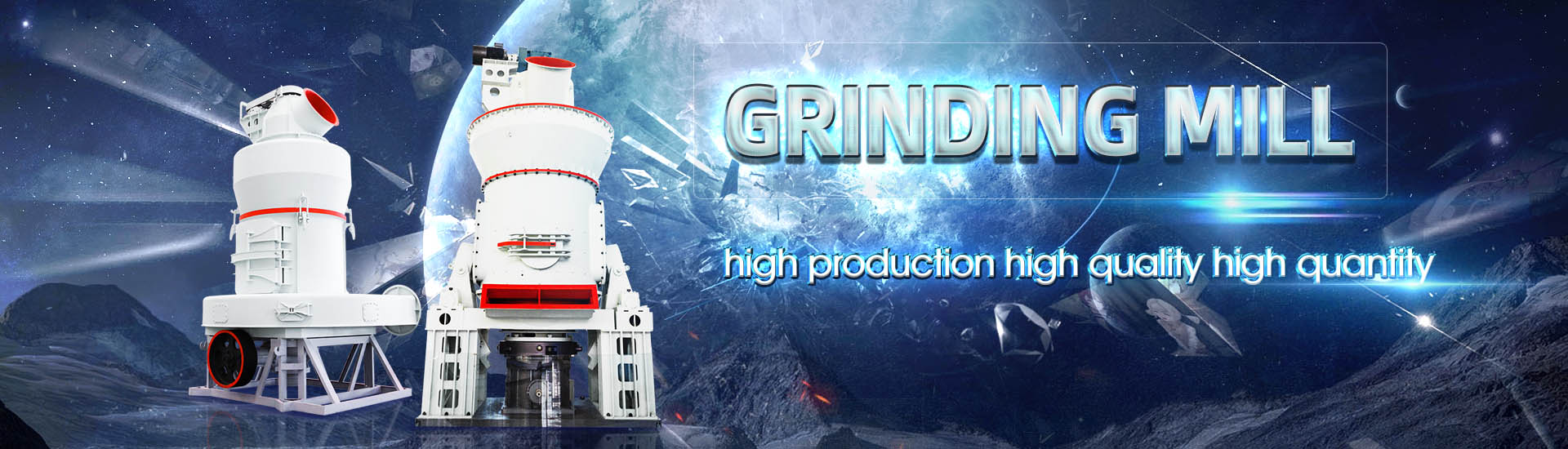
Ultrafine zirconia injection molding
.jpg)
Injection molding of ultrafine zirconia (YTZP) powders KCI
Injection moldings of three types of ultrafine zirconia powder were investigated It was demonstrated that powder characteristics involving particle size, particle size distribution, 1995年1月1日 Injection moulded components and test bars were prepared from three zirconia powders with specific surface areas of 22, 7 and 4 m 2 g −1 at 50–60 vol% ceramic The The injection moulding of fine and ultrafine zirconia powders2006年1月1日 Injection moldings of three types of ultrafine zirconia powder were investigated It was demonstrated that powder characteristics involving particle size, particleInjection molding of ultrafine zirconia (YTZP) powders1995年1月1日 Micro Ceramic Injection Molding (μCIM) is a near netshape process to produce smaller and intricate parts at a competitive cost The application of nanosized ceramic powder The injection moulding of fine and ultrafine zirconia powders
.jpg)
The effect of organic vehicle on the injection molding of ultrafine
2005年2月1日 The results indicate that DBP and SA were more suitable for the injection mold of the mixtures containing PW PP, EVA and ultrafine zirconia powder Increasing the content of It is shown that chemically derived ultrafine zirconia powders (mean particle size ≤100 nm) can be processed at up to 60 vol % in a wax‐based organic vehicle by the selection of suitable The injection moulding of fine and ultrafine zirconia powders2005年2月1日 This study aimed to fabricate zirconiaalumina composites via powder injection molding and investigated the effects of alumina addition on microstructure as well as physical The Effect of Organic Vehicle on the Injection Molding of Ultra Using ultrafine ceramic powders (eg zirconia) and highquality LIGA mould inserts, surface qualities of R a = 40 nm or R max ≤ 3 mm could be obtainedMicro powderinjection moulding of metals and ceramics

Injection moulding of zirconia (YTZP) ceramics
Ceramic injection molding is a nearnet shapeprocessing technique, producing ceramic components with low tooling costs and complex shapes In this paper, ZrO2 ceramics with 2005年2月1日 With respect to polymerfiller composite (feedstock) development for the different variants of powder injection molding the use of dispersants or surfactants is essential for a The effect of organic vehicle on the injection molding of ultrafine Metal Injection Molding The Metal Injection Molding (MIM) process uses Ultra Fine metal powders and plastic binders to cost effectively produce small, complex parts for a wide variety of applications including aerospace, automotive, consumer goods, dental tools, firearms, and medical devicesMetal Injection Molding Ultra Fine2021年3月28日 The injection molding was done at 190℃ followed by water debinding of PEG at 40℃ Powder injection molding of zirconia [1321] have been explore d in a numbe r of s tudies(PDF) Microstructure and properties of zirconia
.jpg)
Zhejiang Jinkun Zirconia lndustry Co,Ltd
Zhejiang Jinkun Zirconia lndustry Co,Ltd The main products JK3YZN, JKYDENTAL are suitable for pressing molding,injection molding,isostatic pressing molding,casting molding and extrusion molding The products satisfy the different needs of 2004年11月1日 The procedures of ceramic injection molding (CIM) include four steps: kneading process, injection molding, debinding, and sintering[1], [2], [3] The CIM technology offers the opportunity to make complex and nearnetshape of ceramic parts The kneading process is an important step in ceramic injection moldingKneading behaviour and homogeneity of zirconia feedstocks for 2015年6月1日 The ceramic injection molding technique was used in the gaspressure sintering of ultrafine Si3N4 powder The feedstock’s flowability, debinding rate, defect evolution, and microstructural Injection molding of ultrafine Si3N4 powder for gasInjection molding of ultrafine zirconia (YTZP) powders Jiesheng Luoa, Zhongzhou Yib, Bing Xiaoc, Yan Gaoa, Zhipeng Xiea,*, Jianbao Lia and Yong Huanga a Department of Materials Science Engineering, Tsinghua University, Beijing, , China b Chemistry Department of Honghe University, Yunnan , China c Zhongyuan Engineering College, Zhengzhou JCPR
.jpg)
Twostage sintering of nanosized yttria stabilized zirconia
2007年10月1日 The effect of organic vehicle on the injection molding of ultrafine zirconia powders Mater Des, 26 (2005), pp 7982 View PDF View article View in Scopus Google Scholar [8] Grain growth in ultrafinegrained YTZP ceramics J Eur Ceram Soc, 17 (1997), pp 11331141 View PDF View article View in Scopus Google ScholarDespite its unique high efficiency and good environmental compatibility, the watersoluble binder system still encounters problems achieving a desired sintered part via ceramic injection molding because of the poor compatibility and the powderbinder A strategy to obtain a highdensity and highstrength zirconia 2004年11月1日 The procedures of ceramic injection molding (CIM) include four steps: kneading process, injection molding, debinding, and sintering [1], [2], [3] The CIM technology offers the opportunity to make complex and nearnetshape of ceramic parts The kneading process is an important step in ceramic injection moldingKneading behaviour and homogeneity of zirconia feedstocks for 2007年10月1日 Powder injection moulding (PIM) is capable of mass producing intricately shaped components In recent years, this technology has been adopted in the electronic, computer, chemical and medical industries The 3 mol% yttria stabilized zirconia (YTZP) is well recognised for its high fracture toughnessPIM of nanosized YTZP hence offer attractive Twostage sintering of nanosized yttria stabilized zirconia
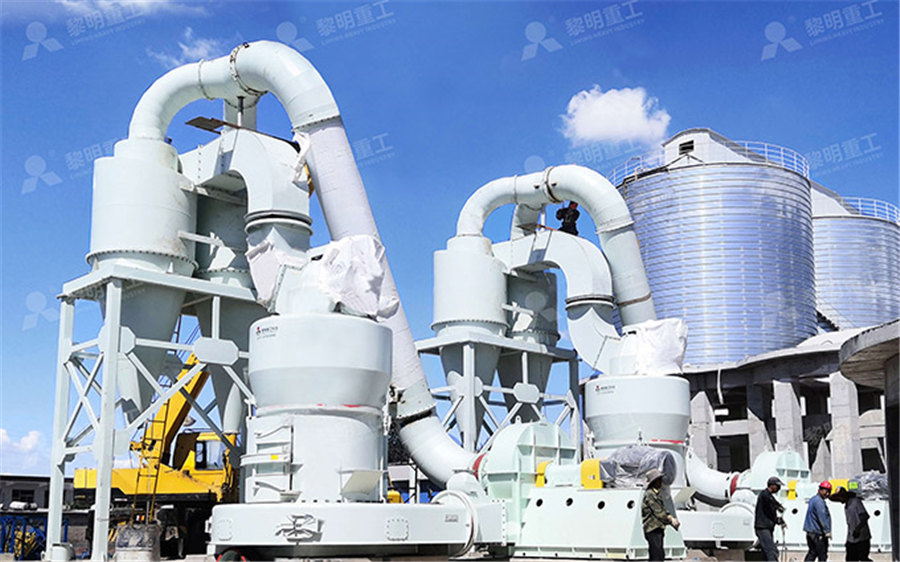
The effect of organic vehicle on the injection molding of ultrafine
2005年2月1日 Zirconia powders used for engineering ceramics are usually in the nanometer or submicrometer range, and have a narrow size distribution Compounds of such fine zirconia and polyolefin lack appropriate fluidity, which causes considerable difficulties in injection moulding [6]Yu et al carried out a microinjection molding test of zirconia microgears to obtain a zirconia microgear with good performance [40,41] Piotter et al [ 42 ] and Gietzelt et al [ 43 ] successfully produced highprecision ZrO 2 screws and microgear pumps with a threedimensional thread structure, which opened up a wider application space for micropowder injection molding ZrO 2 Fabrication of MicroParts with HighAspect Ratio MicroHole 2022年11月1日 In the present study, zirconia toughened alumina (ZTA) for orthopaedic implants has been developed by Ceramic Injection Molding (CIM) process Microstructural, mechanical and tribological studies have been carried out to establish whether the Mechanical and tribological properties of injection molded zirconia 2020年5月1日 DOI: 101111/IJAC13349 Corpus ID: ; Theory and practice of rapid and safe thermal debinding in ceramic injection molding @article{Xie2020TheoryAP, title={Theory and practice of rapid and safe thermal debinding in ceramic injection molding}, author={Hehan Xie and Jie Jiang and Xian Feng Yang and Qinglong He and Zhe Zhou and Xiewen Xu and Li Theory and practice of rapid and safe thermal debinding in
.jpg)
Injection moulding of zirconia (YTZP) ceramics ScienceDirect
1993年1月1日 Compared to normally continuous sintering at 1500 °C for 30 min, a novel twostage sintering by firing the sample at 1500 °C for 5 min and then rapidly cooling down to 1300 °C for 10 h was proposed to investigate sintering behavior and mechanical strength of injectionmolded yttriastabilized zirconia (Z3Y)The injectionmolded Z3Y feedstocks were prepared Injection molding is a kind of plasticity shaping technique that utilizes binder, plasticizer, lubricant, and a coupling agent 27) Injection molding is suitable for making fine ceramics, and the products shaped by this technique are highly precise and of good quality for clinical application, requiring little or no modification 28)Comparison of periimplant bone formation around injection 2017年5月28日 Despite its unique high efficiency and good environmental compatibility, the watersoluble binder system still encounters problems achieving a desired sintered part via ceramic injection molding because of the poor compatibility and the powderbinder segregation between ceramic powders and binders The objective of this study was to obtain a sintered A strategy to obtain a highdensity and highstrength zirconia 2011年8月21日 Microstructure of 48haged injectionmolded unstabilized ZTA10 pressurelesssintered at 1500 °C/1 h, thermally etched 1350°/05 h Ageing Behavior of InjectionMolded ZTA Ceramics as a Function
.jpg)
The injection moulding of fine and ultrafine zirconia powders
1995年1月1日 Ceramics International 21 (1995) 325333 The Injection Moulding of Fine and Ultrafine Zirconia Powders J H Song J R G Evans Department of Materials Technology, Brunei University, Uxbridge, Middlesex, UB8 3PH, UK (Received 16 November 1994; accepted 29 January 1995) Abstract: Injection moulded components and test bars were prepared from Ceramic Injection Molding (CIM) Zirconia (ZrO2) parts demonstrate a hardness of 85 HRA, highlighting their exceptional resistance to wear and abrasion The high hardness level ensures prolonged service life and minimized material degradation It makes them wellsuited for applications exposed to wear and abrasion, such as in bearings and sealsZirconia (ZrO2)2000年6月1日 For the preparation of injection moulded specimens, yttriastabilized tetragonal zirconia powder TZ3YS (Tosoh Corp, Japan) was used, which contained 52 wt% of Y 2 O 3According to the manufacturer the size of crystallites was 36 nm and the specific surface was 64 m 2 /g The ceramic suspension was formed using a binder containing type Elvax 250 Effect of powder treatment on injection moulded zirconia ceramics2013年6月1日 Ceramic International, 1995, 21: 325 333 [14] SONG J H, EVANS J R G Ultrafine ceramic powder injection molding: the role of dispersants [J] Journal of Rheology, 1996, 40(1): 131 152 [15] XIE Z P, LUO J S, WANG X, LI J B, HUANG Y The effect of organic vehicles on the injection molding of ultrafine zirconia powders [J]Influence of surfactant addition on rheological behaviors of injection
.jpg)
Binder Removal from Injection Molded Zirconia Ceramics
2004年5月1日 Binder removal characteristics of injection molded zirconia (ZrO2) ceramics in the form of oneclosed end tubes were studied by thermal analysis methods such as thermogravimetry and calorimetry2001年12月31日 Request PDF NearNetShape Forming of Zirconia Optical Sleeves by Ceramics Injection Molding Conventional sleeve blanks are currently produced by extrusion, which causes large dimension NearNetShape Forming of Zirconia Optical Sleeves by Ceramics DOI: 101016/JCERAMINT201305134 Corpus ID: ; Fabrication of zirconiatoughened alumina parts by powder injection molding process: Optimized processing parameters @article{Ani2014FabricationOZ, title={Fabrication of zirconiatoughened alumina parts by powder injection molding process: Optimized processing parameters}, author={Sarizal Md Ani and Fabrication of zirconiatoughened alumina parts by powder injection 2005年6月1日 Injection molding of ultrafine 3YZrO2 and Al2O 3 powders with high purity were studied in this work, which included the fluidity of feedstock, the properties of green bodies and sintered bodiesInjection molding of oxide ceramic with high performance
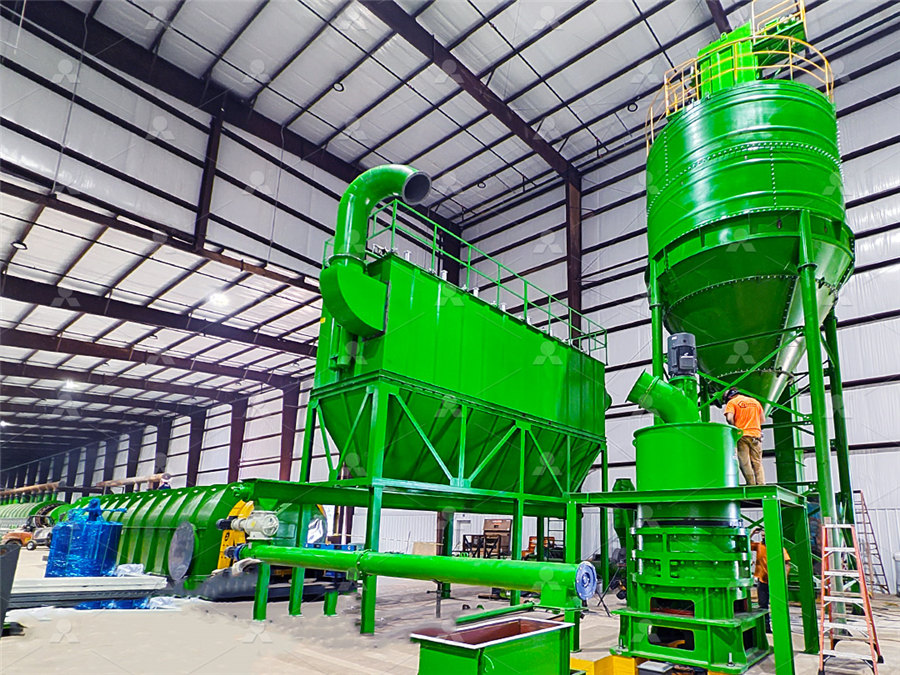
Injection molding of ultrafine zirconia (YTZP) powders
Injection moldings of three types of ultrafine zirconia powder were investigated It was demonstrated that powder characteristics involving particle size, particle size distribution, particle shape and specific surface area significantly affect the optimal compositions of binders and ceramic powders, and the properties of sintered compactsInjection moldings of three types of ultrafine zirconia powder were investigated It was demonstrated that powder characteristics involving particle size, particle size distribution, particle shape and specific surface area significantly affect the optimal compositions of binders and ceramic powders, and the properties of sintered compactsInjection molding of ultrafine zirconia (YTZP) powders2014年3月1日 Feedstocks for ceramic injection molding of ZTA containing 90 vol% of subμm alumina and 10 vol% of zirconia nanopowder were prepared by different processing techniquesInfluence of feedstock preparation on ceramic injection molding The ceramic injection molding technique was used in the gaspressure sintering of ultrafine Si3N4 powder The feedstock’s flowability, debinding rate, defect evolution, and microstructural evolution during production were explored The results show that the solid volume loading of less than 50vol% and the surfactant mass fraction of 6wt% result in a perfect flowability of Injection molding of ultrafine Si3N4 powder for gaspressure
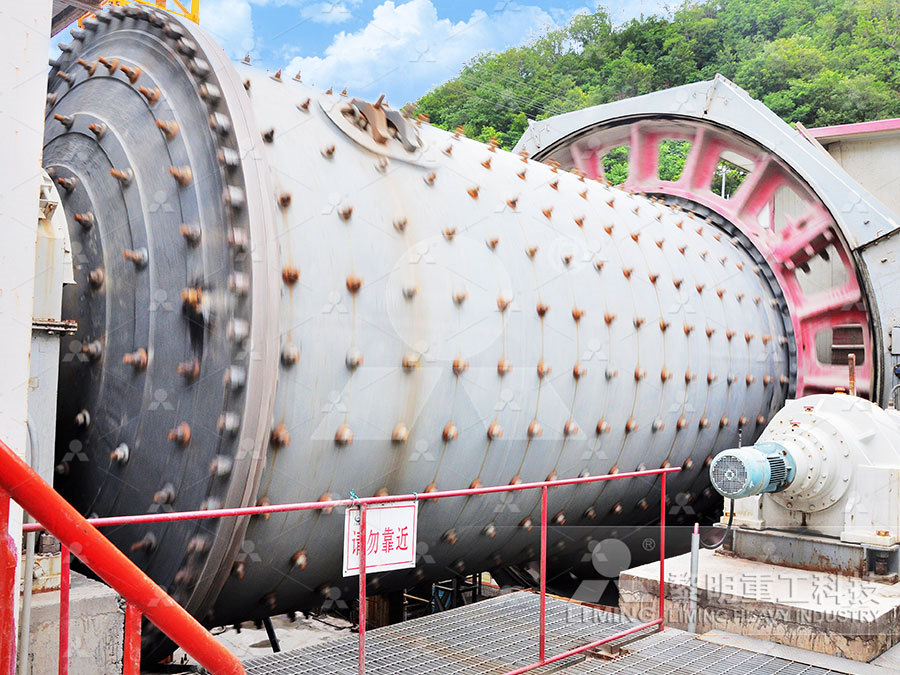
Metal Injection Molding Ultra Fine
Metal Injection Molding The Metal Injection Molding (MIM) process uses Ultra Fine metal powders and plastic binders to cost effectively produce small, complex parts for a wide variety of applications including aerospace, automotive, consumer goods, dental tools, firearms, and medical devices2021年3月28日 The injection molding was done at 190℃ followed by water debinding of PEG at 40℃ Powder injection molding of zirconia [1321] have been explore d in a numbe r of s tudies(PDF) Microstructure and properties of zirconia Zhejiang Jinkun Zirconia lndustry Co,Ltd The main products JK3YZN, JKYDENTAL are suitable for pressing molding,injection molding,isostatic pressing molding,casting molding and extrusion molding The products satisfy the different needs of Zhejiang Jinkun Zirconia lndustry Co,Ltd2004年11月1日 The procedures of ceramic injection molding (CIM) include four steps: kneading process, injection molding, debinding, and sintering[1], [2], [3] The CIM technology offers the opportunity to make complex and nearnetshape of ceramic parts The kneading process is an important step in ceramic injection moldingKneading behaviour and homogeneity of zirconia feedstocks for
.jpg)
Injection molding of ultrafine Si3N4 powder for gas
2015年6月1日 The ceramic injection molding technique was used in the gaspressure sintering of ultrafine Si3N4 powder The feedstock’s flowability, debinding rate, defect evolution, and microstructural Injection molding of ultrafine zirconia (YTZP) powders Jiesheng Luoa, Zhongzhou Yib, Bing Xiaoc, Yan Gaoa, Zhipeng Xiea,*, Jianbao Lia and Yong Huanga a Department of Materials Science Engineering, Tsinghua University, Beijing, , China b Chemistry Department of Honghe University, Yunnan , China c Zhongyuan Engineering College, Zhengzhou JCPR2007年10月1日 The effect of organic vehicle on the injection molding of ultrafine zirconia powders Mater Des, 26 (2005), pp 7982 View PDF View article View in Scopus Google Scholar [8] Grain growth in ultrafinegrained YTZP ceramics J Eur Ceram Soc, 17 (1997), pp 11331141 View PDF View article View in Scopus Google ScholarTwostage sintering of nanosized yttria stabilized zirconia Despite its unique high efficiency and good environmental compatibility, the watersoluble binder system still encounters problems achieving a desired sintered part via ceramic injection molding because of the poor compatibility and the powderbinder A strategy to obtain a highdensity and highstrength zirconia
.jpg)
Kneading behaviour and homogeneity of zirconia feedstocks for
2004年11月1日 The procedures of ceramic injection molding (CIM) include four steps: kneading process, injection molding, debinding, and sintering [1], [2], [3] The CIM technology offers the opportunity to make complex and nearnetshape of ceramic parts The kneading process is an important step in ceramic injection molding2007年10月1日 Powder injection moulding (PIM) is capable of mass producing intricately shaped components In recent years, this technology has been adopted in the electronic, computer, chemical and medical industries The 3 mol% yttria stabilized zirconia (YTZP) is well recognised for its high fracture toughnessPIM of nanosized YTZP hence offer attractive Twostage sintering of nanosized yttria stabilized zirconia