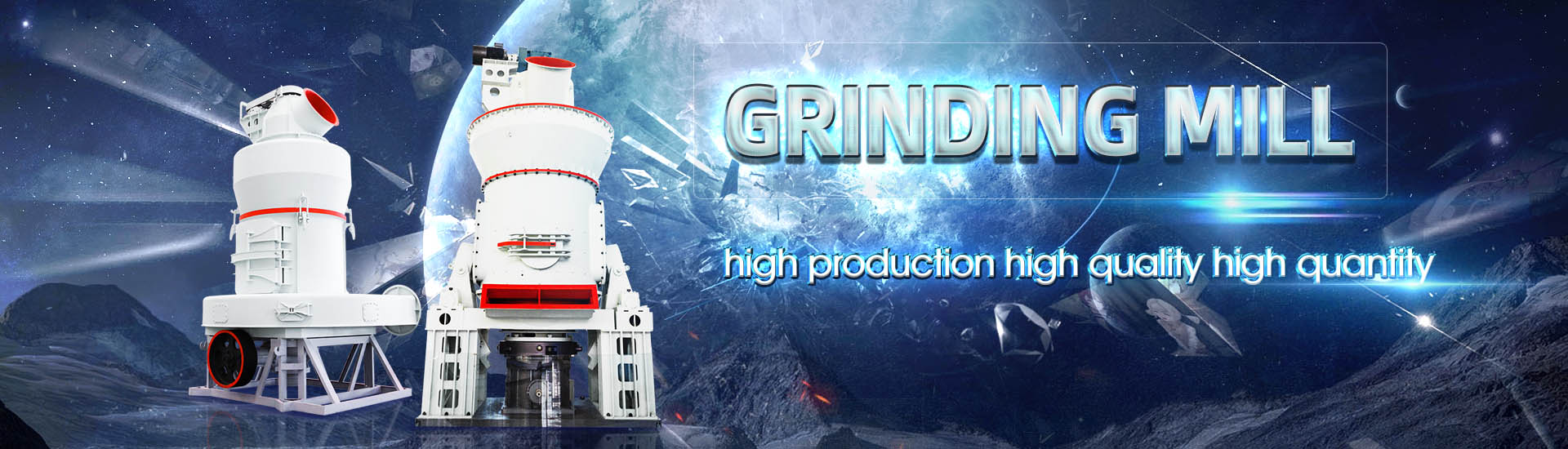
Silica powder processing process flow
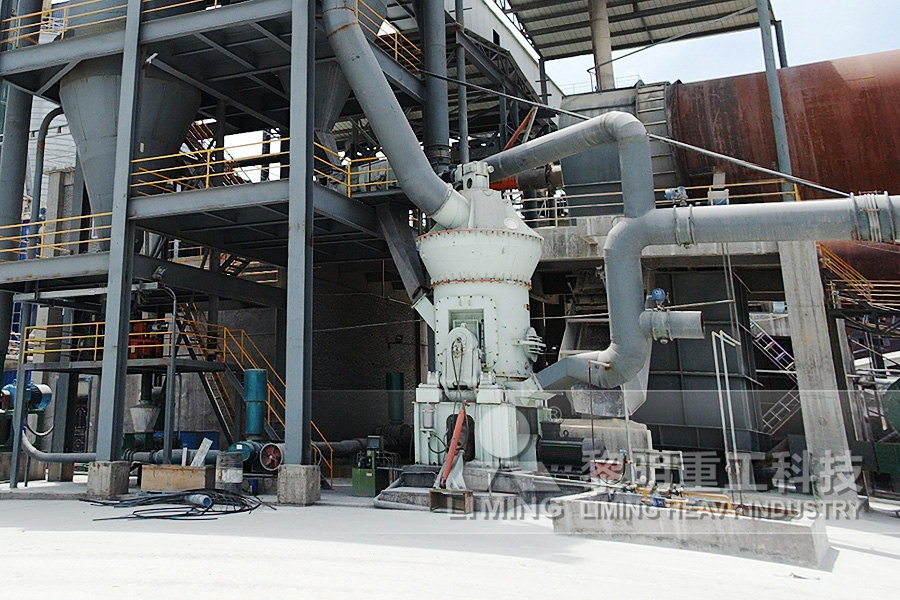
Analysis of silica production and drying processes IOSR Journals
In the production of silica by precipitation and dissociation, drying is an essential part of the process, and the design of a reasonable silica drying method is essential to improve the production efficiency and economic effectiveness of silica2023年6月1日 A magnetically assisted impaction coater and a hybridizer have also been to coat cohesive cornstarch powder with silica particles to improve the powder flow The Hosokawa A concise summary of powder processing methodologies for flow Modifying silica particles via exsitu involves two separate steps: forming porous silica particles with sodium lauryl sulfate (SLS) as a template and impregnation using ultrasound assistanceFlow chart showing the processing steps for the cubic The process consists of two primary batch unit operations for processing Silica powder: (1) a Pfaudler glass lined stirred tank reactor with a refluxing condenser where the Silica is reacted Silica Powder Production Process Review, Documentation,
.jpg)
Effects of fumed silica flow aids on flowability and packing of
2021年12月15日 Results show that the mixing process for flow aids and powders has significant influence on the improvements Moreover, the amount of aerosil is a key criterion for optimized 2019年2月10日 The mechanism of colloidal silica action to improve flow properties of pharmaceutical powders is known to be based on interparticle force disruption by silica On the mechanism of colloidal silica action to improve flow In this paper, we identify the (I) characteristics of silica (II) optimum silica for API, and (III) appropriate silica for direct compression vehiclesImproving Powder Flow Properties of a Direct Compression 44FP silica to prevent caking and segregation during blending and processing SYLOID® 244FP silica adsorbs the right amount of moisture to create a freeflowing powder mixture, while the SYLOID FP Silica Pharmaceutical Excipients Solving Flow and
.jpg)
Migration and deposition behavior of silica powder in saturated
2022年8月2日 To explore the effects of temperature and percolation velocity on the migration and deposition characteristics of different silica powder in saturated porous media under 2020年10月14日 Fumed silica is one of the most commonly used flow additives in the powder coating industry To investigate the influence of the properties of fumed silica on powder coatings, three different types of fumed silica, Aerosil Investigation of the Performance of Fumed Silica as 2019年8月14日 The effect of admixing fumed silica particles on the flow behavior of the PEEK powder was analyzed by degree of coverage tests to improve the powder deposition process via doctor blade(PDF) Impact of Flow Aid on the Flowability and2011年11月1日 Request PDF Profoundly Improving Flow Properties of a Cohesive Cellulose Powder by Surface Coating with Nanosilica Through Comilling Poor flow properties hinder the easy handling of powders Profoundly Improving Flow Properties of a Cohesive Cellulose Powder
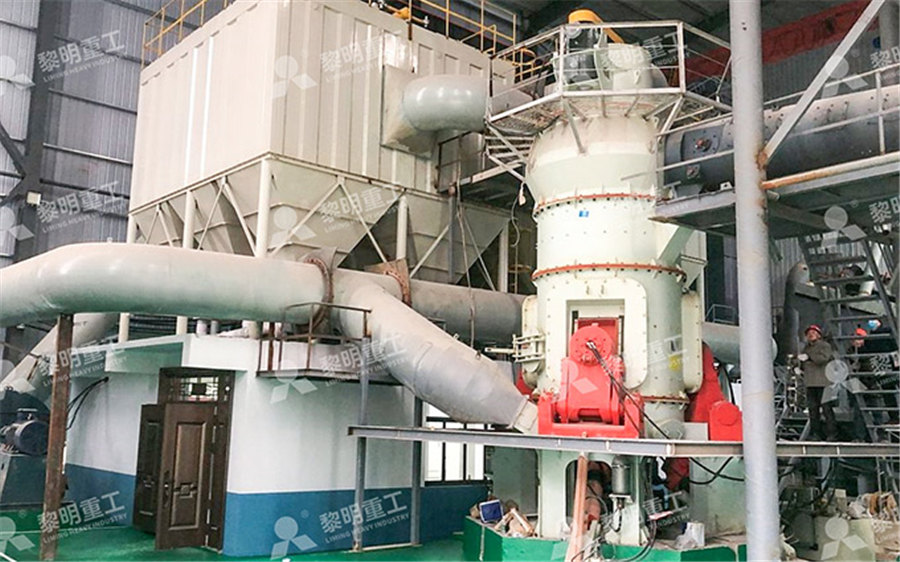
A concise summary of powder processing
The knowledge of powder properties has been highlighted since the 19th century since most formulations focus on solid dosage forms, and powder flow is essential for various manufacturing operations A poor powder flow may So before using silica in the carboreduction process, it must be enriched for eliminating the impurities [1] 2 Several studies have been carried out to obtain high purity silica by eliminating Quartz mining and processing flow chart at selected deposits 2019年8月26日 Zircon processing description from its geology mineral property to how to extract mineral from rock and placer deposit, related processing plant flow chart and layout designZircon Processing Equipment, Process Flow, Cases JXSC Therefore, unfavorable powder flow is the fundamental and serious bottleneck to be first eliminated in the direct compression processing Glidants are usually incorporated in direct compression formulations to improve powder flow and control tablet weight Specifically, silica has been reported to be the mostImproving Powder Flow Properties of a Direct Compression
.jpg)
Powder Processing an overview ScienceDirect Topics
Production equipment and tooling selection Peter Scallan, in Process Planning, 2003 Powder processing The steps involved in powder processing were previously described in Section 4103 and these are powder blending, compacting, sintering and finally secondary processing In terms of equipment, the compacting requires a press that can deliver forces in the region of 10–17 2021年3月15日 Consequently, powder flow characterization using image analysis technologies demonstrated to be an additional tool in pharmaceutical tablet manufacture to predict inprocess performance and to detect flow problems before the powder Effect of colloidal silicon dioxide and moisture on powder flow 2021年3月1日 This paper describes the laser powder bed fusion of a soda lime silica glass Optimisation of the laser powder bed fusion process was undertaken and the physical and mechanical properties of the manufactured parts were characterised revealing an average porosity of 12%, a mean flexural strength of 65 MPa and a fully amorphous structureLaser powder bed fusion of soda lime silica glass: Optimisation of 2015年2月28日 Powder properties However, where powders must be moved efficiently, properties can be evoked that offer particular benefits In such applications, the powder is moved by making it "flow like a liquid," using air to fluidize the powder The materials involved are of high uniform porosity, minimizing energy required to make the powder flowSome recent fluidization developments in powder handling
.jpg)
The Importance Of Powder Flow Characterization
What Is Powder Flow? Powder flow, also known as flowability, is defined as the relative movement of a bulk of particles among neighboring particles or along the container wall surface [1] In other words, powder flowability refers to the 2018年5月16日 Silica sand, also known as quartz sand, is mainly composed of silica( SiO2), which is the main raw material for making glassSilica sand has ordinary silica sand, refined silica sand and high purity silica sand The How to Process Silica Sand? JXSC Machine2020年7月17日 To get the controlled size and monodispersed silica nanoparticle is a popular topic since its broad applications are in a lot of fields such as biological medicine, military project, catalyst, and chip industry The Stöber process was often used to prepare silica nanoparticle because of its low cost and easy operation Here, the combined method of microchannel and The combined method to synthesis silica nanoparticle by Stöber process Poor flow properties hinder the easy handling of powders during industrial‐scale processing In this work, we show that powder flow can be substantially improved by reducing the cohesion of powders by coating them with nanosized guest particles We further show that comilling is an efficient process for nanocoating We have systematically investigated the effects of total Profoundly improving flow properties of a cohesive cellulose powder
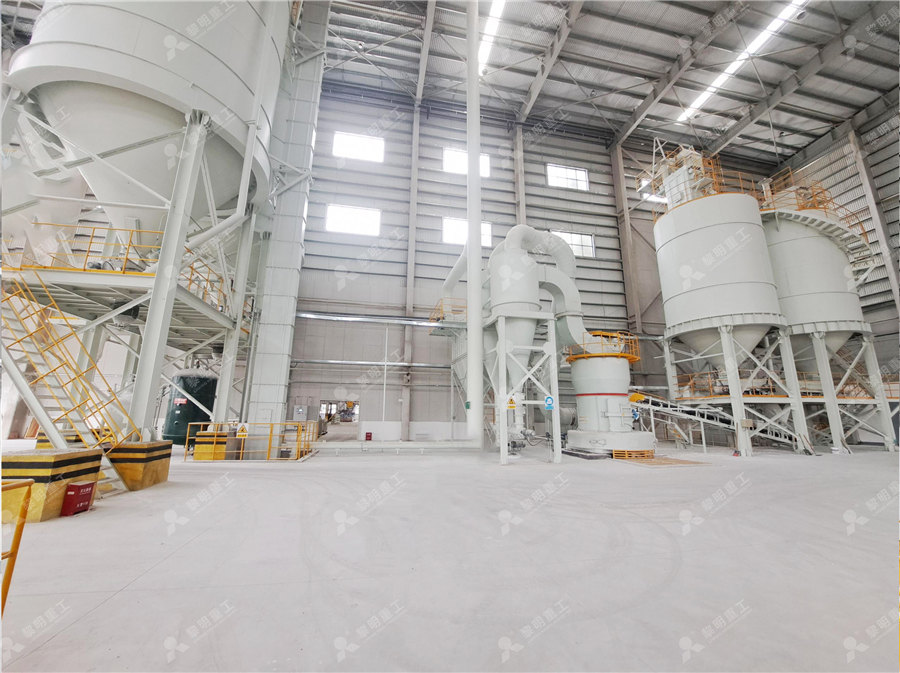
Kaolinite Processing Equipment, Process Flow, Cases JXSC
2019年8月23日 The wet process includes three stages of ore preparation, ore beneficiation processing and product processing The beneficiation stage may include hydraulic grading, flotation, selective flocculation, magnetic separation, chemical treatment (bleaching), etc to remove different impurities The prepared slurry pulp is first desanded by the rake type Precipitated silica products encapsulate powder particles and absorb ambient liquids, The ability to prevent clumping makes precipitated silica useful for: Freeflow of granulated and powdered foods such as table salt animal feed nutrients and industrial additives in process machinery, such as conveyors and drying, mixing and screening Anti Caking Agent PPG Silica Products2005年5月1日 Request PDF Dry Powder Processing of Fibrous Fumed Silica Compacts for Thermal Insulation This study proposes a new dry powder processing method to produce fiber reinforced fumed silica Dry Powder Processing of Fibrous Fumed Silica Compacts for The Bayer process is a chemical process for refining aluminium hydroxide, Al(OH) 3 from bauxite; this aluminium hydroxide is subsequently calcined to produce alumina, Al 2 O 3The basis of the Bayer process is an understanding of the characteristics of the sodiumhydroxide—sodiumaluminate solution relationship, namely its ability to keep sodiumaluminate in a dissolved state Chemical Processing of Bauxite: Alumina and Silica
.jpg)
Fumed Silica ‐ Production, Properties, and Applications
2008年4月1日 These characteristics enable fumed silica to act as a free flow additive in powderlike solids, as a thickener in various liquids and as a powerful reinforcing filler in elastomers2023年3月21日 In Figure 1, the pure flowing agents and wheat flour are shown in the flow function of the shear cell powder flow tester and it can be seen that TCP 3 is more cohesive than the rest This was also noticeable when working with the dust, where it often seemed to stick to walls, watch glasses, etcSilica Alternatives, Are They Viable? • BulkInside2011年11月1日 The small particle size of Avicel PH105 (d 10 = 68 ± 01 μm, d 50 = 209 ± 01 μm, and d 90 = 457 ± 05 μm; n = 3) is consistent with its high cohesiveness and poor flow propertiesThe particle size increases slightly for Avicel PH105 coated with 1% silica after 40 comilling cycles, which can be attributed to the deposition of nanoparticles on the surfaces of Profoundly improving flow properties of a cohesive cellulose powder 2019年2月10日 Since the Quality by Design (QbD) concept is ever more emphasized in pharmaceutical process development, recent studies address not only the sole fact of glidant use to design successful formulation, but more general aspects of glidant interaction with the powder and its action to improve the flow properties thereof, are the objects of interest On the mechanism of colloidal silica action to improve flow
.jpg)
Laser powder bed fusion of soda lime silica glass: Optimisation of
Laser powder bed fusion of soda lime silica glass: Optimisation of processing parameters and evaluation of part properties KC Datsiou a, 1 , F Spirrett a , I Ashcroft a , M Magallanes b , S 1999年9月28日 In this article, a leaching study, carried out on a quartz sample to obtain highpurity silica sands, has been presented A leaching process by using oxalic acid to remove low iron content from the ore under study and to obtain a material suitable for fiber optic production has been evaluated A characterization study has been carried out to establish the location of Iron Removal Process for HighPurity Silica Sands Production by −Ease of processing Powder Coating Summit September 23, 2021 Novel Synthetic Silica for Matting Powder Coatings 6 Formulation and Process Parameters Flow aid Acrylic polymer on silica carrier 10 Degassing Benzoin 05 Carbon black Carbon black pellets 10Novel Synthetic Silica for Matting Powder Coatings PCI Mag2020年10月14日 Fumed silica is one of the most commonly used flow additives in the powder coating industry To investigate the influence of the properties of fumed silica on powder coatings, three different types of fumed silica, Aerosil R812, R972, and R8200, were selected and introduced to an ultrahighgloss powder paint by the dryblending method with preset mixing Investigation of the Performance of Fumed Silica as Flow
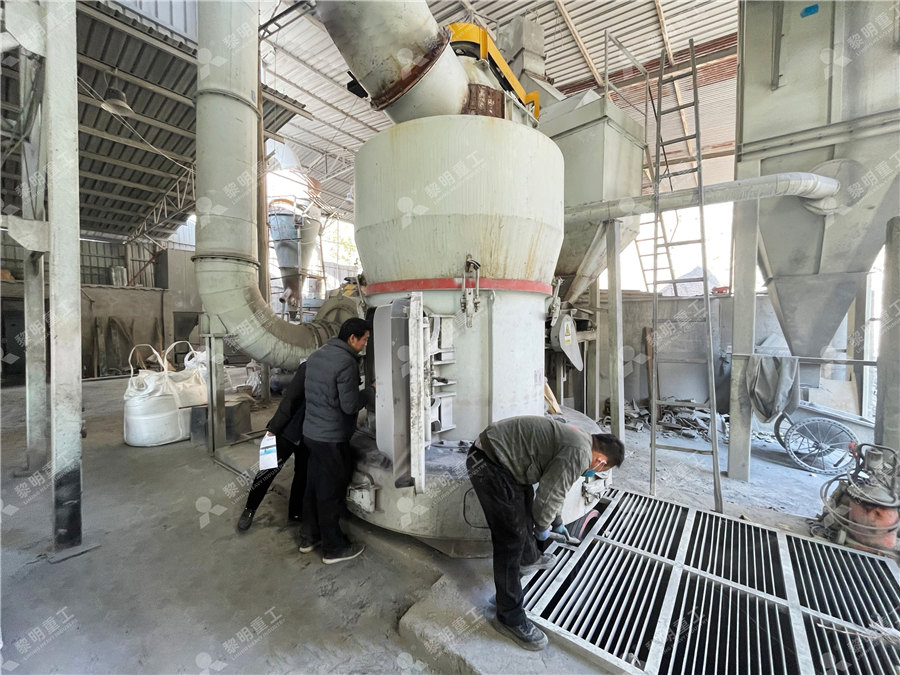
USB2 Process for treating synthetic silica powder and
A process for producing a synthetic quartz glass powder which is substantially free of carbon contaminant, for reduced bubble density and improved stability of articles made from the synthetic quartz glass during fusion molding by maintaining the synthetic silica powder in an oxidizing environment, eg, an atmosphere comprising at least 3 vol % ozone at a temperature of less SILICA POWDER PROCESSING OF BALL MILL AND AIR CLASSIFIER The silica powder produced by this production process has high purity, and its particle size can be controlled flexibly according to user requirements The added value is high, but this process required high energy consumptionSilica Powder Processing TechnologyALPA POWDERIn addition, for one pilot scale dry sizing process, PROCESS was contracted to document the design of the existing “as built” process and conduct a process design and safety review of this process The set of silica powder dry processing equipment consists of: the pilot scale Dry Sizing (DS) unit, a 30 inch diameter SWECO vibratory screener Silica Powders Lab and Pilot Process Design Safety Review2020年7月30日 The mechanism of droplet formation from the molten metal depends on the powder characteristics: size, shape, and structure; process parameters: molten metal properties (composition, viscosity, and surface tension), molten metal flow properties (flow path, flow rate, and flow length); type of disintegration process: melt drop process driven by capillary forces, Nanomaterials through Powder Metallurgy: Production, Processing
.jpg)
(PDF) Impact of Flow Aid on the Flowability and
2019年8月14日 The effect of admixing fumed silica particles on the flow behavior of the PEEK powder was analyzed by degree of coverage tests to improve the powder deposition process via doctor blade2011年11月1日 Request PDF Profoundly Improving Flow Properties of a Cohesive Cellulose Powder by Surface Coating with Nanosilica Through Comilling Poor flow properties hinder the easy handling of powders Profoundly Improving Flow Properties of a Cohesive Cellulose Powder The knowledge of powder properties has been highlighted since the 19th century since most formulations focus on solid dosage forms, and powder flow is essential for various manufacturing operations A poor powder flow may A concise summary of powder processing So before using silica in the carboreduction process, it must be enriched for eliminating the impurities [1] 2 Several studies have been carried out to obtain high purity silica by eliminating Quartz mining and processing flow chart at selected deposits
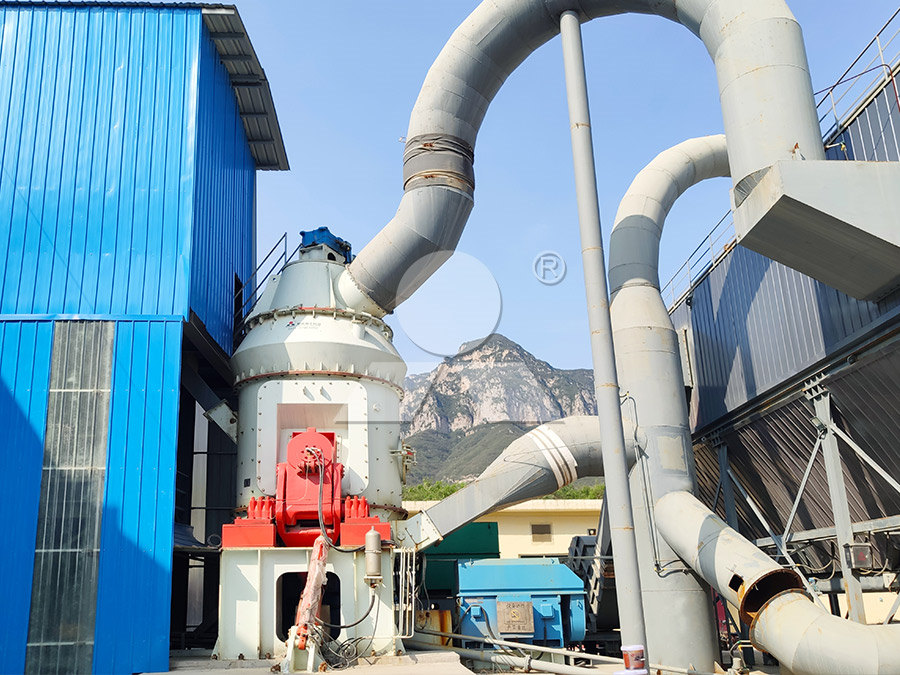
Zircon Processing Equipment, Process Flow, Cases JXSC
2019年8月26日 Zircon processing description from its geology mineral property to how to extract mineral from rock and placer deposit, related processing plant flow chart and layout designTherefore, unfavorable powder flow is the fundamental and serious bottleneck to be first eliminated in the direct compression processing Glidants are usually incorporated in direct compression formulations to improve powder flow and control tablet weight Specifically, silica has been reported to be the mostImproving Powder Flow Properties of a Direct Compression Production equipment and tooling selection Peter Scallan, in Process Planning, 2003 Powder processing The steps involved in powder processing were previously described in Section 4103 and these are powder blending, compacting, sintering and finally secondary processing In terms of equipment, the compacting requires a press that can deliver forces in the region of 10–17 Powder Processing an overview ScienceDirect Topics2021年3月15日 Consequently, powder flow characterization using image analysis technologies demonstrated to be an additional tool in pharmaceutical tablet manufacture to predict inprocess performance and to detect flow problems before the powder Effect of colloidal silicon dioxide and moisture on powder flow
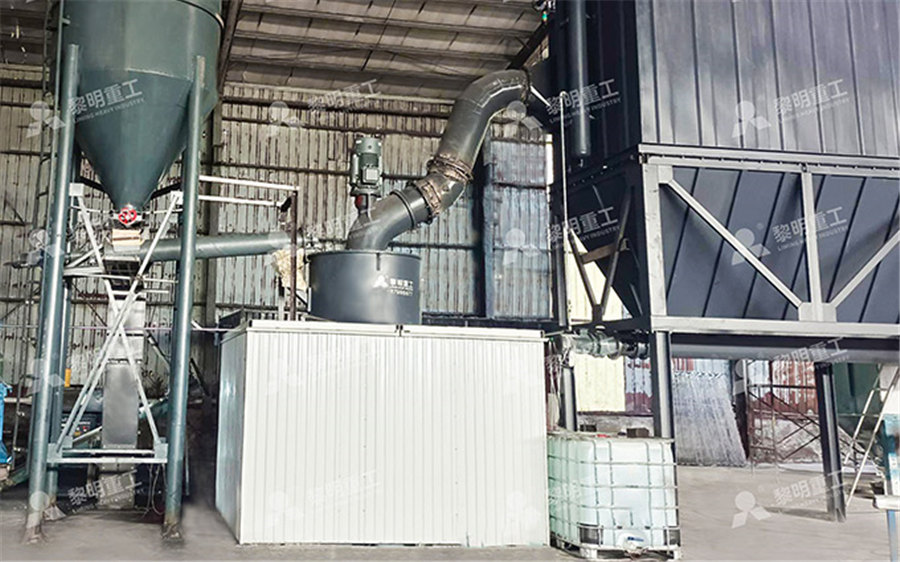
Laser powder bed fusion of soda lime silica glass: Optimisation of
2021年3月1日 This paper describes the laser powder bed fusion of a soda lime silica glass Optimisation of the laser powder bed fusion process was undertaken and the physical and mechanical properties of the manufactured parts were characterised revealing an average porosity of 12%, a mean flexural strength of 65 MPa and a fully amorphous structure2015年2月28日 Powder properties However, where powders must be moved efficiently, properties can be evoked that offer particular benefits In such applications, the powder is moved by making it "flow like a liquid," using air to fluidize the powder The materials involved are of high uniform porosity, minimizing energy required to make the powder flowSome recent fluidization developments in powder handling