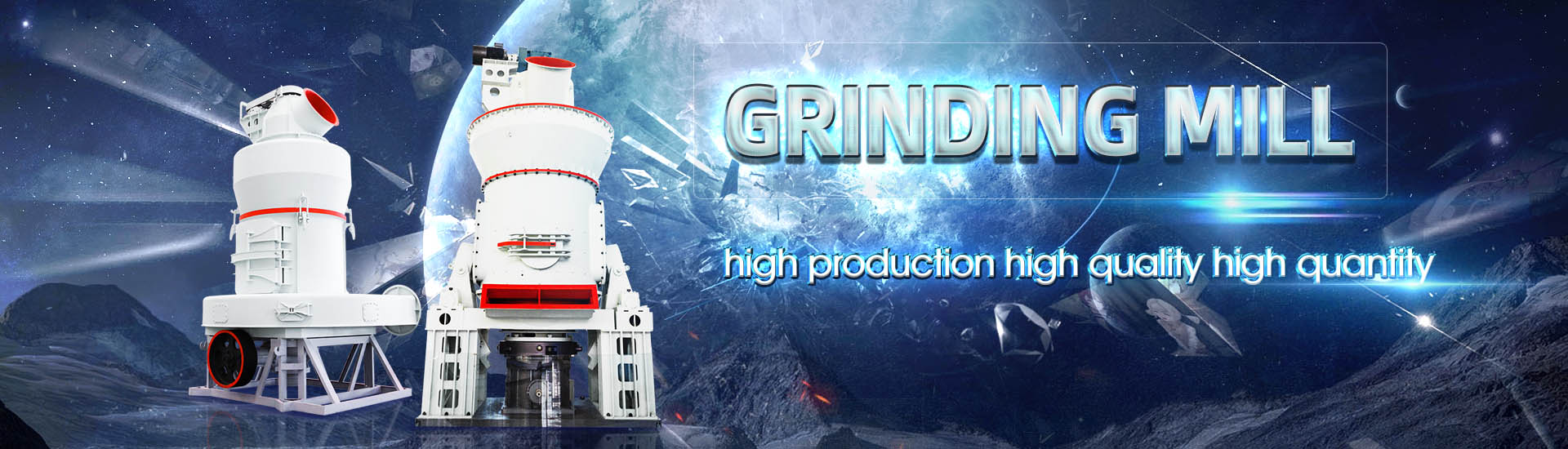
Alligator ore mill installation requirements
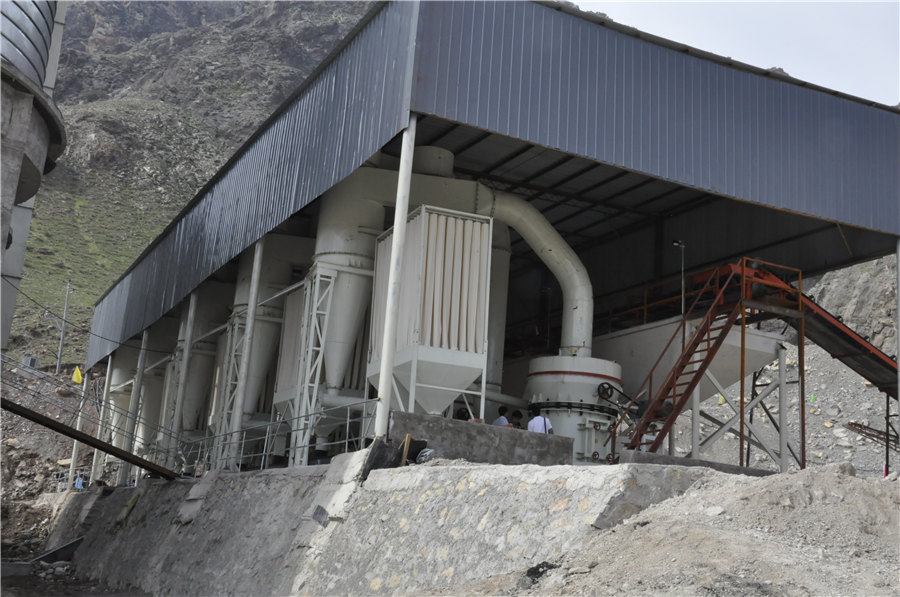
SUPPLY, INSTALLATION, COMMISSIONING OF THE WORLD'S
36 ft (111 m) mill would treat ore at a rate slightly lower than the required 17 t/a The 38 ft (116 m) and 40 ft (122 m) mill options were simulated as achieving the target treatment rate; however, the 38 ft (116 m) mill required a higher ball charge (10%)Currently a number of the largest SAG mills designed are installed in single stage configuration This paper discusses the challenges associated with the process design of single stage SINGLE STAGE SAG/AG MILLING DESIGN SquarespaceThe energy required to lift and throw charge (aimed to generate highenergy ballrock impacts at the charge toe) can be estimated from the lifting rate and height of lift of material between the Semiautogenous grinding (SAG) mill liner design and developmentIncreasing angles on the leading edge of the lifter bar will cause the mill to require a higher speed to obtain the desired mill power level at a given set of conditions of load (measured as percent SUPPLY, INSTALLATION, COMMISSIONING OF THE WORLD'S
7TOCS.jpg)
Design of the 40 foot SAG Mill Installed at the Cadia
The design of the 40foot diameter SAG mill installed at the Cadia Gold Mine, New South Wales Australia, followed after two years of extensive laboratory and pilot plant testwork This entirely possible for a relatively ‘soft’ ore with Axb ~70 to have similar SAG milling Ecs requirements as a relatively competent ore with Axb ~40, depending on the cumulative SAG Mill Design and Benchmarking Using Trends in the JKTech machine parameters and ore character istics, so it will facilitate the design of a "best fit crusher" for any given applica tion flowsheet It can also be used to finetune existing crushing imgX4These projects involved SAG mills from 26 to 36 ft in diameter, with installed power in the range 97 to 168 MW using single, twin pinion, and gearless technology for drives over 16 MW The Recent International Concentrator Startups Do and Don’ts for
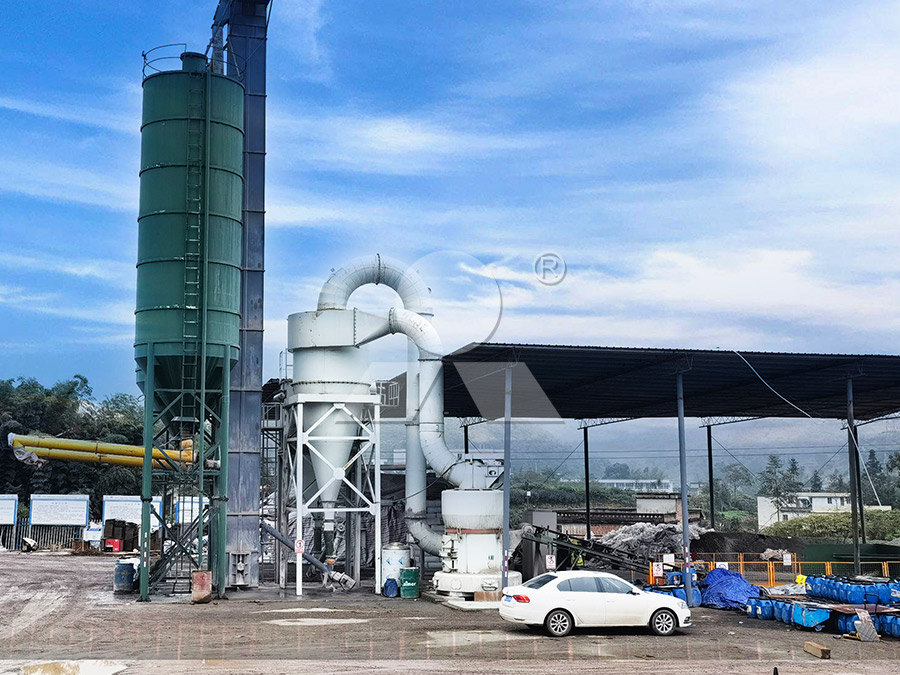
SAG mill increases productivity, reduces unscheduled shutdowns
autogenous mills – commonly known as SAG mills – use milling balls, as well as the weight of the ore itself, to break down the ore into smaller particles – a process known as comminution The 960284D Installation 1 aa Aain n 1 VERTICAL MILL INSTALLATION INSTRUCTIONS Machine RequiReMents Machine footprints and operating dimensions are available in the brochure and the anchoring addendum GeneRal RequiReMents Operating Temperature Range 41°F to 104°F (5 to 40°C) Storage Temperature Range 4°F to 158°F (20 to 70°C)VERTICAL MILL INSTALLATION INSTRUCTIONS Haas AutomationAlliGator Installation System Requirements This software will only run on Microsoft Windows 10 64 bit Some of the functions used by the software support parallelism, therefore a multiprocessor and/or multicore computer is recommended (this statement is not as dated as it sounds, as virtual machines offer the choice of core number)AlliGator Installation — AlliGator 097 documentation Read 2022年11月13日 3 According to the discharge situation (qualified products) and output of the rod mill, the reasonable rod loading capacity of this rod mill should be determined with reference to the actual rod loading capacity of the same Rod Mill operation manual : how to install use
.jpg)
CLASSIFIER MILL INSTALLATION, OPERATION, AND MAINTENANCE MANUAL
CLASSIFIER MILL INSTALLATION/OPERATION AND MAINTENANCE MANUAL 8 Section 2: Introduction 21 Manual Overview This manual describes the installation requirements, procedures, and routine maintenance of Prater’s Classifier Mill, Model #’s CLM – 36, CLM – 51, CLM – 76, and CLM 101 Refer to this manual beforeThis document provides instructions for installing a 16x22ft, 2800kW ball mill It outlines 8 key steps: 1) Prepare the foundation and install the trunnion bearing sole plates 2) Assemble and mount the trunnion bearings onto the sole plates 3) Assemble the trunnion ends to the mill shell 4) Lower the mill unit into the bearings and check clearances 5) Install the girth gear 6) 16' X 22' Ball Mill Installation Manual PDF ScribdCOLLOID MILL PHARMA DEVILS QUALITY ASSURANCE DEPARTMENT 20 OBJECTIVE: To provide documented evidence for the Installation Qualification of Colloidal Mill To confirm that the equipment and its components are installed as per the Specifications mentioned in the design qualification document and other requirements given by supplierINSTALLATION QUALIFICATION PROTOCOL CUM REPORT FOR COLLOID MILL2020年7月27日 #BallmillBall Mill Installation In Africa For Grinding Ore 2020 Ball mill installation is a must step before it is put into production, which will affect thBall Mill Installation In Africa For Grinding Ore 2020 YouTube
.jpg)
Predicting the overall specific energy requirement of crushing,
80 ( ) 80 0 295 1 80 80 1818 ib P Gbp p f p f f f M − = (6) where Mib = fine ore work index (kWh/tonne) P1 = closing screen size in microns Gbp = net grams of screen undersize per mill revolution p80 = 80% passing size of the product in microns f80 = 80% passing size of the feed in microns Note that the Bond ball work index test should be carried out with a closing screenInstallation Tools Alligator® Quad Staple Driver Ordering Number ST69 Alligator® Quad Staple Driver The Alligator® Quad Staple Driver allows for the installation of four staples at one time Using a 9 kg hammer, this durable, heattreated steel quad driver allows installers to cut their installation time by 50% Alligator® Staple Tool KitAlligator Staple Fastening System FlexcoNAME OF ITEM: Colloid Mill PROTOCOL No FUNCTIONAL AREA: Production Page No: 2 of 11 Page 2 of 11 CONTENT SNo Description 10 URS Approval 20 Objective Pre Installation Requirements will be supplied by Vendor 632 LIST Equipment and instrument list with Component description Electrical component parts list withInstallation Qualitifcation Report Pharma Devils36 ft (111 m) mill would treat ore at a rate slightly lower than the required 17 t/a The 38 ft (116 m) and 40 ft (122 m) mill options were simulated as achieving the target treatment rate; however, the 38 ft (116 m) mill required a higher ball charge (10%) The pilot plant testing had indicated that operating and circuit stabilitySUPPLY, INSTALLATION, COMMISSIONING OF THE WORLD'S LARGEST GRINDING MILL
.jpg)
Regrind Mills: Challenges of Scaleup Abstract 911 Metallurgist
As ore deposits become finer grained the requirements for regrinding before cleaning or leaching have increased substantially Despite this increasing need, there is no standard test to predict grinding energy requirement below 70 microns The standard Bond Mill test applies for coarser ball milling, but is not2012年12月6日 Ball mill is the important equipment in mineral ore grinding or mineral powder making and beneficiation, so ball mill installation and maintenance are become the important thing, following are common knowledge about ball mill machines’ installation i large ball mill must be installed in the already dry solid reinforced concrete foundationBall Mill Installation Instructions Mining, Crushing, Grinding In this article, we will discuss the work that needs to be done after the installation of a ball mill and the precautions that need to be taken to ensure safe and efficient operation Inspection of the ball mill After installing a ball mill, it is important to conduct a thorough inspection of the equipment to ensure everything is in orderBall Mill Installation Essential Work and PrecautionsES33 Rev AW Oct 3 Page 4 of 9 Haas Technical Publications PreInstallation Information Placement and Preparation Foundation Requirements Machines must be set on a solid, sound and stable, steel barreinforced concrete slab poured directly onPREINSTALLATION INFORMATION UC Santa Barbara
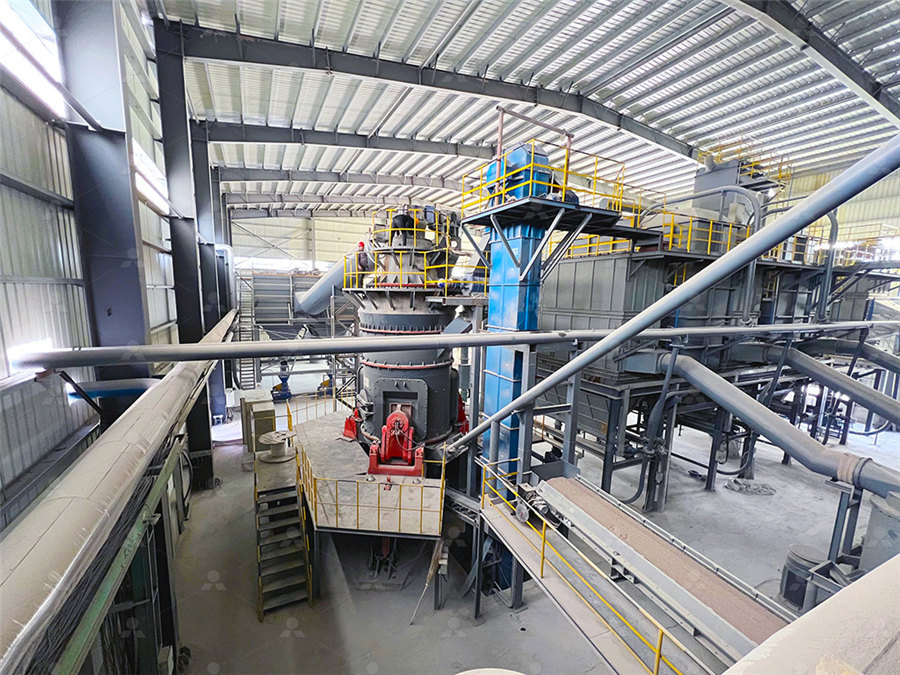
Methodology for Grinding Mill Installation Fault Zone
2015年2月12日 Setup for installation of the mill liners according to the requirements of the type being used Establish a method of moving the liners into the mill by way of a cable feed structure or mono rail, allowing each liner or lifter to be hooked onto the system and fed into the men working inside the mill2010年9月30日 The document discusses the basic requirements and design considerations for running a wind mill It notes that atmospheric pressure should be 85 bar and efficiency increases 100% for every 10 meters in height Blades should be airfoil shaped and made of materials like NACA 44 or 63 to withstand all weather conditionsWind Mill PPT SlideShare2020年1月3日 Installation steps of ball mill The installation of the ball mill shall be carried out according to the following steps: preparation before entering the site, foundation review, sizing block How to install the ball mill? Here is a detailed strategy: installation the early installations treated only ultrafine sizes, the current mill installations are treating courser sized materials, once the domain of tower and ball mills The need for energy efficient grinding circuits will only result in more IsaMill™ circuits being applied in the future IsaMill™ OPERATION Grinding MechanismIsaMill Technology Used in Effecient Grinding Circuits
.jpg)
What Are the Requirements for Building a Steel Rolling Mill?
2024年3月11日 To sum up, establishing a steel rolling mill requires comprehensive consideration of many aspects such as capital, technology, raw materials, environmental protection, market, policy, and human resources Only when these conditions are met, the steel rolling mill can be constructed and operated smoothly and achieve sustainable developmentmill specific power, pilot plant ball mill specific power, pilot plant product size distributions and Bondtype calculations (as reported by Rowland (Rowland, 1982) and modified by Minproc) SAG Mill Dimensions: The SAG mill was designed for monzonite ore, with allowance in the mine schedule for reduced throughput when treating the harder Design of the 40 foot SAG Mill Installed at the Cadia Gold Copper 2023年10月8日 System requirements for Autodesk PowerMill 2023; Operating System: 64bit Microsoft® Windows® 11 and Windows 10 See Autodesk's Product Support Lifecycle for support information: CPU Type: Multiple core 64bit processor, such as Intel® Core™ i7 or Intel® Core™ i9System requirements for Autodesk PowerMill 年6月25日 This procedure tells you how to install a Mini Mill/2/EDU, or Super Mini Mill/2 To install a Reboot Mini Mill, refer to the Mini Mill Installation procedure for more information Note: For air requirements refer to the Mini Mill/Super Mini Mill Installation Haas
.jpg)
VERTICAL MILL INSTALLATION INSTRUCTIONS Amazon Web
4030 HP System Voltage Requirements HighVoltage Requirements2 50 TAPER, HT10K(40T), VM, SS mills (195260V) (354488V) Power Supply1 100 AMP 50 AMP Haas Circuit Breaker 80 AMP 40 AMP If service run from elecpanel is less than 100' use: 4 GA WIRE 8 GA WIRE If service run from elec panelDOVE offers a wide range of high quality ball mills, for wet or dry grinding operations, as well as regrinding application, for capacities up to 240 Tons/HourBall Mill Ball Mills Wet Dry Grinding DOVESuper Mini Mill Install Guide CNY ONLY SuperSpeed Mini Vertical Mill with 16" x 14" x 15" travels 40 Taper; 3 Axis; 10k RPM; 30 Verify the power requirement before running power for your machine Air Requirements for Haas MachinesSuper Mini Mill Preinstall Guide Haas Automation IncThis Video shows installation and commissioning process of Ball mill All kinds of ball mills produced and sold by our company have good mechanical performance and high grinding efficiency, which are favored by the marketInstallation and Commissioning of Ball mill Facebook
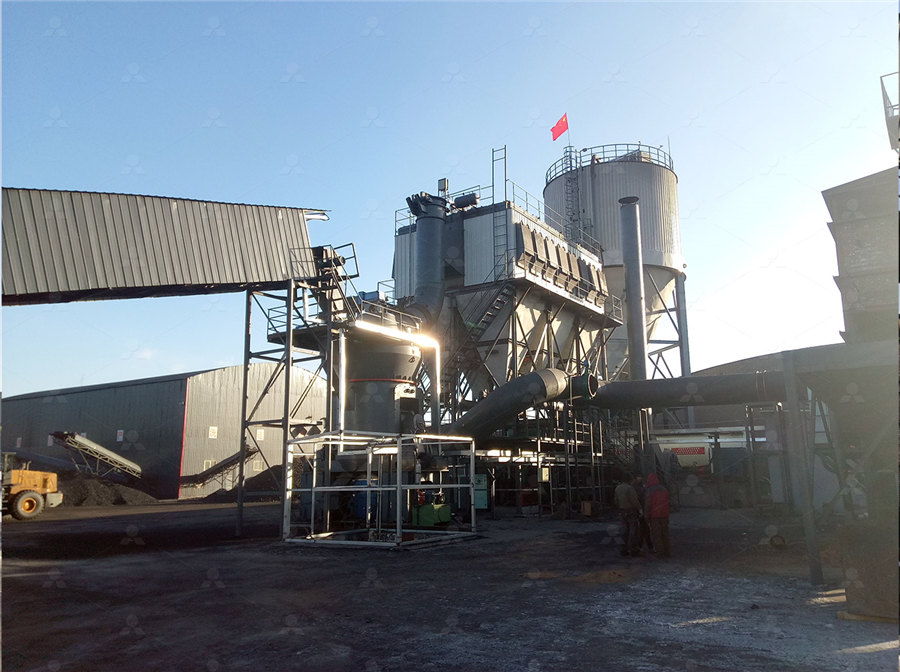
Monitoring ore loss and dilution for minetomill integration in
2016年2月1日 The purpose of this study is to understand how ore loss and dilution affect the mine call factor, with the aim of subsequently improving the quality of ore mined and fed to the millThe rod mill is another type of grinding mill used in the copper ore mining process This machine uses steel rods as the grinding media instead of balls, which are commonly used in ball mills The rods grind the ore by tumbling within the mill, similar to the action of a rotating drumUnderstanding the SAG Mill in Copper Ore Mining ProcessAlligator® Lacing Overview Author: Flexco® Subject: Обзор соединителей Alligator® Lacing Flexco® Keywords: Alligator® Lacing, Flexco Alligator® Lacing, @centrobelt Created Date: 2/7/2014 9:27:54 AMALLIGATOR Radius Check960284D Installation 1 aa Aain n 1 VERTICAL MILL INSTALLATION INSTRUCTIONS Machine RequiReMents Machine footprints and operating dimensions are available in the brochure and the anchoring addendum GeneRal RequiReMents Operating Temperature Range 41°F to 104°F (5 to 40°C) Storage Temperature Range 4°F to 158°F (20 to 70°C)VERTICAL MILL INSTALLATION INSTRUCTIONS Haas Automation
.jpg)
AlliGator Installation — AlliGator 097 documentation Read
AlliGator Installation System Requirements This software will only run on Microsoft Windows 10 64 bit Some of the functions used by the software support parallelism, therefore a multiprocessor and/or multicore computer is recommended (this statement is not as dated as it sounds, as virtual machines offer the choice of core number)2022年11月13日 3 According to the discharge situation (qualified products) and output of the rod mill, the reasonable rod loading capacity of this rod mill should be determined with reference to the actual rod loading capacity of the same Rod Mill operation manual : how to install use CLASSIFIER MILL INSTALLATION/OPERATION AND MAINTENANCE MANUAL 8 Section 2: Introduction 21 Manual Overview This manual describes the installation requirements, procedures, and routine maintenance of Prater’s Classifier Mill, Model #’s CLM – 36, CLM – 51, CLM – 76, and CLM 101 Refer to this manual beforeCLASSIFIER MILL INSTALLATION, OPERATION, AND MAINTENANCE MANUALThis document provides instructions for installing a 16x22ft, 2800kW ball mill It outlines 8 key steps: 1) Prepare the foundation and install the trunnion bearing sole plates 2) Assemble and mount the trunnion bearings onto the sole plates 3) Assemble the trunnion ends to the mill shell 4) Lower the mill unit into the bearings and check clearances 5) Install the girth gear 6) 16' X 22' Ball Mill Installation Manual PDF Scribd
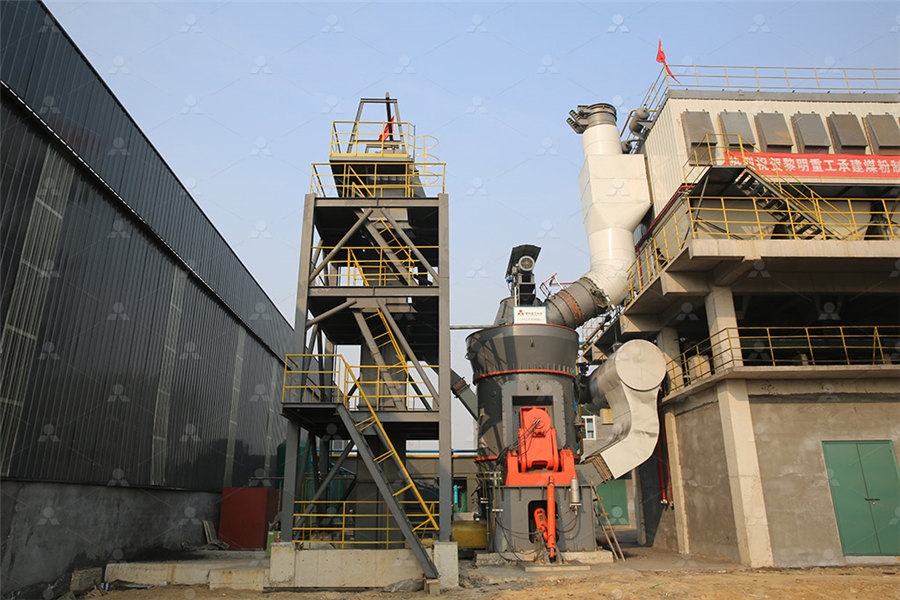
INSTALLATION QUALIFICATION PROTOCOL CUM REPORT FOR COLLOID MILL
COLLOID MILL PHARMA DEVILS QUALITY ASSURANCE DEPARTMENT 20 OBJECTIVE: To provide documented evidence for the Installation Qualification of Colloidal Mill To confirm that the equipment and its components are installed as per the Specifications mentioned in the design qualification document and other requirements given by supplier2020年7月27日 #BallmillBall Mill Installation In Africa For Grinding Ore 2020 Ball mill installation is a must step before it is put into production, which will affect thBall Mill Installation In Africa For Grinding Ore 2020 YouTube80 ( ) 80 0 295 1 80 80 1818 ib P Gbp p f p f f f M − = (6) where Mib = fine ore work index (kWh/tonne) P1 = closing screen size in microns Gbp = net grams of screen undersize per mill revolution p80 = 80% passing size of the product in microns f80 = 80% passing size of the feed in microns Note that the Bond ball work index test should be carried out with a closing screenPredicting the overall specific energy requirement of crushing, Installation Tools Alligator® Quad Staple Driver Ordering Number ST69 Alligator® Quad Staple Driver The Alligator® Quad Staple Driver allows for the installation of four staples at one time Using a 9 kg hammer, this durable, heattreated steel quad driver allows installers to cut their installation time by 50% Alligator® Staple Tool KitAlligator Staple Fastening System Flexco
.jpg)
Installation Qualitifcation Report Pharma Devils
NAME OF ITEM: Colloid Mill PROTOCOL No FUNCTIONAL AREA: Production Page No: 2 of 11 Page 2 of 11 CONTENT SNo Description 10 URS Approval 20 Objective Pre Installation Requirements will be supplied by Vendor 632 LIST Equipment and instrument list with Component description Electrical component parts list with