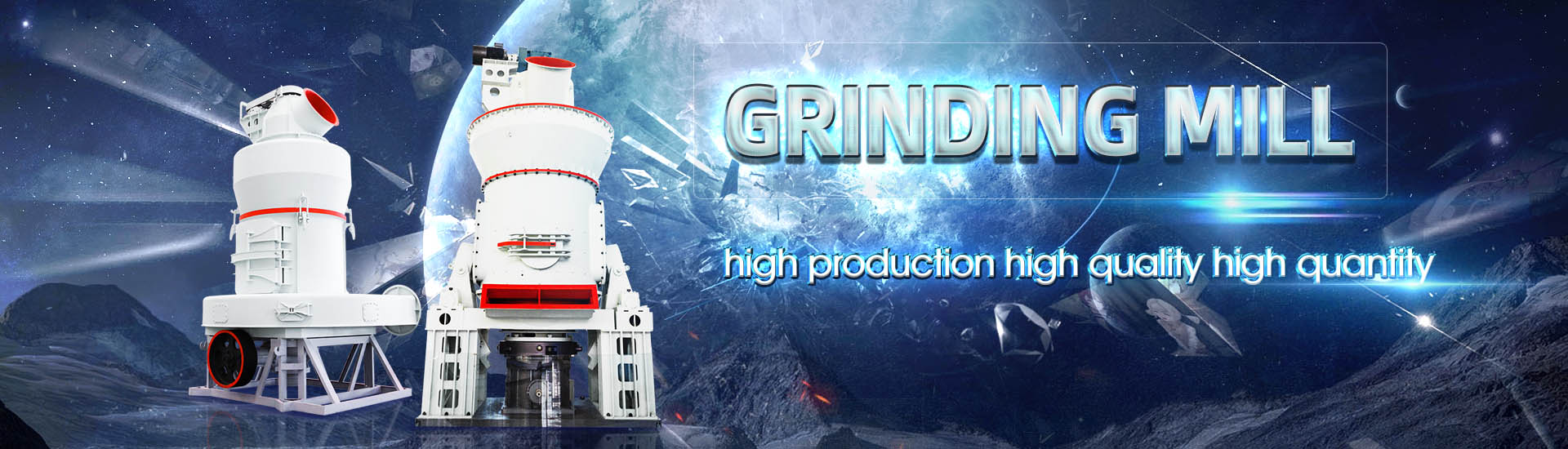
What documents are required for ore powder mill production
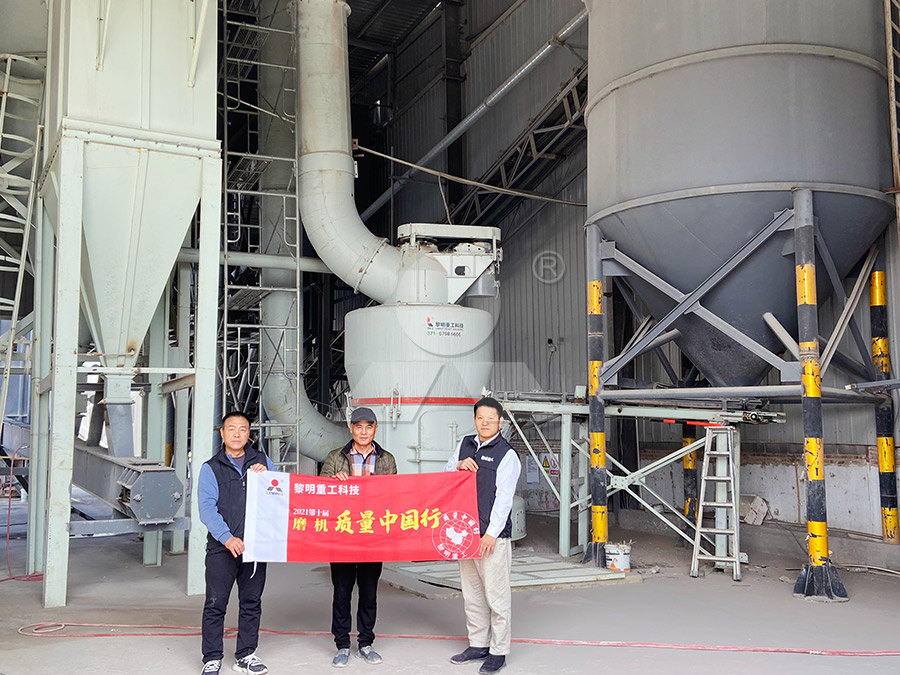
Iron Manufacturing process related to the specified manufacture(s)
The Höganäs process is a direct reduction method for production of sponge iron powder using magnetite ore (Fe3O4) and carbon as raw materials The reduction process takes place in a gas fired tunnel kiln at around 1200°C for 60 hours producing a sponge iron cake that is crushed, Ore powder production involves the conversion of mined ore into fine particles through a series of crushing, grinding, and classifying processes The equipment used in this process must be Advancements in ore powder production process equipment: IN the operation of any ore processing plant, no matter what beneficiation process or combination of processes may be used, certain fundamental figures are regularly needed for essential OneMine Mill Operating Records And AccountsBasic steps of the Powder Metallurgy Process A collection of powder metallurgy parts PM is the choice when requirements for strength, wear resistance or high operating temperatures MME 3518 POWDER METALLURGY
CFB石灰石脱硫剂制备96.jpg)
Powder Milling an overview ScienceDirect Topics
2010年4月1日 Powder Production The flow sheet of powder production by solidphase reduction of metal compounds includes three main stages: preparation of the raw material 2024年4月26日 Iron ore processing is a complex and vital process that transforms raw iron ore into usable steel From exploration and extraction to grinding, beneficiation, and ironmaking, Iron Ore Processing: From Extraction to ManufacturingMany important performance and design elements must go into the selection and integration of a grinding or milling system Trust PPS to consider all your system parameters to integrate the Grinding Milling Powder ProcessSolutionsWater and raw materials are fed to the mill and milled for several hours After milling, the resultant slurry is drawn off to be dehydrated and dried Other methods, for example attritor milling, only Powder Processing an overview ScienceDirect Topics
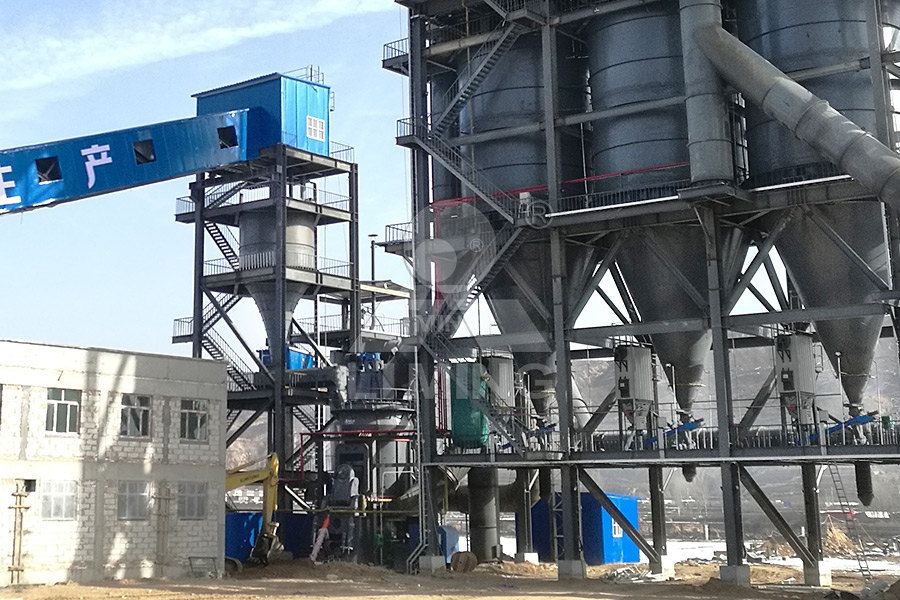
Powder Milling and Grinding An Engineering Guide
Our Powder milling Engineering Guide gives access to all knowledge interesting to Process Engineers in the field of bulk solids size reduction to answer questions related to design or ods are employed for the production of metal powders Seven of the commonly used commercial methods are atomization, decom position, electrolysis, gaseous reduction of solutions, Commercial Methods for Powder Production Springer2007年1月1日 This account for the extensive work that has been done on energy auditing system of many manufacturing operations with the aim of improving the design and performance of energy transfer systemsDesign Considerations for the Construction and Powder processing often involves bulk powders, additives, or ingredients being milled for particle size reduction A mill or grinder uses a mechanical action to break the material and reduce it to the required size This may encompass a Grinding Milling Powder ProcessSolutions
.jpg)
Advancements in ore powder production process equipment:
Key Components of Ore Powder Production Equipment: 1 Crushers The initial step in ore powder production is the reduction of ore size, which is accomplished by crushers Jaw crushers, cone crushers, and impact crushers are commonly used to break down the ore into manageable pieces 2 Grinding Mills Grinding mills are central to the powder Ball Mill Grinding Process Handbook Free download as PDF File (pdf), Text File (txt) or read online for free This document provides guidance on ball mill grinding processes It covers topics such as ball mill design including length to diameter ratios, percent loading, critical speed, and internals evaluation Methods for assessing ball charge, wear rates, and liner management are Ball Mill Grinding Process HandbookThis paper presents a review of comill processing, for the production of highefficiency inhalation therapies, including the jet mill, mechanofusion, or ball mill methodologies We investigate the different techniques, additives, and drugs studied, and impact on performance in DPI systemsA review of comilling techniques for the production of high 2017年4月3日 This paper presents a review of comill processing, for the production of highefficiency inhalation therapies, including the jet mill, mechanofusion, or ball mill methodologiesA review of comilling techniques for the production of high dose
.jpg)
The Art of Milling Metrohm
Required Fineness A frequent requirement is to "grind the sample to fine powder" The term "powder", however, is not precise Washing powder, coffee powder or baking powder are bulk materials which are all characterized as "powders", although they 2015年12月31日 Request PDF Quality requirements of iron ore for iron production The blast furnace (BF) ironmaking process is currently the dominant process for providing steelmaking raw materials worldwideQuality requirements of iron ore for iron production2019年9月1日 Powder origins and characteristics Understanding how metal powders are made can inform an understanding of how they behave Metal powders are typically produced using an atomisation process, whereby the metal is heated until molten and either gas or water is jetted at the stream to break up the liquid into smaller particlesUnderstanding metal powder requirements for Additive This has been for long the most widely used method for the production of iron powder Selected ore is crushed, mixed with carbon, and passed through a continuous furnace where reaction takes place leaving a cake of sponge iron which is then further treated by crushing, separation of nonmetallic material, and sieving to produce powderPowder Metallurgy – Powder Processes (Solid State Reduction
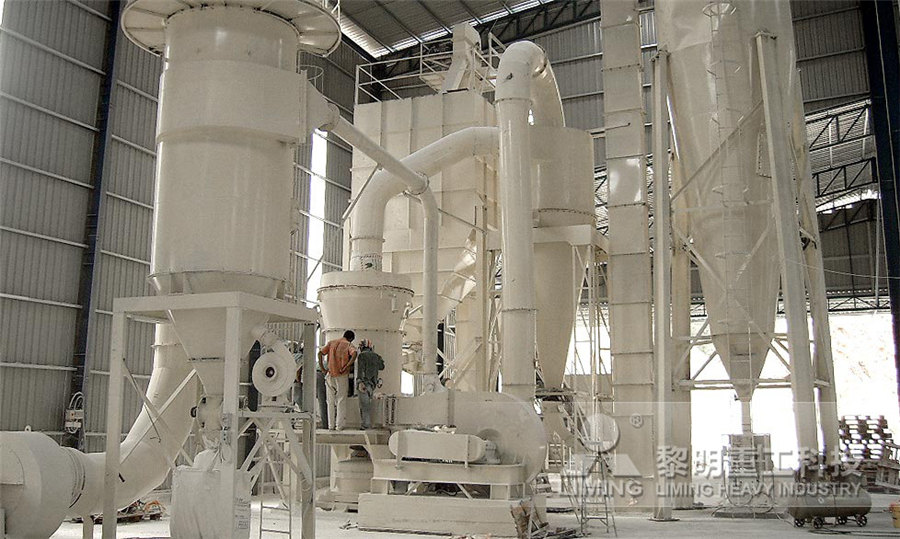
(PDF) i) Direct Reduced Iron: Production
2016年3月30日 In book: Encyclopedia of Iron, Steel, and Their Alloys (pppp 10821108) Chapter: i) Direct Reduced Iron: Production; Publisher: CRC Press, Taylor and Francis Group, New York2023年10月17日 Factors for choosing a suitable ore powder grinding mill 1 Raw material characteristics: Different raw materials have different hardness, humidity and grinding and crushing properties, and the corresponding ore How to choose a suitable ore powder grinding mill?SBM ultrafine powder technology co,ltd Is China's excellent ore mill supplier Our main products include ultrafine vertical roller mill, ultrafine grinding mill, stone powder production equipment, Welcome to consult +17 [ SBM Ultrafine Powder Technology Industrial 2021年2月1日 The ore used in this study was provided by Eti Maden Operations General Directorate in Ankara, Turkey The ore was firstly crushed in a laboratory jaw crusher and then ground in a laboratory ball mill The milled ore was subjected to particle size analysis by using a laser diffraction particle analyzer (Malvern Mastersizer 2000)Production of mixed rare earth oxide powder from a thorium
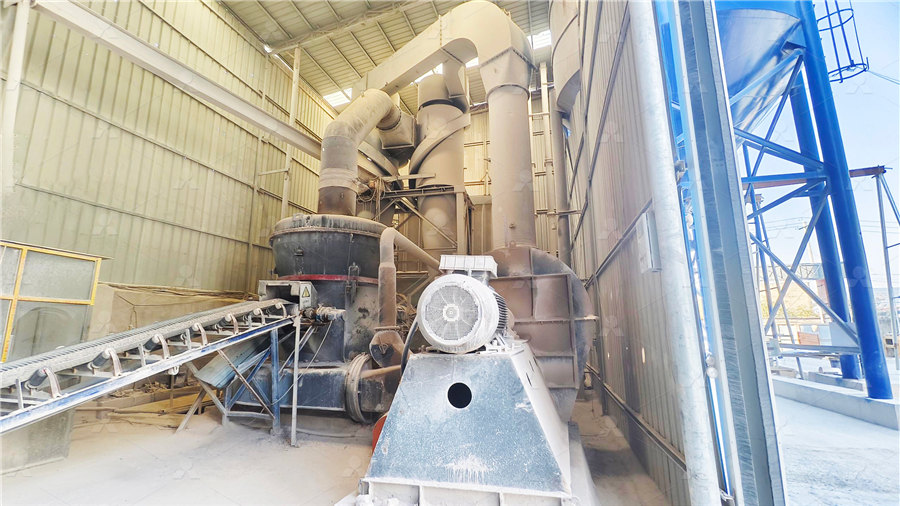
From ore to dore: Four main processes in gold production
2021年11月5日 Today, Metso Outotec can offer processes and equipment that cover the full gold value stream from ore to dore This includes all three main oxidative processes for the treatment of refractory gold concentrates – BIOX, pressure oxidation, and roasting – as well as the equipment for ultrafine grinding as a fourth, nonoxidative treatment optionThe required power consumption of a grinding mill based on the calculations shown above can be estimated thanks to this free Excel calculator : Calculation Tool Grinding Mill Power Calculation Warning : this calculator is provided to illustrate the concepts mentioned in this webpage, it is not intended for detail design Grinding power : step by step calculation PowderProcess2024年2月26日 Oxidised pellets have become an indispensable highquality charge for blast furnaces Nevertheless, highquality pellet feeds are becoming scarcer and scarcer To broaden the range of sources of pellet feeds and reduce the production cost of pellets, more steel mills are predicted to use coarse iron ore fines with a relatively low iron grade and low impurities for the Grinding of Australian and Brazilian Iron Ore Fines for LowCarbon 2022年4月20日 Classification: Limestone is processed into finished products of various specifications through impact crushing according to user requirementsThe particle shape is good and can be classified by vibrating screen The particle size of limestone crushing is very small after coarse crushing and medium and fine crushingLimestone crushing and grinding production line SBM Ultrafine Powder
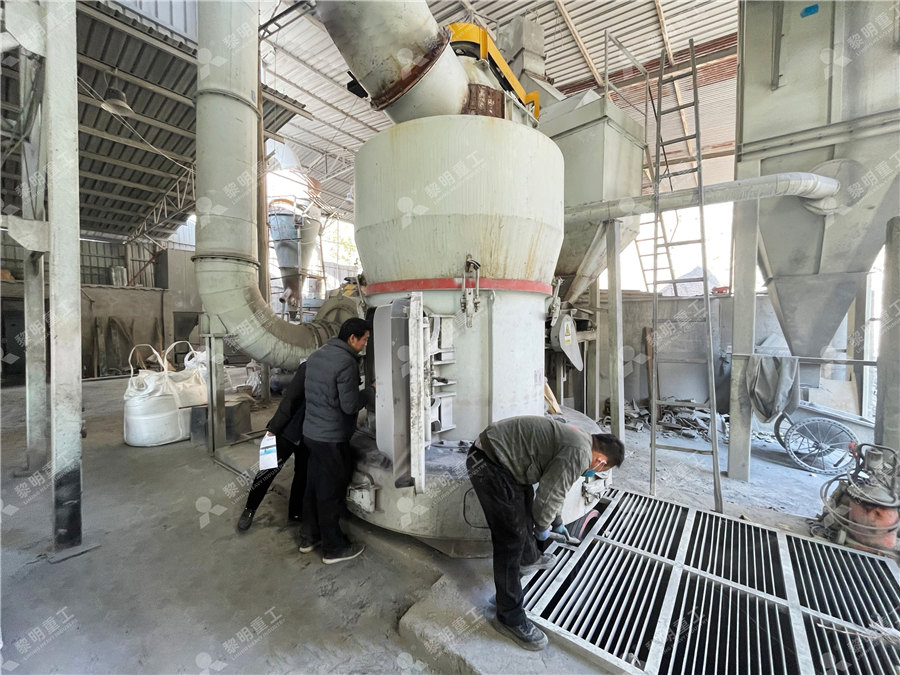
Monitoring ore loss and dilution for minetomill integration in
However, ore below the pay limit adds variation to the mill grade as increased mill throughput will be required to make up for the loss of gold, and that impacts on the recovery in the plant It is against these perspectives and findings of this study that the MCF should be seen as a method that identify the real problems underground and when these are addressed, the profitability of Required Fineness A frequent requirement is to "grind the sample to fine powder" The term "powder", however, is not precise Washing powder, coffee powder or baking powder are bulk materials which are all characterized as "powders", although they Retsch: The art of Milling2021年9月20日 3 Powder Production Milling techniques can include: (1) attritor ball milling that can be categorized as dry grinding or wet grinding, using regular speed (to 400 rpm) or high speed (400–1800 rpm) attritors [10,16]; (2) roll milling []; (3) planetary type [7,13]; (4) disc milling [10,18,19]Powder production mostly involves fracturing cleaned and dried chips/swarf; From Machining Chips to Raw Material for Powder Metallurgy—A The grinding medium in the mill repeatedly impacts and grinds the material by virtue of the kinetic energy obtained when the mill rotates The crushed material is discharged into the suction tank through the tail of the ball mill, and then Ball Mill and Air Classifier Production Line ALPA
.jpg)
Powder Processing in Pharmaceutical Applications—InDepth
In all production processes of solid dosage forms, powders with a multitude of distributed properties must be processed Starting with their handling for dispensing and weighing, over blending, dosing, comminution, and granulation, up to capsule filling or tableting, powder properties crucially determine the process performance and product qualityAt the heart of steel production lies the intricate process of ironmaking, where iron ore is transformed into molten iron and eventually alloyed to create various grades of steel This article delves into the journey from ore to alloy, exploring the technologies, challenges, and innovations that shape modern ironmaking 1From Ore to Alloy: Navigating Ironmaking in Modern Steel Production2021年1月1日 Mill Scale, generated in a rolling steel mill can be a potential material for iron powder production Mill scale is a combination of different oxides like Hematite (Fe 2 O 3), Magnetite (Fe 3 O 4), and Wustite (FeO) [2], [3]Besides, this multioxide mill scale's conversion into single oxide (Fe 2 O 3) is the bestsuited route for further reduction into iron powder due to Overview on production of reduced iron powder from mill scale 2023年6月27日 Metal fragments can be used to produce new metal products and can be recycled to reduce waste and conserve natural resources [40,41,42]Machining chips are estimated to account for a significant portion (137% aluminum and 146% steel) of the trash created by all manufacturing processes globally []This includes metal waste generated from Producing Metal Powder from Machining Chips Using Ball Milling
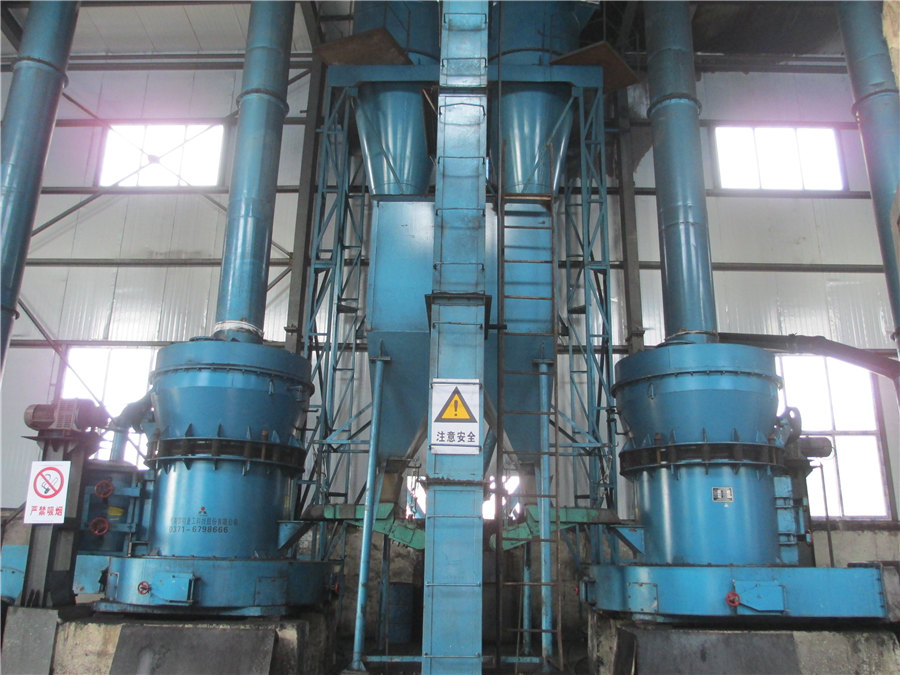
Frequent Asked Questions about Powder Milling and Sizing Equipment
However, it is not just about the mill, but also the screen type and impeller that are selected too We help our customers with their options by sharing our ‘Particle Size Card’ this sizing chart ties the target particle size to the mill type and the size of round or grater hole screen required in 2016年2月1日 The purpose of this study is to understand how ore loss and dilution affect the mine call factor, with the aim of subsequently improving the quality of ore mined and fed to the millMonitoring ore loss and dilution for minetomill integration in 2023年6月27日 Metal scrap: (a) scrap metal from turning; (b) scrap metal from grinding; (c) scrap metal from milling [48] (PDF) Producing Metal Powder from Machining Chips Using Ball used for many years in the production of iron powder by carbon re duction of mill scale Iron powder is the only powder of interest to us made by this process today Reduction of Oxides with Gases A simple and common commercial method is applied for pow ders whose oxides can be reduced by the reducing gases, H2 and mercial Methods for Powder Production Springer

Design Considerations for the Construction and
2007年1月1日 This account for the extensive work that has been done on energy auditing system of many manufacturing operations with the aim of improving the design and performance of energy transfer systemsPowder processing often involves bulk powders, additives, or ingredients being milled for particle size reduction A mill or grinder uses a mechanical action to break the material and reduce it to the required size This may encompass a Grinding Milling Powder ProcessSolutionsKey Components of Ore Powder Production Equipment: 1 Crushers The initial step in ore powder production is the reduction of ore size, which is accomplished by crushers Jaw crushers, cone crushers, and impact crushers are commonly used to break down the ore into manageable pieces 2 Grinding Mills Grinding mills are central to the powder Advancements in ore powder production process equipment: Ball Mill Grinding Process Handbook Free download as PDF File (pdf), Text File (txt) or read online for free This document provides guidance on ball mill grinding processes It covers topics such as ball mill design including length to diameter ratios, percent loading, critical speed, and internals evaluation Methods for assessing ball charge, wear rates, and liner management are Ball Mill Grinding Process Handbook
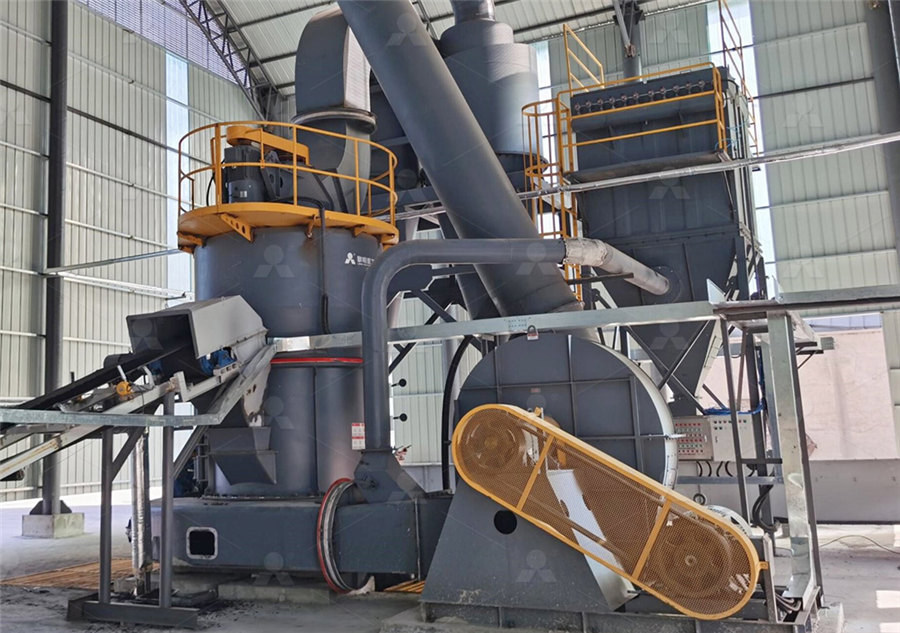
A review of comilling techniques for the production of high
This paper presents a review of comill processing, for the production of highefficiency inhalation therapies, including the jet mill, mechanofusion, or ball mill methodologies We investigate the different techniques, additives, and drugs studied, and impact on performance in DPI systems2017年4月3日 This paper presents a review of comill processing, for the production of highefficiency inhalation therapies, including the jet mill, mechanofusion, or ball mill methodologiesA review of comilling techniques for the production of high dose Required Fineness A frequent requirement is to "grind the sample to fine powder" The term "powder", however, is not precise Washing powder, coffee powder or baking powder are bulk materials which are all characterized as "powders", although they The Art of Milling Metrohm2015年12月31日 Request PDF Quality requirements of iron ore for iron production The blast furnace (BF) ironmaking process is currently the dominant process for providing steelmaking raw materials worldwideQuality requirements of iron ore for iron production
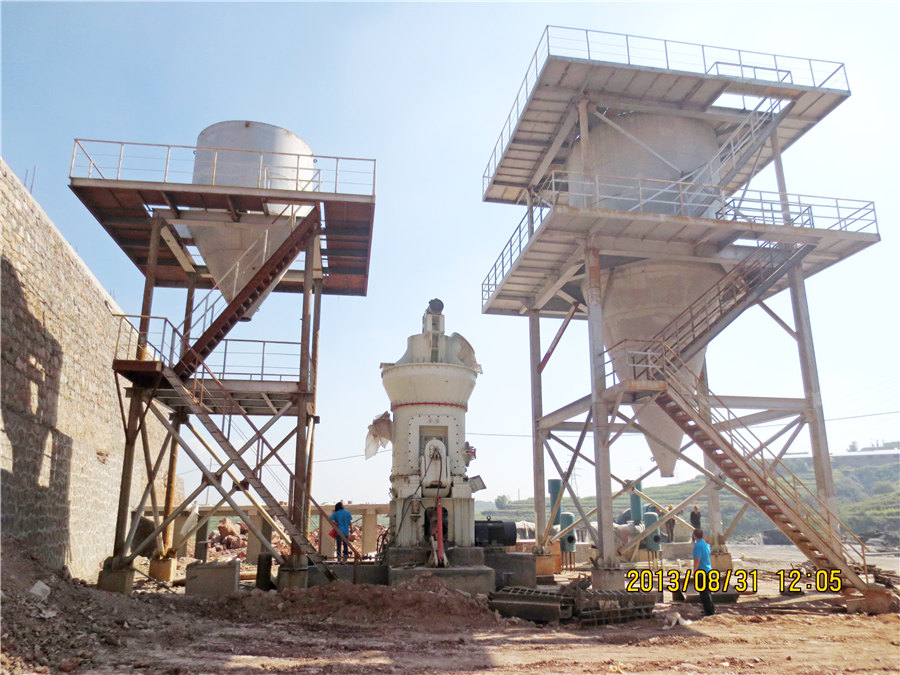
Understanding metal powder requirements for Additive
2019年9月1日 Powder origins and characteristics Understanding how metal powders are made can inform an understanding of how they behave Metal powders are typically produced using an atomisation process, whereby the metal is heated until molten and either gas or water is jetted at the stream to break up the liquid into smaller particlesThis has been for long the most widely used method for the production of iron powder Selected ore is crushed, mixed with carbon, and passed through a continuous furnace where reaction takes place leaving a cake of sponge iron which is then further treated by crushing, separation of nonmetallic material, and sieving to produce powderPowder Metallurgy – Powder Processes (Solid State Reduction