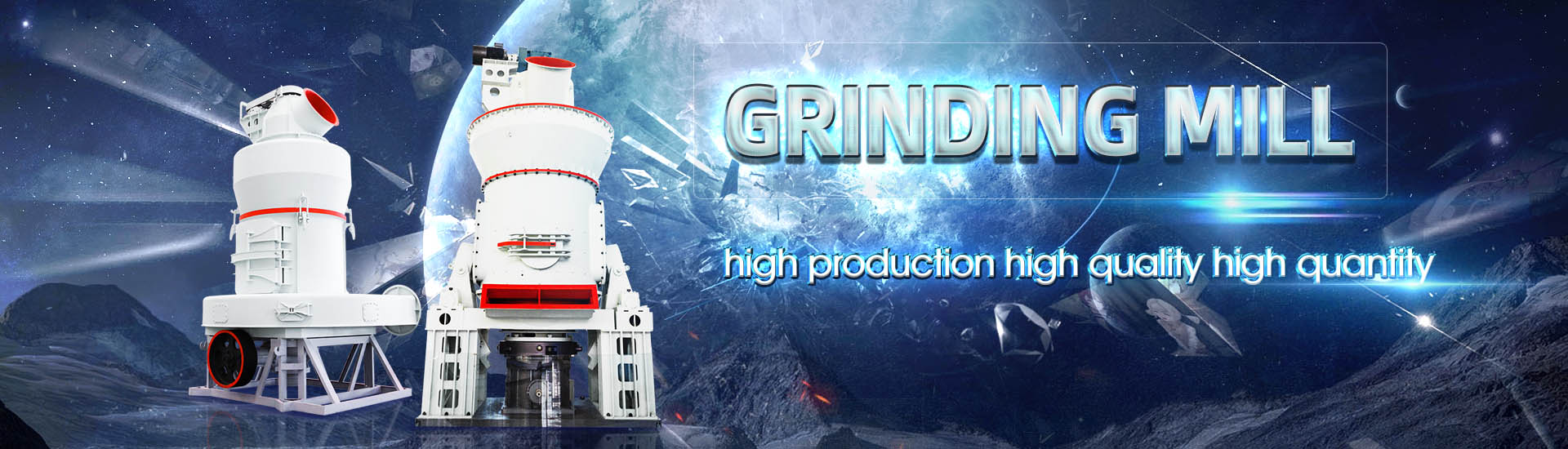
Iron oxide green powder making process working principle
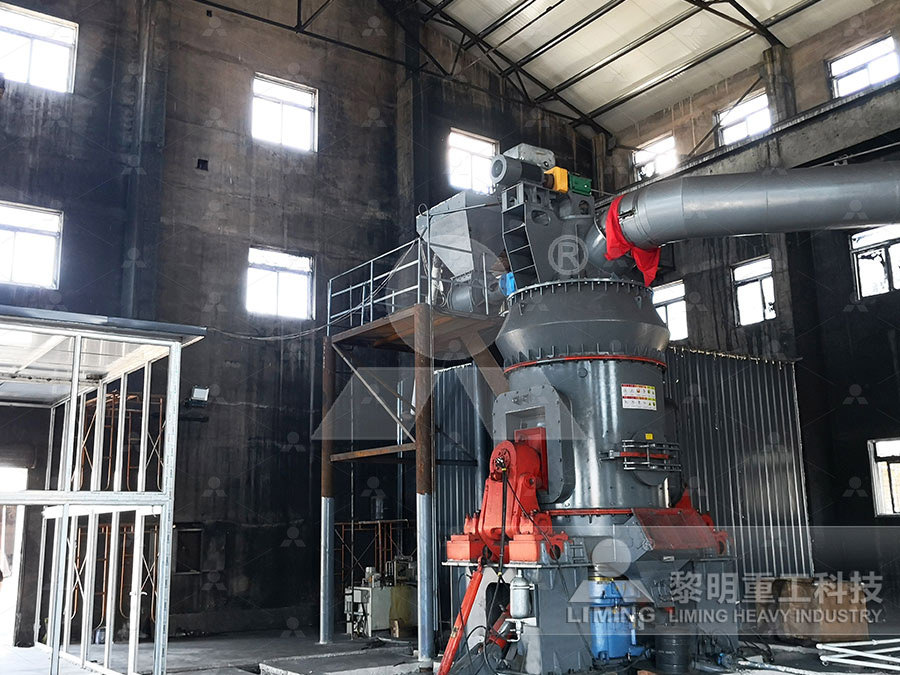
Powder Metallurgy – Powder Processes (Solid State Reduction
The principal method is to disintegrate a thin stream of molten metal by subjecting it to the impact of high energy jets of gas or liquid Air, nitrogen and argon are commonly used gases, and water is the liquid most widely used A commercial scale plant was set up in Japan to produce iron In this study, the reaction process of the ICCB occurred in the contact between the solid green carbon and the iron ore powder, mainly realizing the stepbystep reduction of Fe 3 O 4 → Study on strength and reduction characteristics of iron ore powder Pelletizing iron ore fines is an agglomeration process that through a thermal treatment converts the ultrafines fraction thereof into small balls ranging in size from 8mm (031 in) to 18mm Iron Ore Pelletizing Process: An Overview Academia2017年2月16日 Sintering is a thermal agglomeration process that is applied to a mixture of iron ore fines, recycled ironmaking products, fluxes, slagforming agents, and solid fuel (coke) The (PDF) Iron Ore Sintering: Process ResearchGate
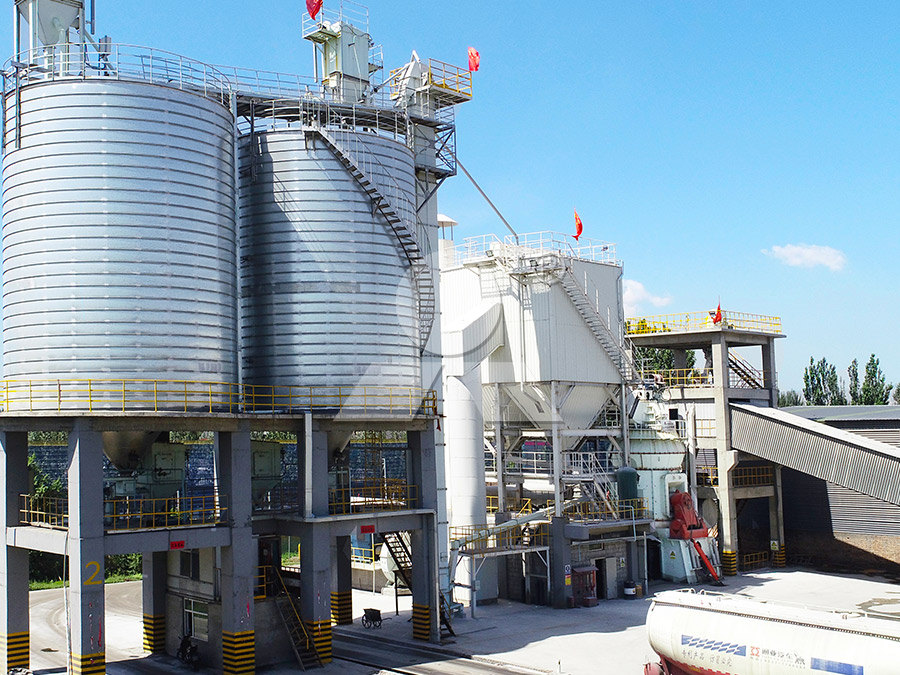
Producing green iron with a zeroCarbon electrochemical Process S
2023年2月9日 develop a new understanding of iron ore dissolution kinetics and a novel electrochemical regeneration scheme that enhances iron ore dissolution and increases the There are four main processes used in powder production: solidstate reduction, atomization, electrolysis, and chemical In solidstate reduction, selected ore is crushed, typically mixed Making Metal Powder MPIF2023年6月1日 Green synthesis is by far the most environmentally friendly method to produce iron oxide nanoparticles (Fe 2 O 3 NPs) In this review article, we report the recent studies on Ecofriendly green synthesis approach and evaluation of 2023年9月1日 The green synthesized iron oxide nanoparticles were characterized using UV–Visible spectrophotometer, Xray powder diffraction (XRD), Fourier transform infrared Green synthesis of iron oxide nanoparticles by Taguchi design of
.jpg)
Iron Ore Pelletizing Process: An Overview ResearchGate
2018年7月11日 concentration process must be agglomerated for use in iron and steelmaking This chapter shows the status of the pelletizing process with a special focus on binders2023年10月9日 This paper introduces the working principle and several typical working states of fluidized bed (FB) technology to clarify the key to fluidized bed process operation(PDF) Development and Problems of Fluidized Bed Process integration and optimization is another good option to decarbonize the iron and steel industry Various optimization techniques have been applied for the iron and steel sector, such as an integrated steel plant system [99], energy intensity optimization [100], and materialenergy nexus flow combination [101]One study [17] illustrated the concept of massthermal network Iron Making an overview ScienceDirect Topics2023年2月9日 develop a new understanding of iron ore dissolution kinetics and a novel electrochemical regeneration scheme that enhances iron ore dissolution and increases the efficiency of iron extraction Instead of heating and smelting the iron ore, Electra’s process dissolves the ore in a waterbased acid solution Next, electricity is used to Producing green iron with a zeroCarbon electrochemical Process S

Iron Ore Pellets and Pelletization Process – IspatGuru
2014年11月26日 Iron Ore Pellets and Pelletization Process satyendra; November 26, 2014; 0 Comments ; bentonite, binder, Grate kiln, induration, Pelletization Pellets, straight grate,; Iron Ore Pellets and Pelletization Process Pelletizing of iron ore was started in the 1950s to facilitate the utilization of finely ground iron ore concentrates in steel production2022年11月24日 The degradation of rifampicin using iron oxide nanoparticles was found to be pseudosecondorder, endothermic, and dependent on the reactant dose used during the study, and variation in reaction (PDF) Kinetics of Rifampicin Antibiotic Degradation Using Green The first step in the overall powder metallurgy process is making metal powders the technique is applicable to all metals that can be melted and is used commercially for the production of iron; copper; alloy steels; brass; bronze; lowmeltingpoint metals such as The most common chemical powder treatments involve oxide reduction, Making Metal Powder MPIFDownload scientific diagram Working principle of a solid oxide electrolysis cell (SOEC) from publication: High Temperature Electrolysis in Alkaline Cells, Solid Proton Conducting Cells, and Working principle of a solid oxide electrolysis cell (SOEC)
.jpg)
Powder Metallurgy Processes and Making Metal Powder
2020年10月26日 This research includes a review of powder metallurgy processes, advantages and disadvantages, applications, and production methods of metal powder Powder metallurgy process steps consist of FFC process The ironmaking process of the FFC is shown in Fig 4 [27] Given that the FFC process uses an oxide as the cathode of the electrochemical reaction, the oxide is not dissolved in the electrolyte during the whole electrolytic process, and no liquid or ionic metal with strong activity is presentResearch progress in the preparation of iron by electrochemical Iron processing Smelting, Refining, Alloying: The primary objective of iron making is to release iron from chemical combination with oxygen, and, since the blast furnace is much the most efficient process, it receives the most attention here Alternative methods known as direct reduction are used in over a score of countries, but less than 5 percent of iron is made this wayIron processing Smelting, Refining, Alloying BritannicaTo solve the problems the granulation of the oxide powder and a twostep heat treatment process [10] A closer description of the technology was published in a previous paper [12] In the first step the iron oxide powder was milled in a binder slurry for spray granulation The principle of the mortar grinder ensures high shear New Processing Route for Production of Fine Spherical Iron Powder
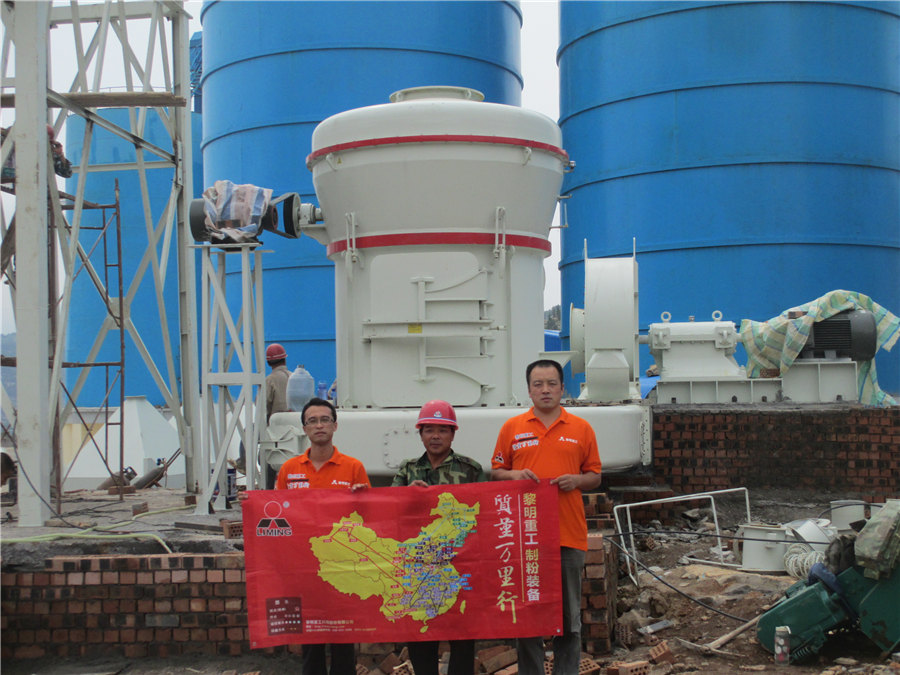
(PDF) IRON ORE PELLETIZING PROCESS ResearchGate
2023年11月15日 Poveromo, JJ, 2014 Future trends in Ironmaking, prepared for McMaster blast furnace ironmaking course, May 11 – 16, 2014CI 77491 Red Iron Oxide Powder is an oildispersible pigment which is suitable to use in lotions, soap, Cold Process Soap 15 Product Downloads Chromium Oxide Green Pigment Powder Read more £780 incVAT £650 Red Iron Oxide Powder CI 77491 Soapmakers Store2023年9月8日 solutions have been proposed for the blast furnace, for example, hig hly oxygenenriched or hydrogenrich operationBlast Furnace process optimization for sustainable Iron making2021年10月31日 This review reveals 12 principles of “green” chemistry and examples of biological components suitable for “green” synthesis, as well as modern scientific research of ecofriendly synthesis Green Synthesis of Metal and Metal Oxide Nanoparticles:Principles
.jpg)
Making sustainability measurable – Environmental Product
It is deployed in the so called precipitation process that results in very highquality yellow pigments with special properties such as high tinting strength and thermal stability This “green” raw material helps to cut CO2 emissions during the manufacture of these product groups by up to 40 percent per kilogram of pigmentOne of the benefits of the gas atomized pure iron powder over carbonyl or fine powder derived from sponge iron is that the powder is slightly coarser and has better flowability, thus allowing it to be used with MBJ Inherently, the sinterability of pure iron is extremely low, so in order to evaluate the magnetic response of the iron powder PROPERTIES AND APPLICATIONS FOR IRON POWDER MADE BY 2024年5月15日 1 Iron as a solution in emerging technologies for a decarbonized energy future The concept of energy resilience is now becoming an increasingly important topic of discussion at many levels (eg, social, economic, technical, and political), highlighting the need for concrete solutionsThe shift towards producing energy from renewable and lowcarbon energy sources Back to the future with emerging iron technologiesKey Components of Iron Oxide Pigments For Fertilizers The primary component of iron oxide pigments for fertilizers is iron oxide Iron oxide pigments are manufactured from several types of iron oxides, including ferric oxide (Fe2O3), ferrous oxide (FeO), and magnetite (Fe3O4) The type of iron oxide used depends on the desired color of the pigmentIron Oxide Pigments For Fertilizers
.jpg)
Green synthesis of iron oxide nanoparticles by Taguchi design of
2023年9月1日 The effect of process parameters such as leaves extracts volume, salt precursor concentration, contact time and calcination temperature were investigated on the surface area of iron oxide nanoparticle synthesis The green synthesized iron oxide nanoparticles were characterized using UV–Visible spectrophotometer, Xray powder diffraction (XRD iron oxide green Iron oxide green is also called compound ferric green, it is green powder with bright green and deep green, which owns high opacity, strong tinting strength, easy dispersibility, outstanding light and weather fastnessIron Oxide Green Compound Ferric Green Iron Oxide Green How to make red iron oxide powder in industry Manufacturing red iron oxide powder, also known as rust, is a crucial process in the industry The powder is primarily utilized as a pigment in many applications such as paints, ceramics, and construction materials In this concise guide, we will take a closer look at the process of producing red Make red iron oxide powder Farayand powder2024年12月2日 Metallurgy Powder, Process, Components: Powder metallurgy (P/M) consists of making solid parts out of metal powders The powder is mixed with a lubricant, pressed into a die to form the desired shape, and then Metallurgy Powder, Process, Components Britannica
.jpg)
WaterAssisted Green Production of Steel Powder in Molten Salt
2021年1月22日 In this process, the mixed oxides in In the present study, 15 g iron oxide powder was directly used in the making them uneconomical for largescale pound, usually the oxide, in the solid state, electrodeposition, and the atomization of molten metal Of these the last three account for the bulk of the powders used Solid State Reduction This has been for long the most widely used method Powder Metallurgy – Powder Processes (Solid State Reduction 2020年8月11日 Request PDF Sustainable IronMaking Using Oxalic Acid: The Concept, A Brief Review of Key Reactions, and An Experimental Demonstration of the IronMaking Process Global iron and steel Sustainable IronMaking Using Oxalic Acid: The Concept, A Brief Iron Oxide Green PIGMENT150 Grams : Amazon: Home Kitchen Whether you are working on your own projects or planning to turn kids on, TOLARAM RANGWALA Shop Mica Powder Soap Making Kit Makeup Dye Chameleon Powder Iron Oxide Green PIGMENT150 Grams Amazon
.jpg)
Green Steelmaking IspatGuru
2021年9月8日 The process is to depend on a CO2lean electricity source such as renewable power, hydro power, or nuclear power ULCOLYSIS is the molten oxide electrolysis Molten oxide electrolysis works by passing an electric current through molten slag fed with iron oxide The iron oxide breaks down into liquid iron and oxygen gas No CO2 is produced2023年11月7日 This comprehensive monograph is primarily intended to describe the patented FerWIN® technology, a green and zerocarbon ironmaking process, which consists to perform the electrowinning of iron (PDF) Electrowinning Iron and Recycling Sulfuric Acid from Iron 2024年1月15日 The therapeutic application of iron (oxyhydr)oxide nanoparticles is becoming increasingly important This is due to their lowcost production, nontoxic properties, good bioavailability and biodegradability [[1], [2], [3]], as well as their exceptional properties such as high surfacetovolume ratio [4], and superparamagnetism [3]Thus, iron (oxyhydr)oxide Process development for pilotscale spray drying of ultrasmall iron 2023年10月9日 This paper introduces the working principle and several typical working states of fluidized bed (FB) technology to clarify the key to fluidized bed process operation(PDF) Development and Problems of Fluidized Bed
.jpg)
Iron Making an overview ScienceDirect Topics
Process integration and optimization is another good option to decarbonize the iron and steel industry Various optimization techniques have been applied for the iron and steel sector, such as an integrated steel plant system [99], energy intensity optimization [100], and materialenergy nexus flow combination [101]One study [17] illustrated the concept of massthermal network 2023年2月9日 develop a new understanding of iron ore dissolution kinetics and a novel electrochemical regeneration scheme that enhances iron ore dissolution and increases the efficiency of iron extraction Instead of heating and smelting the iron ore, Electra’s process dissolves the ore in a waterbased acid solution Next, electricity is used to Producing green iron with a zeroCarbon electrochemical Process S2014年11月26日 Iron Ore Pellets and Pelletization Process satyendra; November 26, 2014; 0 Comments ; bentonite, binder, Grate kiln, induration, Pelletization Pellets, straight grate,; Iron Ore Pellets and Pelletization Process Pelletizing of iron ore was started in the 1950s to facilitate the utilization of finely ground iron ore concentrates in steel productionIron Ore Pellets and Pelletization Process – IspatGuru2022年11月24日 The degradation of rifampicin using iron oxide nanoparticles was found to be pseudosecondorder, endothermic, and dependent on the reactant dose used during the study, and variation in reaction (PDF) Kinetics of Rifampicin Antibiotic Degradation Using Green
.jpg)
Making Metal Powder MPIF
The first step in the overall powder metallurgy process is making metal powders the technique is applicable to all metals that can be melted and is used commercially for the production of iron; copper; alloy steels; brass; bronze; lowmeltingpoint metals such as The most common chemical powder treatments involve oxide reduction, Download scientific diagram Working principle of a solid oxide electrolysis cell (SOEC) from publication: High Temperature Electrolysis in Alkaline Cells, Solid Proton Conducting Cells, and Working principle of a solid oxide electrolysis cell (SOEC)2020年10月26日 This research includes a review of powder metallurgy processes, advantages and disadvantages, applications, and production methods of metal powder Powder metallurgy process steps consist of Powder Metallurgy Processes and Making Metal PowderFFC process The ironmaking process of the FFC is shown in Fig 4 [27] Given that the FFC process uses an oxide as the cathode of the electrochemical reaction, the oxide is not dissolved in the electrolyte during the whole electrolytic process, and no liquid or ionic metal with strong activity is presentResearch progress in the preparation of iron by electrochemical
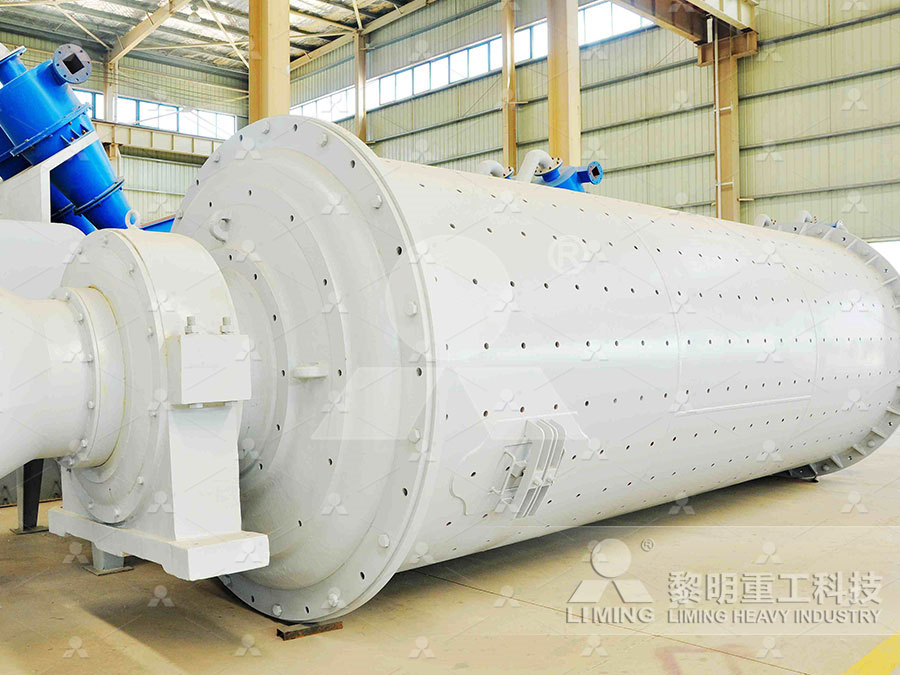
Iron processing Smelting, Refining, Alloying Britannica
Iron processing Smelting, Refining, Alloying: The primary objective of iron making is to release iron from chemical combination with oxygen, and, since the blast furnace is much the most efficient process, it receives the most attention here Alternative methods known as direct reduction are used in over a score of countries, but less than 5 percent of iron is made this way