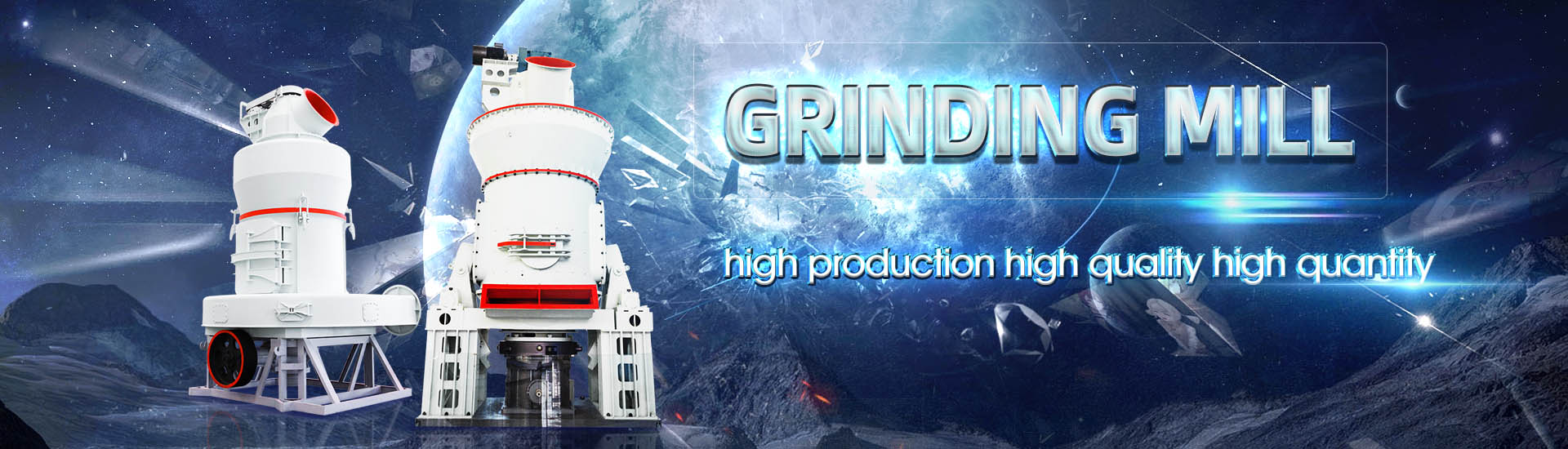
The flow of the grinding mill is blocked
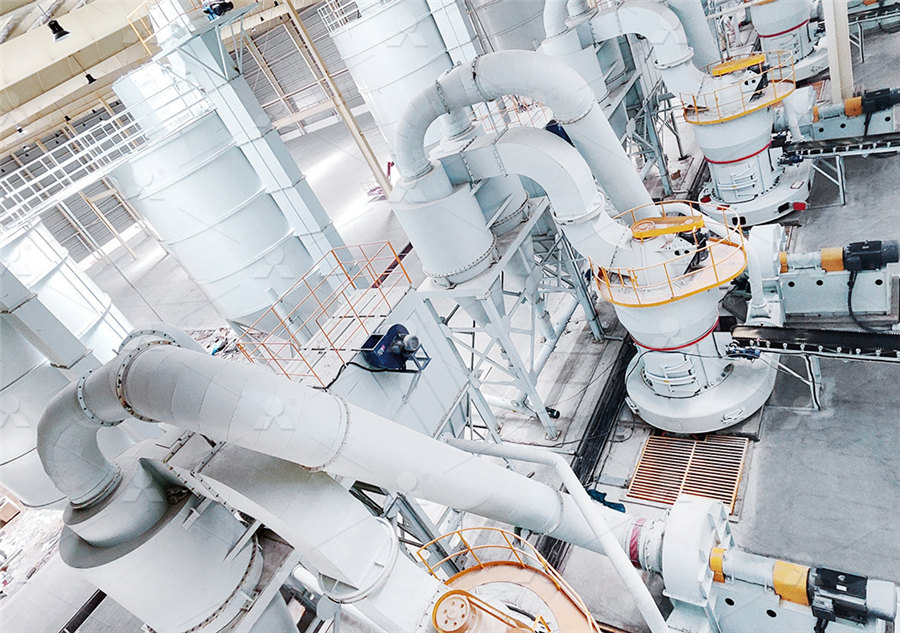
How to resolve the most common hydrocyclone
2020年7月23日 Producing dilute cyclone underflow densities can lead to over grinding in the mill, translating to pay metal (product) recovery losses in flotation Operating cyclones with apex diameters that are too small can lead to cyclone 2015年8月7日 What happens to your circuit? First the extra ore enters the rod mill the density begins to climb and the grind gets coarser You start to get a few rejects Then the heavier density with the courser grind is pumped to the Operating and Troubleshooting a Grinding Circuit2021年11月29日 In fact, clogging is a very common failure of the grinder during grinding, and the main reason is still caused by the operation 1 The feeding speed is too fast and the load increases, causing blockage During the feeding How to deal with the blockage of jet mill ALPA PowderIn wet grinding, the nature of the slurry flow plays an important role in transporting feed rock and ground fines inside the mill and also assists discharge from the mill Operating conditions and impeller design can affect the slurry distribution Slurry pooling and transport issues in SAG mills
.jpg)
Simplified functional block of the mill The flowrates of
The flowrates of ore and water are the main material flows entering in the closed grinding cycle The ore is fed into the mill load by a frequencydriven belt conveyor The water is suppliedThis document provides steps to check air flow through a grinding mill by measuring air velocity and identifying sources of decreased flow or false air entry Key steps include: 1 Measure air velocity at the mill inlet and outlets using an Checking Mill Air Flow PDF Mill (Grinding)2016年6月1日 The control architecture aims to achieve independent control of circuit throughput and product quality, and consists of a nonlinear model predictive controller for grinding mill Throughput and product quality control for a grinding mill circuit A nonlinear modelbased control architecture for a singlestage grinding mill circuit closed with a hydrocyclone is proposed The control architecture aims to achieve independent control of Throughput and product quality control for a grinding mill circuit
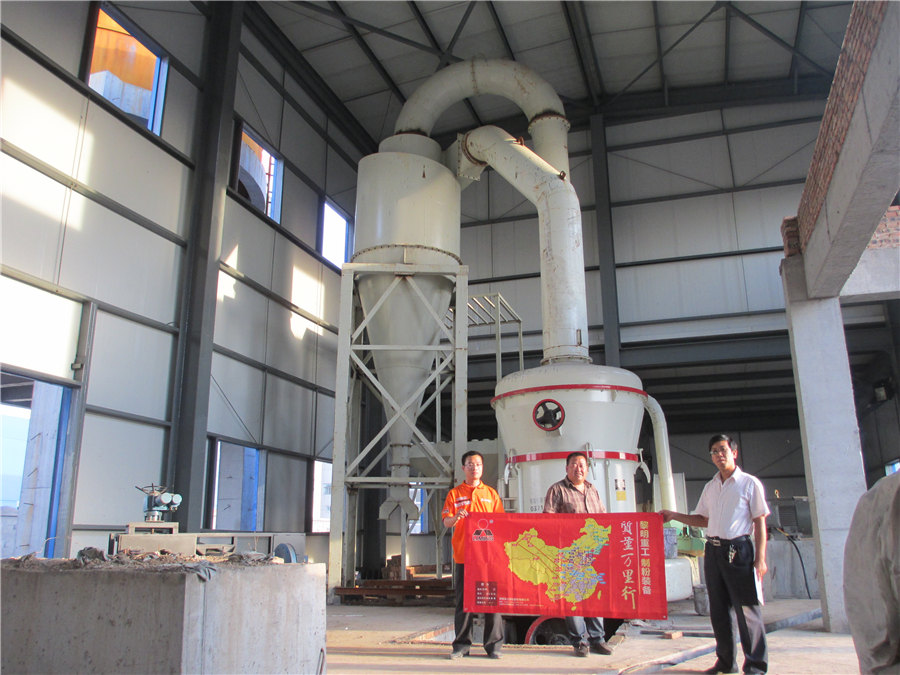
Process control in the grinding circuit Rhosonics
2023年8月11日 Excessive water in the process leads to the production of more middlesize particles, which escape the grinding circuit through the cyclone overflow, decreasing the 1 EFFECT OF GRINDING NOZZLES PRESSURE ON PARTICLE AND FLUID FLOW 2 PATTERNS IN A SPIRAL JET MILL 3 Lewis Scott, Antonia Borissova, Alan Burns and Mojtaba Ghadiri* 4 5 School of Chemical and Process Engineering, University of Leeds, 6 Leeds LS2 9JT, UK 7 8 *Corresponding author: 9 Abstract 10 Spiral jet mills utilise Effect of grinding nozzles pressure on particle and fluid flow Raw mill grinding process is a complicated process in cement industry The effects of unwanted vibrations can be severe It causes a reduction in service lifeFlow diagram of the end discharge mill [18]1 Opencircuit grinding consists of one or more grinding mills without size classification The final ground product discharges directly from the mill Tube mills offer the best design for singlestage opencircuit grinding 2 Two or Types and Characteristics of Common Grinding
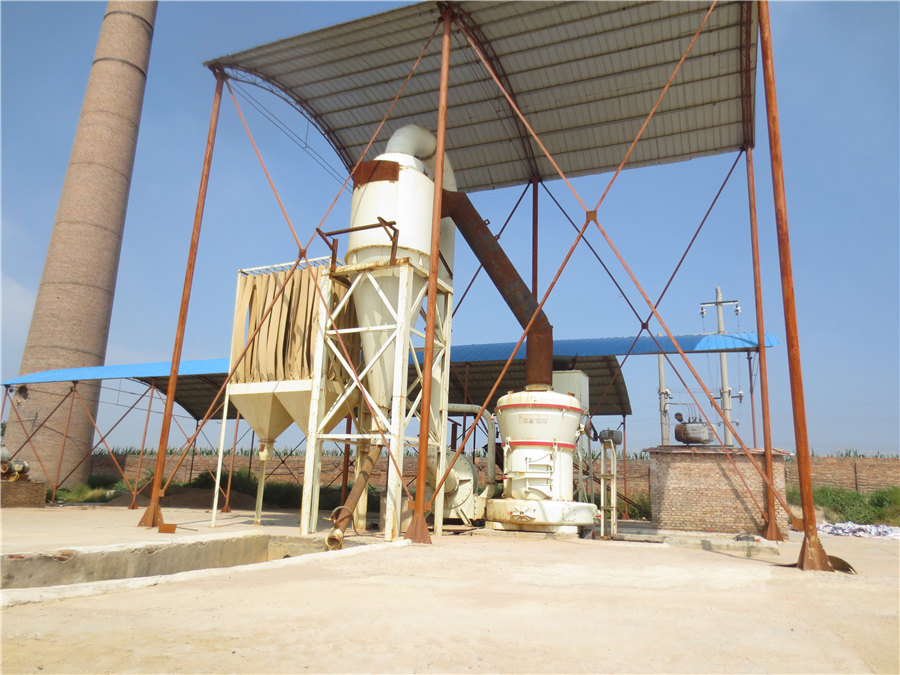
Prediction of the disc wear in a model IsaMill and its effect on the
2011年11月1日 Yang et al (2006) first studied the flow of grinding media in a simplified 14 l laboratory scale Isamill with multiple discs using DEM Jayasundara et al (2006Jayasundara et al Grinding in an air classifier mill — Part II: Characterisation of the twophase flow × Close Log In Log in with Facebook Log in with Google or Flow around the grinding pins 51 Experimental results The measured velocity in the case of the particle laden flow corresponds to the particle velocity in the mill(PDF) Grinding in an air classifier mill Academia2018年11月1日 Other influences of grinding aids on the transport behavior as well as mill retention times are known for the operation of conventional tumbling ball mills (Dombrowe et al, 1982, Sottili and Padovani, 2000) and may be explained by similar powderflowrelated effectsImpact of the powder flow behavior on continuous fine grinding 2011年7月25日 The flow investigations have been performed using a ZPS 100 air classifier mill (Hosokawa ALPINE GmbH) as shown in Fig 1The mill itself consists of a rotating disk with 4 grinding pins at its periphery and an impeller wheel classifier integrated into the top section of Grinding in an air classifier mill — Part I: Characterisation of the
.jpg)
Grinding in an air classifier mill — Part II: Characterisation of
2011年7月1日 Request PDF Grinding in an air classifier mill — Part II: Characterisation of the twophase flow Based on the insights about the air flow within the air classifier mill presented in the CFD MODELLING OF A STIRRED BEAD MILL FOR FINE GRINDING Graeme L LANE CSIRO Minerals, Box 312, Clayton Sth, Victoria 3169 AUSTRALIA ABSTRACT flow in the horizontal stirred mill The various methods are described below In each case the geometry is specified using a multiblock bodyfitted finite volume mesh, and aCFD MODELLING OF A STIRRED BEAD MILL FOR FINE GRINDING2019年11月11日 Flow rate: The unit flow rate of the flour mill is usually expressed in units of contact length of the roller unit, ie kg/cm When the flow rate is too large, the homogeneity of material crushing will be reduced If the flow rate is too small, the feeding state is not normal and the equipment operation is unstableEFFICIENCY IN GRINDING AND ENERGY MANAGEMENT IN 2022年11月17日 The rod mill uses steel bars as the grinding medium, and the materials are in point contact during the grinding process Therefore, compared with the energysaving ball mill, the rod mill has the characteristics of uniform Factors That Affect The Grinding Efficiency of Rod Mill
.jpg)
Flow chart of the grinding and blending process
Download scientific diagram Flow chart of the grinding and blending process from publication: Effective Optimization of the Control System for the Cement Raw Meal Mixing Process: I PID Tuning The document discusses optimization and operation of vertical roller mills (VRMs) Key points include: 1) Continuously monitor and adjust process parameters to find the optimum operating conditions of highest capacity and Optimization of Vertical Raw Mill Operation PDF2023年1月1日 A vertical mill platform for inner circulation is constructed to improve the grinding efficiency A transparent plexiglass grinding chamber is utilized to study the influence of solids density, particle size, solid volume fraction and agitator speed on the variation and transition of flow pattern regimesExperimental studies on the flow pattern regimes of particles Latest Technology of Mill Diaphragms Free download as PDF File (pdf), Text File (txt) or read online for free "Latest technology of mill diaphragms" presented by: Christian Pfeiffer Maschinenfabrik GmbH Sudhoferweg 110 112 59269 Beckum Germany TABLE OF CONTENT: Introduction Requirements for a modern intermediate diaphragm Design Latest Technology of Mill Diaphragms PDF Mill (Grinding)
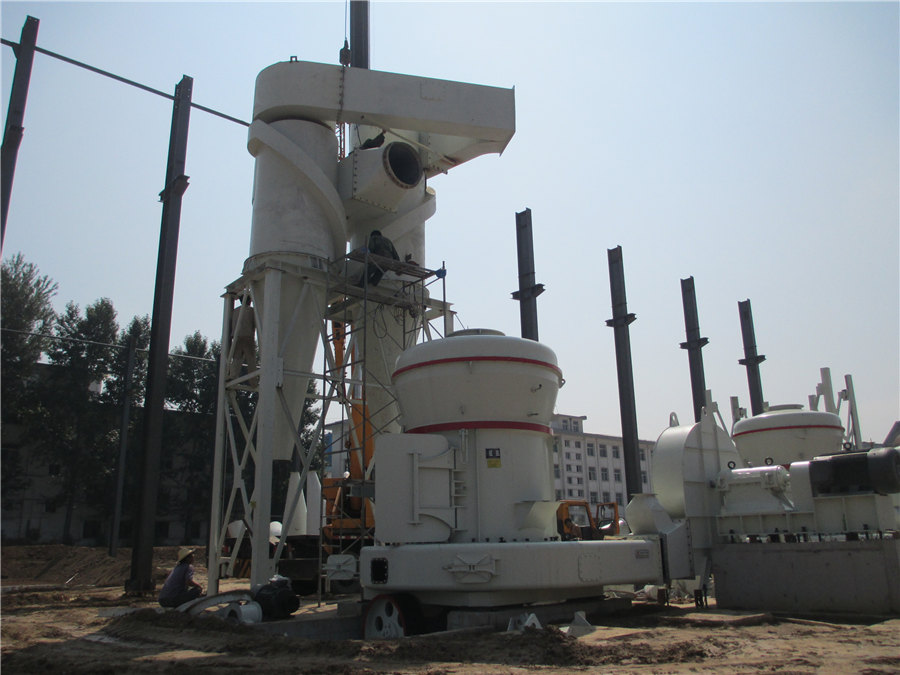
Checking Mill Air Flow PDF Mill (Grinding) Mechanical Fan
Checking Mill Air Flow Free download as PDF File (pdf), Text File (txt) or read online for free This document provides steps to check air flow through a grinding mill by measuring air velocity and identifying sources of decreased flow or false air entry Key steps include: 1 Measure air velocity at the mill inlet and outlets using an anemometer and compare to expected values to Test rig—grinding installation with electromagnetic mill The grinding installation used in this research is shown in Fig 1 Feed material is supplied with a screw feeder and enters the working chamber of the mill There, it is subjected to very intensive grinding by small ferromagnetic rods moved by rotating electromagnetic fieldModel and simulator of inlet air flow in grinding installation with Grinding media, also known as grinding balls, are the materials that facilitate the grinding process within the ball mill They are typically made of steel and are inserted into the mill through a charging port The grinding media come into contact with the materials, causing friction and impact, which breaks them down into smaller particlesExploring the components of ball mills NEWS SMMVIK MachineryA numerical model based on the discrete element method (DEM) was developed to study flow of grinding media in IsaMill mixing pattern and power draw from those measured from a 1:1 scale lab mill Then the flow properties were analysed in terms of flow pattern, flow velocity, force field and power drawDEM simulation of the flow of grinding media in IsaMill
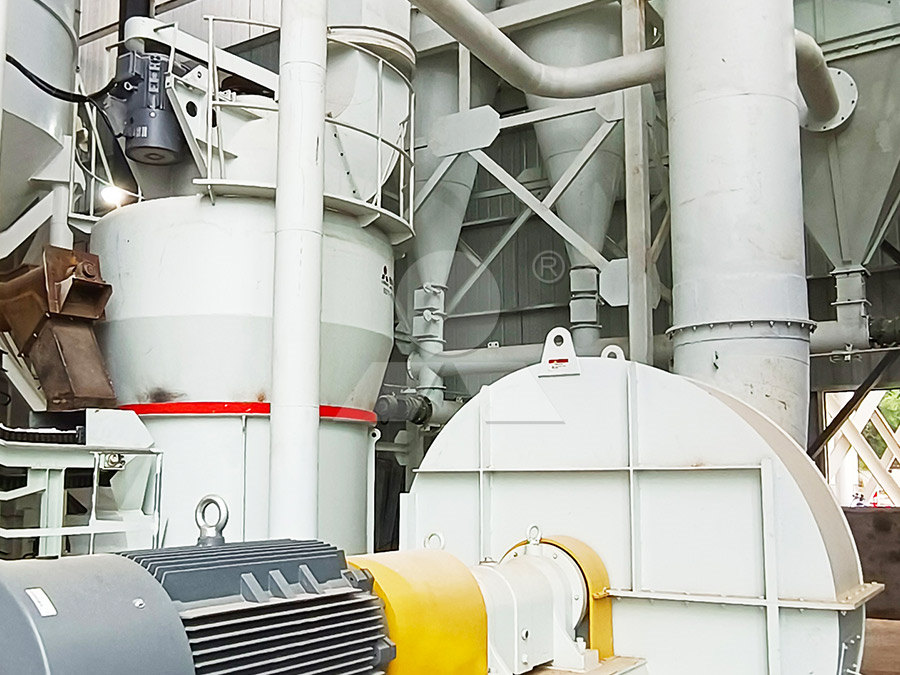
Using the eightroller mill in the purifierless mill flow
2014年12月20日 Double grinding of intermediate streams before sieving has been one of the most notable process developments in flour milling (Owens 2001) The eightroller mill (8 rolls in one housing), also known as two high or double high roller mill, provides two grinding passages without any intermediate siftingProcess Flow Description Latest Free download as Word Doc (doc / docx), PDF File (pdf), Text File (txt) or view presentation slides online The document describes the process at the Tarkwa Gold Mine CIL process plant Ore is Process Flow Description Latest PDF Mill 2022年5月18日 A schematic view of the spiral jet mill used in the experiments is shown in Fig 1, which includes the dimensions Fig 2 shows a schematic view of all elements of the apparatus Air is supplied from a large capacity compressor (capacity: 225 l, pressure: 7 bar, flow rate: 18 cfm) through Ball valve0, a moisture separator and a pressure regulator to the system (shown Analysis of grinding in a spiral jet mill Part 2: Semibatch grinding This document discusses optimizing cement separator and ball mill systems through periodic testing and evaluation It provides guidance on when and why to conduct optimization, including abnormal operations, poor performance, or Cement Separator Ball Mill Optimization PDF Mill
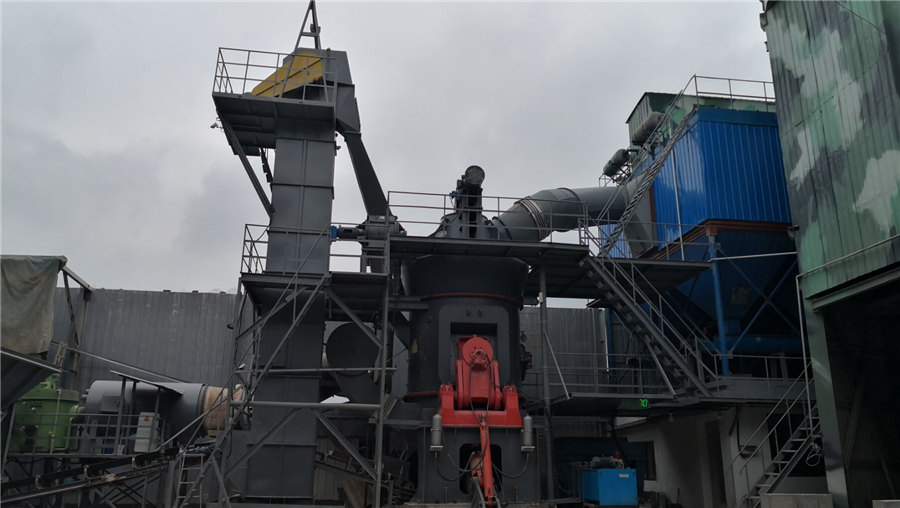
Analysis of grinding in a spiral jet mill Part 1: Batch grinding
2021年2月15日 The spiral jet mill has several additional advantages over other grinding mills which include: production of particles smaller than 10 μ m with a narrow size distribution, low temperature rise due to high gas throughputs, low maintenance since the mill has no mechanical moving parts, suitability for particles with a wide range of material hardness and low SikaGrind®180 MY is added into the grinding mill (first or or sprinkled / dropped onto the clinker (raw material) on the conveyor belt Suitable dosage pumps with adjustable flow rates should be used for accurate dosing Note: Periodically, the end of the additive tube should be checked to ensure, that it is not blocked with cement SikaGrind®180 MY Grinding aid and quality improver for the 2015年7月29日 It also maintains an even steady flow of material through the mill Once the ore has been mixed with water and is in a slurry form, it will flow along with the water The bad side of the water is that it takes up space The more water that is Effect of Water Density on Grinding Mill 911Metallurgistthe mill entrance or directly into the grinding mill Suitable dosage pumps with adjustable flow rates should be used for accurate dosing Note: Periodically, the extremity of the additive tube should be checked to ensure that it is not blocked with cement clinker/dust!SikaGrind®709 Activator MM
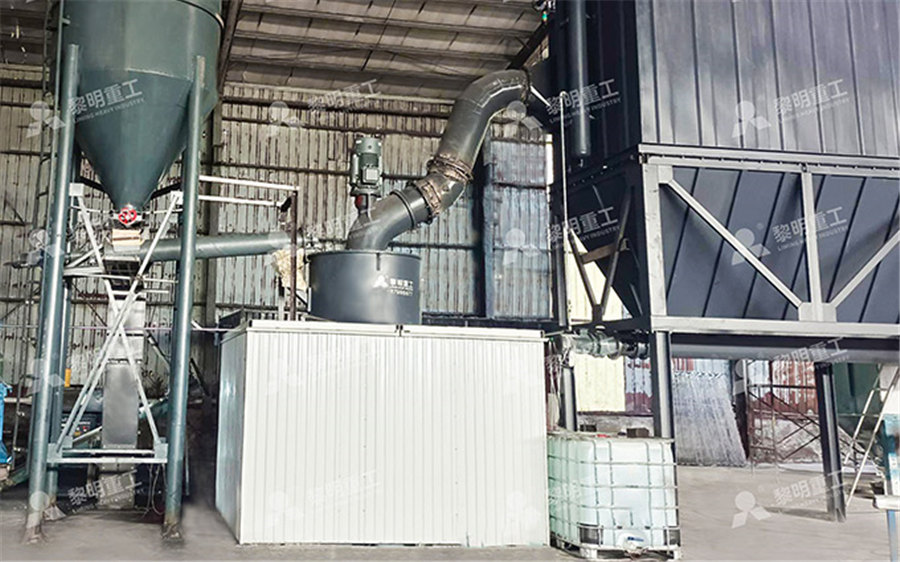
Grinding and Dispersing Nanoparticles American Coatings
200 nanometers and the requirements for grinding large particles to a nanometer range PARTICLE SIZE CONTROL The particle size achieved from a bead mill is a direct function of the media size used for the grinding process The average particle size that can be achieved quickly in a bead mill is about 1/1000 the size of the grinding media2011年1月17日 This paper presents a three dimensional Computational Fluid Dynamics (CFD) model to investigate the flow dynamics of solid–gas phases during fine grinding in an air jet mill Alpine 100AFG fluidized bed air jet mill is considered for the study and the jet milling model is simulated using FLUENT 632 using a standard kε model The model is developed in CFD simulation and experimental analysis of flow dynamics and grinding Also, equipment like ball mill is used at the final stages of grinding Among the comminution and grinding equipment, HPGR is increasingly utilized as tertiary crusher or primary mill because of Three Stage Flow Sheet with Two Stage HPGR and Ball Mill Fine Grinding 1 EFFECT OF GRINDING NOZZLES PRESSURE ON PARTICLE AND FLUID FLOW 2 PATTERNS IN A SPIRAL JET MILL 3 Lewis Scott, Antonia Borissova, Alan Burns and Mojtaba Ghadiri* 4 5 School of Chemical and Process Engineering, University of Leeds, 6 Leeds LS2 9JT, UK 7 8 *Corresponding author: 9 Abstract 10 Spiral jet mills utilise Effect of grinding nozzles pressure on particle and fluid flow
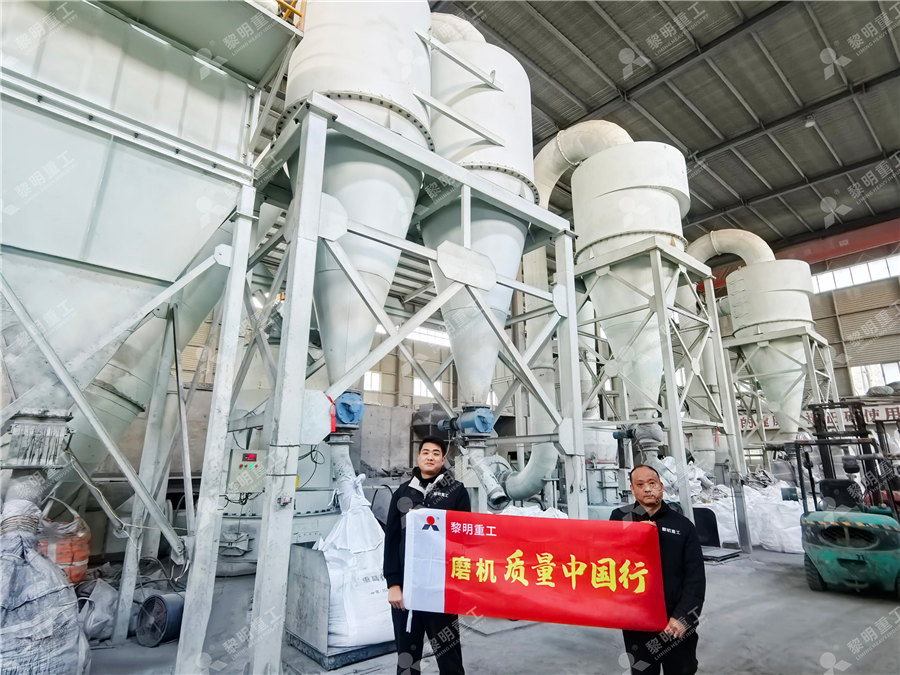
Flow diagram of the end discharge mill [18]
Raw mill grinding process is a complicated process in cement industry The effects of unwanted vibrations can be severe It causes a reduction in service life1 Opencircuit grinding consists of one or more grinding mills without size classification The final ground product discharges directly from the mill Tube mills offer the best design for singlestage opencircuit grinding 2 Two or Types and Characteristics of Common Grinding 2011年11月1日 Yang et al (2006) first studied the flow of grinding media in a simplified 14 l laboratory scale Isamill with multiple discs using DEM Jayasundara et al (2006Jayasundara et al Prediction of the disc wear in a model IsaMill and its effect on the Grinding in an air classifier mill — Part II: Characterisation of the twophase flow × Close Log In Log in with Facebook Log in with Google or Flow around the grinding pins 51 Experimental results The measured velocity in the case of the particle laden flow corresponds to the particle velocity in the mill(PDF) Grinding in an air classifier mill Academia
.jpg)
Impact of the powder flow behavior on continuous fine grinding
2018年11月1日 Other influences of grinding aids on the transport behavior as well as mill retention times are known for the operation of conventional tumbling ball mills (Dombrowe et al, 1982, Sottili and Padovani, 2000) and may be explained by similar powderflowrelated effects2011年7月25日 The flow investigations have been performed using a ZPS 100 air classifier mill (Hosokawa ALPINE GmbH) as shown in Fig 1The mill itself consists of a rotating disk with 4 grinding pins at its periphery and an impeller wheel classifier integrated into the top section of Grinding in an air classifier mill — Part I: Characterisation of the 2011年7月1日 Request PDF Grinding in an air classifier mill — Part II: Characterisation of the twophase flow Based on the insights about the air flow within the air classifier mill presented in the Grinding in an air classifier mill — Part II: Characterisation of CFD MODELLING OF A STIRRED BEAD MILL FOR FINE GRINDING Graeme L LANE CSIRO Minerals, Box 312, Clayton Sth, Victoria 3169 AUSTRALIA ABSTRACT flow in the horizontal stirred mill The various methods are described below In each case the geometry is specified using a multiblock bodyfitted finite volume mesh, and aCFD MODELLING OF A STIRRED BEAD MILL FOR FINE GRINDING
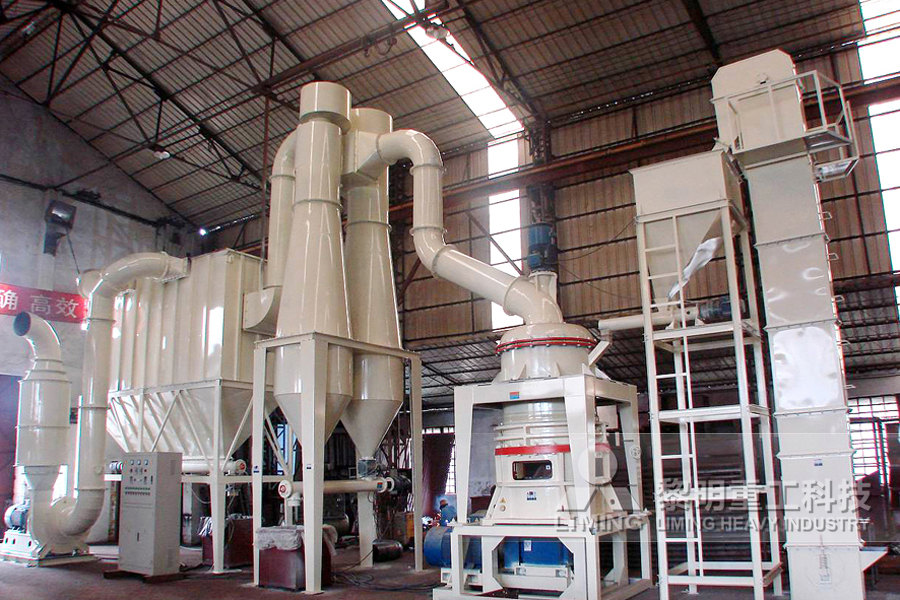
EFFICIENCY IN GRINDING AND ENERGY MANAGEMENT IN
2019年11月11日 Flow rate: The unit flow rate of the flour mill is usually expressed in units of contact length of the roller unit, ie kg/cm When the flow rate is too large, the homogeneity of material crushing will be reduced If the flow rate is too small, the feeding state is not normal and the equipment operation is unstable