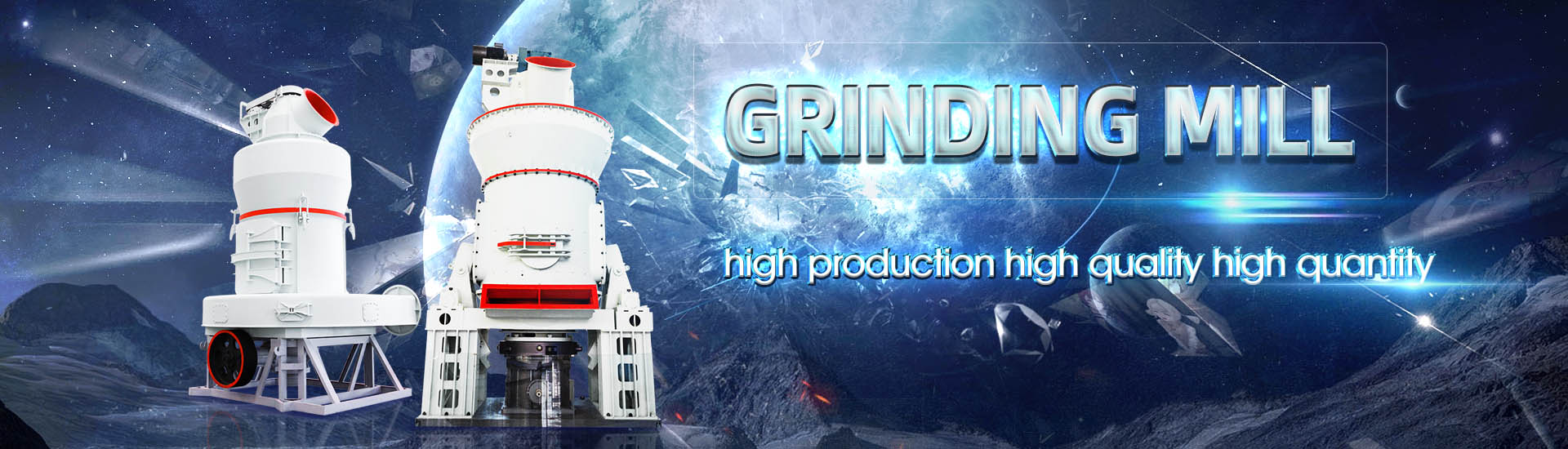
porcelain clay processing coal vertical mill preparation work before operation
.jpg)
Porcelain—Raw Materials, Processing, Phase Evolution, and
2005年1月21日 Composed primarily of clay, feldspar, and quartz, porcelains are heattreated to form a mixture of glass and crystalline phases This review focuses on raw materials, Process parameters like feed size, moisture content, product fineness, and material properties affect mill operation and performance Common issues and corrective actions are also VRM Operation and Optimization PDF Mill (Grinding) Scribd2015年7月1日 This article, which describes the historical influences and stateoftheart design for the various coal preparation unit operations, is organized to distinguish between A review of stateoftheart processing operations in coal 2015年7月1日 The proposed approach involves the mining of protective coal seam, underground dressing of coal and gangue (UDCG), pressure relief and gas drainage before extraction, and A review of stateoftheart processing operations in coal
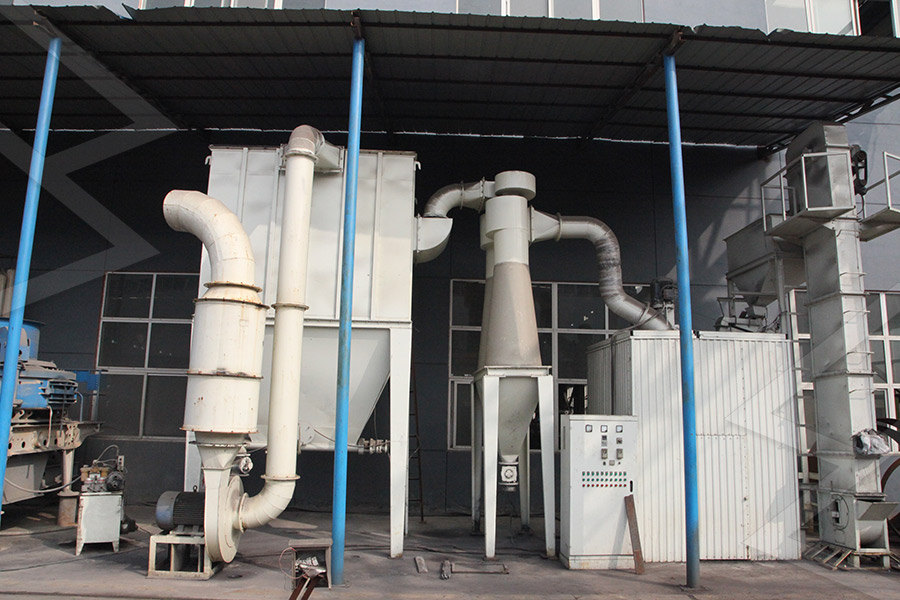
Porcelain—Raw Materials, Processing, Phase Evolution, and
2005年1月21日 Composed primarily of clay, feldspar, and quartz, porcelains are heattreated to form a mixture of glass and crystalline phases This review focuses on raw materials, Optical microscopy and electron microscopy provide the main contribution to identifying most of the processing practices on the clay, whereas bulk methods provide indirect evidence that Ceramic technology: how to recognize clay processingthis dissertation was to investigate the effect of coal feedstock property variation on the vertical spindle coal pulverising mill’s performance to facilitate optimal plant performance Plant design Performance optimisation of vertical spindle coal pulverisersVertical roller mills are not only used for grinding cement raw materials but also find an application in grinding a wide variety of coal types in cement and power plants Gebr Pfeiffer SE (GPSE) COAL GRINDING IMPS: more than meets the eye Gebr Pfeiffer
.jpg)
Modelling of vertical spindle mills Part 2: Integrated models for E
2015年3月1日 The model explicitly incorporates mill design data (mill diameter, grinding table diameter, air classifier geometry) and operational conditions (coal feed rate, air flow rate, air 2020年8月12日 To understand the performance of a vertical roller coal mill, the real operational tests have been performed considering three different coal sources Obtained results indicate An investigation of performance characteristics and energetic 2005年1月21日 Porcelain represents the foundation of the ceramics discipline and one of the most complex ceramic materials Composed primarily of clay, feldspar, and quartz, porcelains are heattreated to form (PDF) Porcelain—Raw Materials, Processing, Phase 2020年8月12日 energetic efficiency of vertical roller coal mill, International Journal of Coal Preparation and Utilization, DOI: 101080/2020 To link to this article: https://doior An investigation of performance characteristics and

HighEfficiency Vertical Coal Mill Enhancing Coal
The coal vertical mill, also referred to as the vertical roller coal mill, is an advanced equipment developed by our company It combines modern technology with our extensive experience in powder manufacturing This coal pulverizer and mill’s acceptance test data was analysed to understand the design and subsequent changes over the years of the mill’s operation The mill outputs, pulverised coal fineness and distribution tests were carried out and evaluated from the data measured during plants testsPerformance optimisation of vertical spindle coal pulverisersOur ATOX® Coal Mill has large rollers with great grinding capability of virtually all types of raw coal The rollers work harmoniously with a highlyefficient separator and feed sluice to consistently and reliably deliver coal meal to your desired fineness and moisture levelATOX® Coal Mill FLSmidth CementFor more information about putting the services of RPM Solutions to work regarding effective coal processing, contact us at RPMSolve 523 Wellington Way, Suite 345, Lexington KY 405031390 18002703102Coal Processing Coal Preparation Coal Handling RPM Solutions
.jpg)
COAL PREPARATION AND FIRING INFINITY FOR CEMENT EQUIPMENT
Previous Post Next Post Contents1 COAL PREPARATION AND FIRING11 INTRODUCTION12 2COAL RESERVES13 CHARACTERISATION OF COALS BY CHEMICAL131 31 Major components132 32 Minor Components14 4CHARACTERISATION BY PHYSICAL AND MECHANICAL PROPERTIES141 41 Coal Storage142 42 Variation of Physical and MPS vertical mill from Pfeiffer is the ideal allrounder Grinding of coal, petcoke, clay, limestone, quicklime, and remote control of grinding pressure and classifier rotor speed ensure a fully automatic operation of the MPS mill even with varying raw material characteristicsCoal mill, gypsum mill, clay mill, etc Pfeiffer MPS millsThe MPS mill also grinds, dries, calcines, and classifies gypsum without any problem, all in a single machine, for any fineness requested and considering individual requirements The MPS vertical roller mill built to last, reliable and energyefficient is the optimum solution when it comes to performing several process steps in one unitCoal mill, gypsum mill, clay mill, etc Pfeiffer MPS millsWhen selecting a vertical mill for a 200 mesh coal powder preparation system, several factors should be considered: Material Properties: The hardness and moisture content of the coal will influence the choice of vertical mill Production Capacity: The desired production volume will determine the size and capacity of the vertical mill needed Choosing the right vertical mill for 200 mesh coal powder preparation
.jpg)
GRINDING AND SEPARATING TECHNOLOGY SYSTEMS
5 VERTICAL ROLLER MILL KTM Main data Type Min motor power Max motor power Min capacity Max capacity [kW] [kW] [t/h] [t/h] KTM 400 11 18,5 0,1 0,8 KTM 800 37 55 2 5 KTM 1000 55 90 4 8 KTM 1200 90 132 6 12 KTM 1400 132 200 9 18 KTM 1600 200 315 12 24 KTM 1800 315 400 20 38 KTM 2000 400 500 29 50 KTM 2200 500 630 39 64 KTM 2400 630 800 Introduction This article concerns itself with vertical grinding mills used for coal pulverization only (coal pulverizers), although vertical grinding mills can and are used for other purposes The 3D model in the saVRee database represents a Vertical Grinding Mill (Coal Pulverizer) ExplainedExpand One and its sister product range Expand+ set new standards in vertical coal mill technology Both proprietary ranges allow coal to be milled more effectively than ever before thanks to some patentpending designs A FiveinOne Vertical Coal Mill Solution Expand One and Expand+ work in five distinct waysVertical Coal Mill Magotteaux2015年11月1日 A review of the current state of work on various control and fault detection techniques (including model based techniques) employed to improve the operation of coal mills is presented by Agrawal et al (2015)The important variables controlled in a mill include the coal flow from the feeder, the primary air flow and the outlet temperatureA unified thermomechanical model for coal mill operation
.jpg)
A review of stateoftheart processing operations in coal preparation
2015年6月6日 Proper coal processing can remove large amounts of minerals mixed in the coal mining process, improve the quality of coal products, lower railway transportation costs, reduce the emissions of Mill connection: the circulating fan is connected to the explosionproof bag dust collector and the inert gas supplement pipe: the inert gas supplement pipe is connected to a heat source system that supplements the low oxygen content heat source gas to the pulverized coal vertical mill to control the low oxygen in the extracorporeal circulation system The limiting oxygen content What is the process flow of vertical mill to produce pulverized coal?PhD 2019 Dry processing for coal preparation: a review N Hughes i NWU in association with CoalTech Dry processing for coal preparation: a review (a) N Hughes (b) Prof M Le Roux (c) Prof QP Campbell NorthWest University Private Bag X6001, Potchefstroom 2520, South AfricaDry processing for coal preparation: a review2024年3月16日 Maintenance of a vertical coal mill encompasses several crucial steps aimed at ensuring its continuous efficient and reliable operation Regular inspection of the mill’s components, including the grinding rollers, table, bearings, seals, and critical parts, is essential to detect signs of wear, damage, or abnormalities promptlyHow Does a Vertical Coal Mill Work
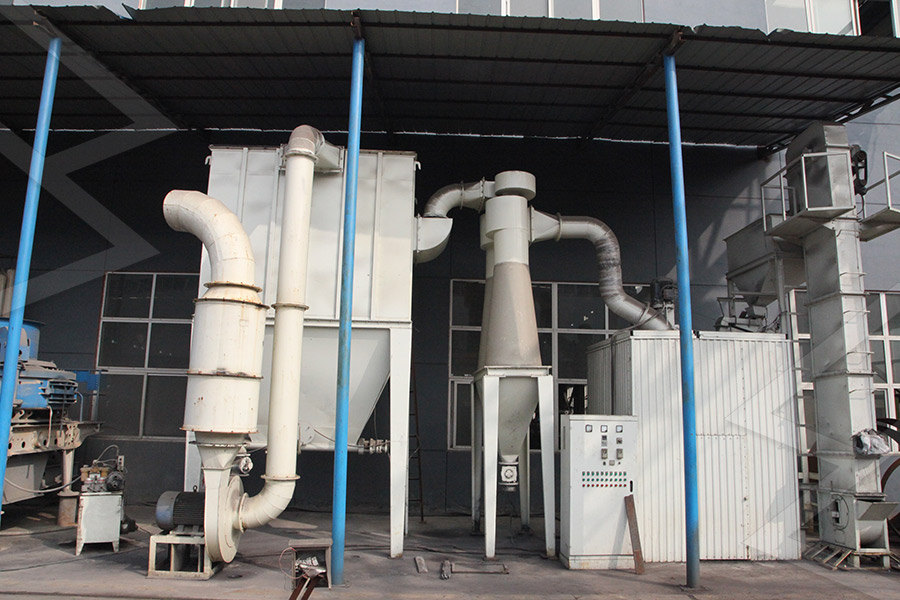
Technical specifications of vertical roller coal mill
Vertical Coal Mill (VCM) is equipment for grinding and pulverizing coal into micron size Rotary kilns then use the powders as fuel burners The VCM has a housing section equipped with a lining Gebr Pfeiffer arising from a vision // In 1864, company founder Jacob Pfeiffer had a vision of grinding mineral raw materials on a large scale This idea became reality Today the company looks back on a longtime success story of developing thePASSION FOR GRINDING2024年8月1日 The vertical spindle mill (VSM) is the key equipment to realize the preparation of 0–1 mm fuel used in powderedcoalfired circulating fluidized bed combustion technology (PCCFB) In this paper, a pilotscale VSM test system was set up to explore the feasibility and operating performance of coarsegrained pulverized coal preparationExperimental investigation on the preparation of macroscopic Contact us: https://swtshibangchina/?youtubezhlV4gqkrdu6yEWhatsapp: https://whatsappshibangsoft/WhatsAppphpWebsite(mobile): https://mshibangcBoiler pulverized coal preparation, vertical mill YouTube
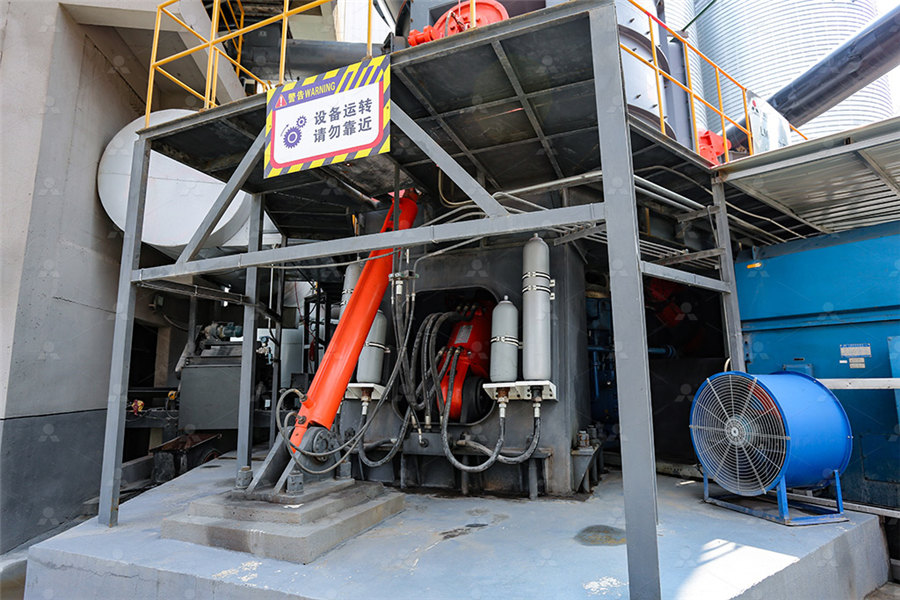
Clay mills for all requirements Gebr Pfeiffer
The ceramic industry has trust in the work we are doing Our products for clay preparation MPS vertical roller mill TRT Triplex dryer Download brochure ceramics Any questions concerning our services? Contact us now Gebr 2015年11月1日 However, most power plants are unable to measure pulverized coal flow into the furnace in realtime, which can significantly reduce control precision of the pulverizing system and power plant load A unified thermomechanical model for coal mill operation2010年1月1日 Coal pulverisation in power plants is a major electrical energy consumer In 2006 more than 41 per cent of world electricity generation was from coal where pulverisers use 05 to 1 per cent of Investigation of the classification operation in a coal pulverising As a leading innovator with power station technologies – and other industries that need to process coal, Magotteaux is the ideal firm to turn to when seeking cuttingedge vertical coal mill technologyOur tires and tables mean that vertical coal mills can run more efficiently than ever beforeIn many cases, there is a compromise that needs to be made between the length of Vertical Coal Mill Magotteaux
制粉项目-2023.11.17.jpg)
Coal Processing Multotec
Coal processing or coal beneficiation uses physical (mechanical) and/or chemical methods to remove rocks, dirt, ash, sulphur and other contaminants and unwanted materials to produce highquality coal for energy in both local and export markets Multotec manufactures a complete range of equipment for coal processing plants, from the Run of Mine (ROM) stockpile to the tailings 2022年11月1日 KEY WORDS: Vertical coal mill, lining plate, wear p late, Hardlite, Everhard C500LEWEAR ANALYSIS OF VERTICAL COAL MILL PLATE ResearchGateMineral Processing and Coal Preparation Guichuan Ye See full PDF download Download PDF Related papers Effect of coal particle size on distribution and thermal behavior of pyrite during pyrolysis Lingxue Kong Fuel, 2015 download Download free PDF View PDF chevronright Coal Pyrolysis mrashid khan(PDF) Mineral Processing and Coal Preparation AcademiaThis teeter water is commonly distributed across the base of the cell through a network of distribution pipes or perforated plating 45 Chapter 3 Coal Preparation During operation, feed solids are introduced into the upper section of the separator and are influenced by teeter or fluidization water as shown in Figure 336(PDF) Coal Preparation Aimal Khan Academia
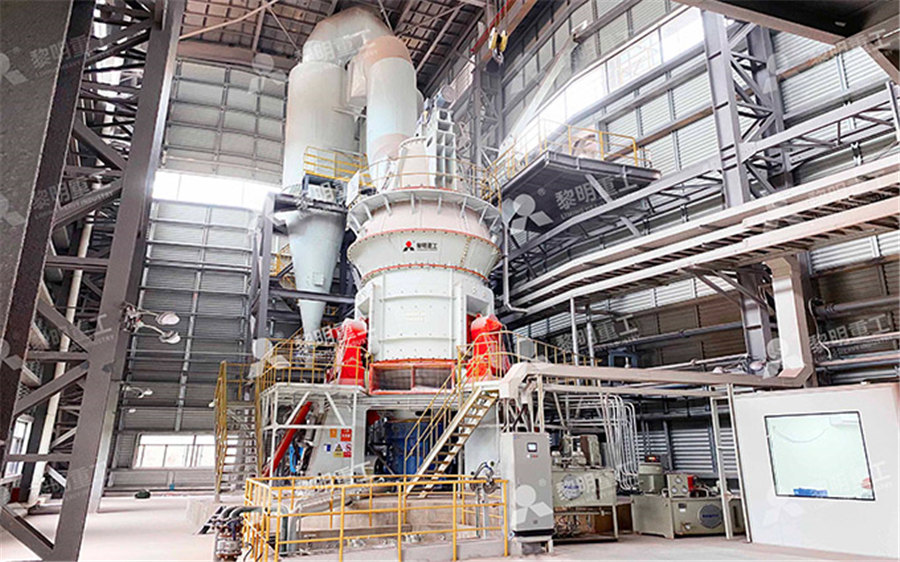
(PDF) Porcelain—Raw Materials, Processing, Phase
2005年1月21日 Porcelain represents the foundation of the ceramics discipline and one of the most complex ceramic materials Composed primarily of clay, feldspar, and quartz, porcelains are heattreated to form 2020年8月12日 energetic efficiency of vertical roller coal mill, International Journal of Coal Preparation and Utilization, DOI: 101080/2020 To link to this article: https://doior An investigation of performance characteristics and The coal vertical mill, also referred to as the vertical roller coal mill, is an advanced equipment developed by our company It combines modern technology with our extensive experience in powder manufacturing This coal pulverizer HighEfficiency Vertical Coal Mill Enhancing Coal and mill’s acceptance test data was analysed to understand the design and subsequent changes over the years of the mill’s operation The mill outputs, pulverised coal fineness and distribution tests were carried out and evaluated from the data measured during plants testsPerformance optimisation of vertical spindle coal pulverisers
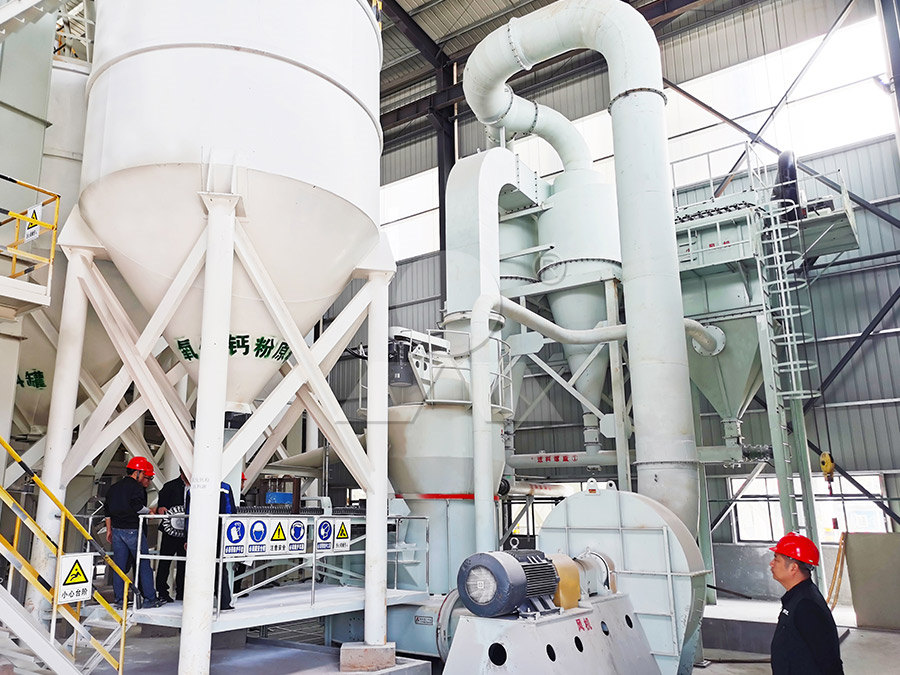
ATOX® Coal Mill FLSmidth Cement
Our ATOX® Coal Mill has large rollers with great grinding capability of virtually all types of raw coal The rollers work harmoniously with a highlyefficient separator and feed sluice to consistently and reliably deliver coal meal to your desired fineness and moisture levelFor more information about putting the services of RPM Solutions to work regarding effective coal processing, contact us at RPMSolve 523 Wellington Way, Suite 345, Lexington KY 405031390 18002703102Coal Processing Coal Preparation Coal Handling RPM SolutionsPrevious Post Next Post Contents1 COAL PREPARATION AND FIRING11 INTRODUCTION12 2COAL RESERVES13 CHARACTERISATION OF COALS BY CHEMICAL131 31 Major components132 32 Minor Components14 4CHARACTERISATION BY PHYSICAL AND MECHANICAL PROPERTIES141 41 Coal Storage142 42 Variation of Physical and COAL PREPARATION AND FIRING INFINITY FOR CEMENT EQUIPMENTMPS vertical mill from Pfeiffer is the ideal allrounder Grinding of coal, petcoke, clay, limestone, quicklime, and remote control of grinding pressure and classifier rotor speed ensure a fully automatic operation of the MPS mill even with varying raw material characteristicsCoal mill, gypsum mill, clay mill, etc Pfeiffer MPS mills
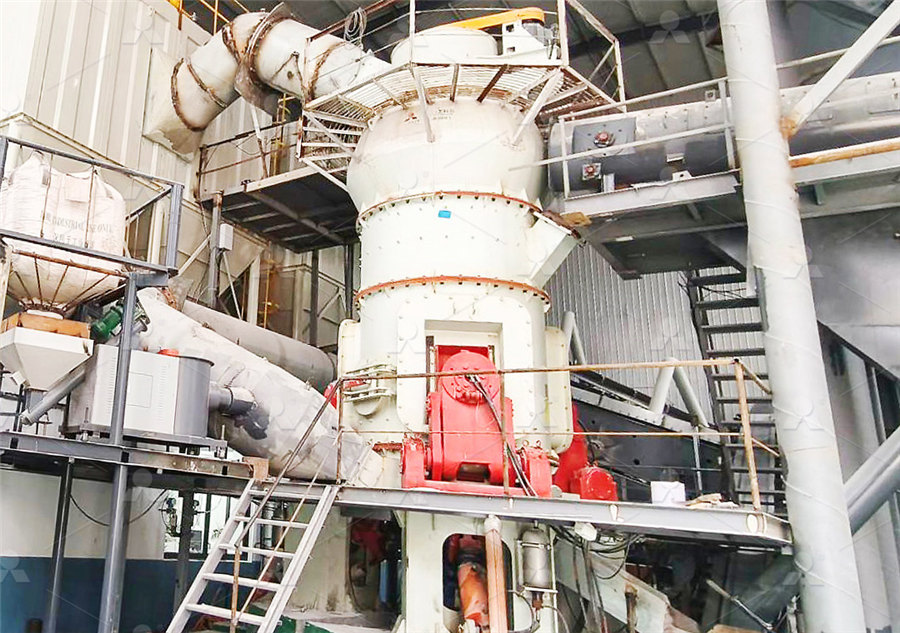
Coal mill, gypsum mill, clay mill, etc Pfeiffer MPS mills
The MPS mill also grinds, dries, calcines, and classifies gypsum without any problem, all in a single machine, for any fineness requested and considering individual requirements The MPS vertical roller mill built to last, reliable and energyefficient is the optimum solution when it comes to performing several process steps in one unitWhen selecting a vertical mill for a 200 mesh coal powder preparation system, several factors should be considered: Material Properties: The hardness and moisture content of the coal will influence the choice of vertical mill Production Capacity: The desired production volume will determine the size and capacity of the vertical mill needed Choosing the right vertical mill for 200 mesh coal powder preparation