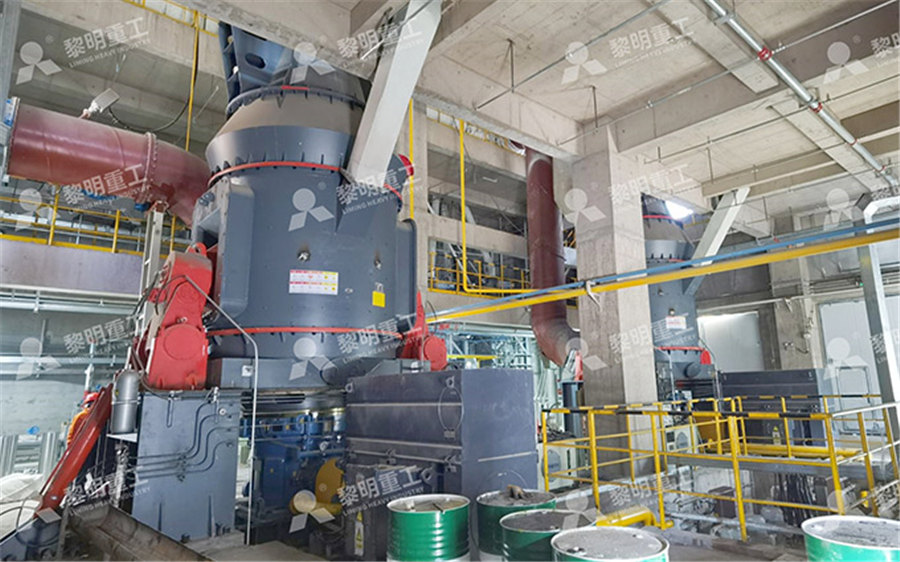
Iron Ore Powder at Best Price from Manufacturers TradeIndia
Find Iron Ore Powder manufacturers, Letter of Credit at Sight (Sight L/C), Cash Against Delivery (CAD), Cash Advance (CA), Telegraphic Transfer (T/T), Days after Acceptance (DA), Cash in Advance This powder is used in water treatment plants for removal of iron, manganese and fluorine from water We use air tight containers and materials process stages, the ore is exposed to a number of heat cycles, which lead to material oxidation35 Therefore, the pellets and the iron ore fines mainly consist of hematite (Fe 2O 3) by the end of their manufacturing process In this study, iron ore powder fines, collected from the iron ore pelletization process, with a size range between 10 Laserassisted reduction of iron ore using aluminum powder DiVAThe sinter plant turns iron ore into sinter, which is the optimal product for the blast furnace Sinter is made by burning a mix of iron ore powder, fluxes and recycled substances from the steel plant to create an opengrained, consistent substance The sinter is then crushed, cooled and screened for dust Sometimes, iron ore is supplied in the form of iron ore pelletsRaw materials Sinter plant ArcelorMittal2017年2月16日 Sintering is a thermal agglomeration process that is applied to a mixture of iron ore fines, recycled ironmaking products, fluxes, slagforming agents and solid fuel (coke)(PDF) Iron Ore Sintering: Process ResearchGate
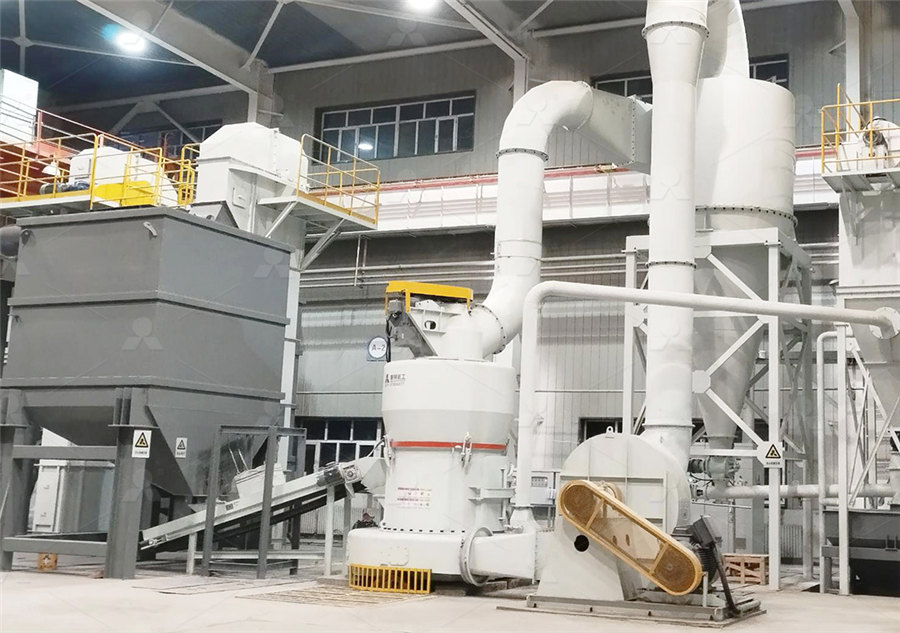
THE GROWING IMPORTANCE OF PELLETIZING FOR IRON ORE
2020年5月14日 The concentration of lowgrade iron ores is vital to the continued availability of iron and steel in our everyday lives (Eisele and Kawatra, 2003;Kawatra and Claremboux, 2021a;Zhang et al, 2021)2017年3月28日 Fig 1 Flow sheet of 6000 tons per day DIOS plant Process description DIOS process has the characteristics of (i) iron ore and coal fines can be directly used, (ii) there is no requirement of coke and hence there is no restriction on the kind of coal used in the process, (iii) process can be stopped and restarted easily and hence good flexibility and (iv) the intensity of Direct Iron Ore Smelting Process for Ironmaking – IspatGuru2024年2月15日 A typical transfer chute station that redirects the particle flow in a 90 ° corner is modeled based on the geometry in the work of Ilic [35], as shown in Fig 1 (ac) The transfer station has a total drop height of 55 meters The chute geometry is commonly divided into three dropping sections categorized by its purpose and drop heightUnrevealing energy dissipation during iron ore transfer through 2023年11月1日 The graded iron ore enters either the coke plant or the sinter plant A coke plant uses coal to heat the iron ore to 125⁰⁰c, and by removing oxygen, it results in pure ironSteel Manufacturing: From Iron Ore to Finished Product
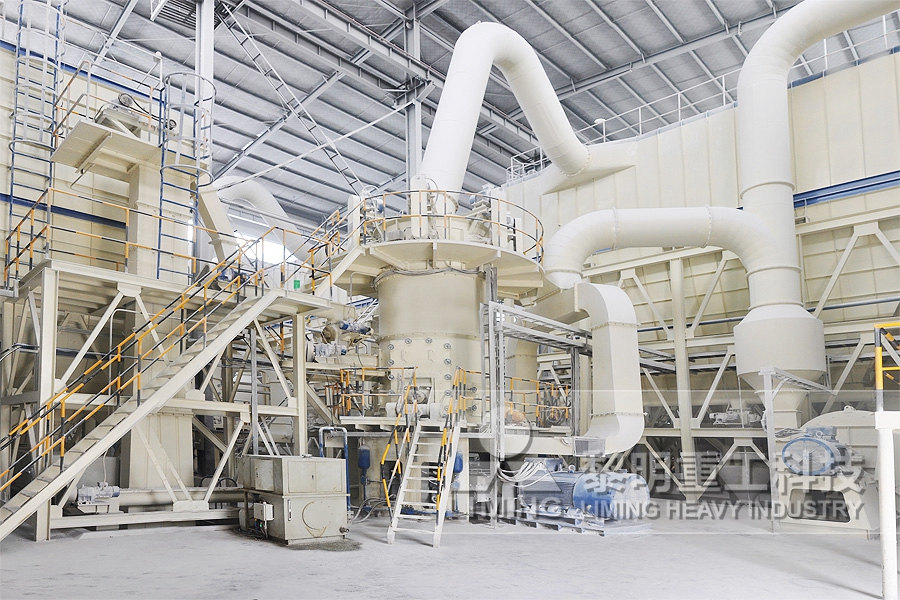
Effect of coal ash on ring behavior of ironore pellet powder in kiln
2017年10月1日 Bonding strength, microstructure and composition of coal ash, ironore pellet powder, and their mixed powder were investigated to analyze the effect of coal ash on ring behavior of pellet powder 2013年8月1日 PDF Sintering is a process by which a mixture of iron ores, fl uxes and coke is agglomerated in a sinter plant to manufacture a sinter product of a Find, read and cite all the research you (PDF) Iron ore sintering Part 1 Theory and practice of Laserassisted reduction of iron ore using aluminum powder Cite as: J Laser Appl 35, (2023); doi: 102351/7 View Online Export Citation CrossMarkLaserassisted reduction of iron ore using aluminum powder2024年1月21日 Please cite this article as: PJ Capdeville, S Kuang and A Yu, Unrevealing energy dissipation during iron ore transfer through chutes with different designs, Powder Technology (2023), https://doiUnrevealing energy dissipation during iron ore transfer through
.jpg)
Stone Dust Powder Processing Plant Conveyor System in Jamaica
Project Features 1 Typical mineral ore powder production and processing line model, strictly using national standards and meeting local environmental requirements; 2 Motor plus reducer drive, improve the efficiency of the conveyor system, reduce production costs, convenient and fast maintenance; 3 The program design and power calculation are accurate, and the overall 2019年10月1日 AbstractLoss on ignition (LOI) in the mineral represents the chemically bonded water which can be removed at high temperatures only High LOI in iron ore fines has an adverse affect during pellet induration process HighLOI iron ore fines are required for detailed laboratory pelletization studies and are used in pellet making The received iron ore is martite–goethitic Usage of HighLOI Iron Ore Fines in Pellet Making1 Feeding: The truck loads the raw material into the first vibrating feeder equipped with a 70mm mesh screen +70mm will be sent to the transfer bin by the 1st conveyor 2 Screening: 070mm materials will be sent to trommel screens with 8mm and 15mm screens for washing and separation The 08mm material will be sent to the vibrating screen with 2mm sieve for Tantalum Niobium Ore Process , Coltan Processing Plant JXSC 2022年2月23日 American food manufacturer The Kraft Heinz Co announced Wednesday that food and agribusiness firm JR Simplot Co will produce and supply products for Kraft’s OreIda brand under a longterm strategic supply agreement Simplot’s division Simplot Food Group will support the brand with its expertise in potato processing and distribution and supply it with Simplot Inks Deal to Produce OreIda Products for Kraft Heinz
.jpg)
Ora Organic Protein Powder Review: Is It Worth It? Vegan Foundry
Ora Organic’s protein powder costs $3999 and comes in 20 servings, which means that each serving costs $2, making it an expensive protein powder You can bring the price per serving down to $160 but you would have to subscribe to their recurring delivery service2019年9月15日 In high throughput Australian iron ore handling operations, premature failure of conveyor belts and transfer chutes due to wear is of great significance to the success of operations Here, a down time in the order of a few hours may result in millions of tonnes of annual export losses Optimisation of existing or brownfield high capacity and utilisation mine, Development of design criteria for reducing wear in iron ore transfer 4 天之前 Copper industrial minerals include: natural copper, chalcopyrite, chalcocite, tetrahedrite, azurite, malachite, etc Chalcopyrite (a compound of copper, sulfur, and iron) is mined mainly, followed by chalcocite and bornite If Copper Ore Processing Plants, Flow And Equipment2015年6月11日 Powder transfer via vacuum offers a solution by providing a contained environment for transport, thereby reducing explosion risk and cutting back on product waste Some vacuum conveying systems offer the additional Contained Powder Transfer: VacuumBased
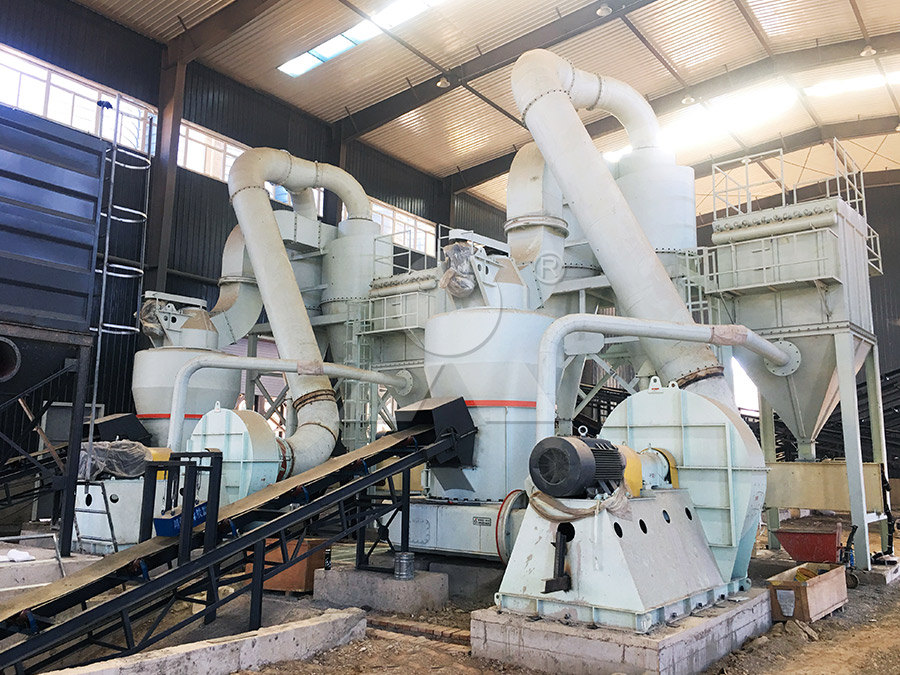
Direct reduction of ironore with hydrogen in fluidized beds: A
2024年4月1日 As a typical nonblast furnace ironmaking method, fluidized ironmaking directly uses pulverized ore as raw material, which eliminates the process of pelletizing and sintering and helps to realize the efficient utilization of lowgrade complex iron ore [8]The direct reduction of iron ore in fluidized beds is a promising method for iron making because of its high heat and 2019年12月24日 Energy Resources, Its Role and Use in Metallurgical Industries RC Gupta, in Treatise on Process Metallurgy: Industrial Processes, 2014 423132 Sinter Making The iron ore fines (− 10 mm) are agglomerated using Dwight Lloyed sintering machine The iron ore fines and coke breeze fines mix with moisture is fed on the sinter bed which is ignited by a gas Sintered Ore an overview ScienceDirect Topics2023年3月1日 Basu et al analyzed the breakage process of iron ore in transfer chute system using DEM and Tavares UFRJ model, and the breakage particle size of iron ore was calculated in different stage (Basu et al, 2023) The advantage of the Tavares UFRJ model is that it can directly calculate the particle size distribution of fragmentsModeling and simulation of mechanical degradation of iron ore Mix dry chrome powder, suitable binders (such as molasses) and lime powder Send the mixture into the chrome ore briquetting machine Finally, the entire chrome ore powder briquette production line feeds smoothly and evenly The workload of the briquetting machine is stable and the production efficiency is high, which solves the problem of the Iron Powder Briquetting Machine Fote Machinery
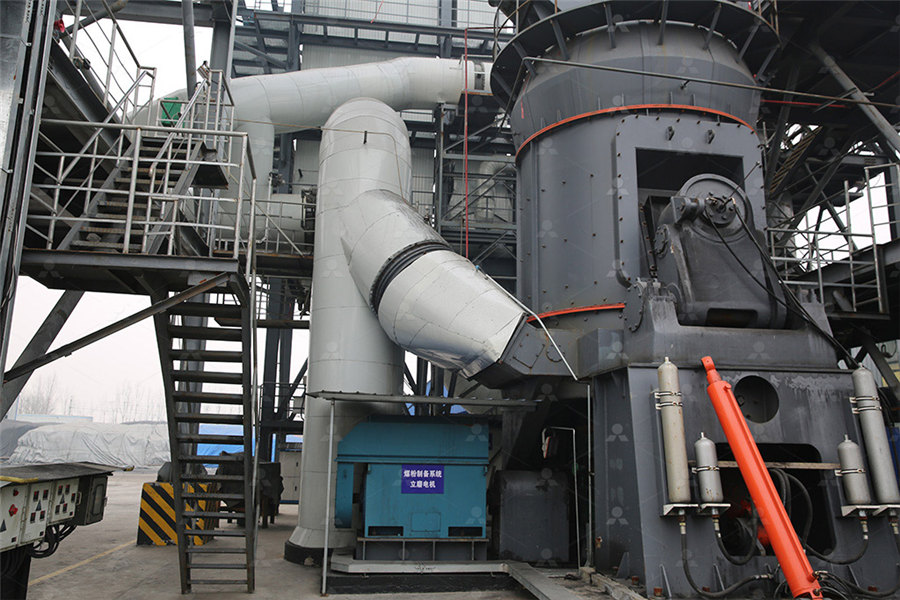
Application of deep learning in iron ore sintering process: a review
2024年3月16日 The sintering process is an intricate system with a protracted process flow The steps in the manufacturing line are primarily composed of the ingredients and mixing process, the sintering operation process, and the treatment of the sintered ore [39, 40]22 Important parameters and characteristics of sintering process As shown in Fig 2, all variables affecting 1 The dump truck feeds the raw ore into the hopper and the vibrating feeder The vibrating feeder feeds evenly to the jaw crusher, which crushes large rocks to less than 200mm 2 The jaw crusher output is sent to the transfer bin through the belt conveyor, and an electromagnetic vibrating feeder is installed below it Convey the material less than 200mm to the first coarse Iron Ore Beneficiation Plant, Iron Ore Magnetic Separation Find innovative production technology for making powder and connect directly with worldleading specialists In manufacturing processes where precise and safe powder transfer is ess If your water treatment plant often facing difficulties with sewage sludge deposits, Powder Manufacturing Equipment Making