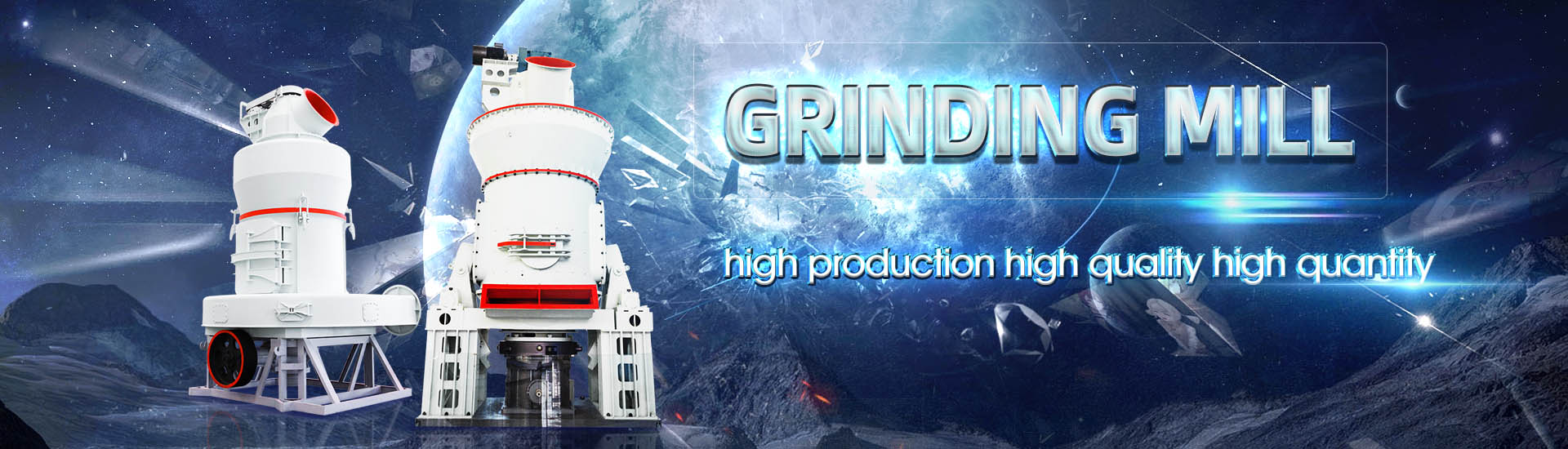
What is the rated breaking weight of the coal mill
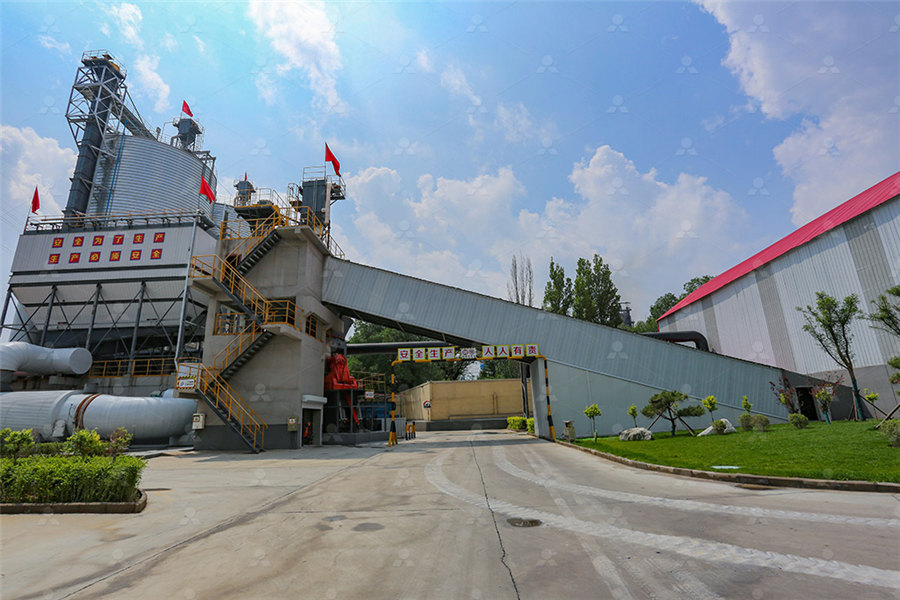
The Coal mill performance monitoring PPT SlideShare
2019年11月27日 • In pulverized coal combustion, the ratio of coal to carrying gas is usually in the range of y = 0506 kg/kg • Assuming a coal density rc = 15 x 103 kg/m 3, and the density of the carrying gas as rg = 09 kg/m 3, the 2014年4月1日 The objective of this study was to investigate the breakage characteristics of LRC by swing hammer mills for use in clean coal technology Generally, the appropriate range of Investigation of breakage characteristics of low rank coals in a The paper presents development and validation of coal mill model (including the action of classifier) to be used for improved coal mill control The model is developed by using the mass (PDF) Modeling and Control of Coal Mill AcademiaCoal is first broken down in a coal breaker into pieces of around 2 cm in diameter, though the size will vary depending on the specific plant machinery The broken coal is then fed into a mill Coal Mill an overview ScienceDirect Topics
.jpg)
Technical specifications of vertical roller coal mill
Technical specifications of vertical roller coal mill This study shows the performance of a currently running vertical roller coal mill (VRM) in an existing coalfired power plant In a2020年8月12日 CMC coal shows relatively better performance since it has lower moisture content and higher hard grove index Ultimately, the energetic efficiency of coal mill has been investigated andAn investigation of performance characteristics and 2012年11月17日 The document discusses coal mill/pulverizers used in thermal power plants It describes how pulverized coal is dried, ground, circulated, and classified within the mill to produce a fine powder that is then transported to Coal mill pulverizer in thermal power plants PPT2013年1月1日 Asmined coal must be crushed and sized to manageable particle sizes for either utilization, or for feed to a preparation plant This chapter reviews the methods for breaking Coal comminution and sizing ScienceDirect
.jpg)
Coal Mill in Thermal Power Plant PDF Mill (Grinding)
Coal Mill in Thermal Power Plant Free download as Word Doc (doc / docx), PDF File (pdf), Text File (txt) or read online for free This document discusses coal pulverizers/mills which are critical components that convert the stored 2021年11月4日 The operating costs of breaking coal particles into fine powder, to achieve optimum combustion for the boilers in a power plant, are made up of power input to carry on Technique to Investigate Pulverizing and Abrasive Performance of 2021年1月29日 Lower mill scale size (300 µm) particles, higher reduction temperature (1100 °C), higher reduction time (240 mins), and mill scale to coal ratio (1:3) yielded higher percentage of metallic iron Study the reduction of mill scale with lean grade coal through 2015年11月1日 As presented by Andersen et al (2009) and Odgaard, Stoustrup, and Mataji (2007), coal moisture imposes limit on the maximum load at which a coal mill can be operated and the load gradient (how fast the mill may change its operating point), if it is desired that the pulverized coal entering the furnace has moisture content less than or equal to a certain value A unified thermomechanical model for coal mill operation
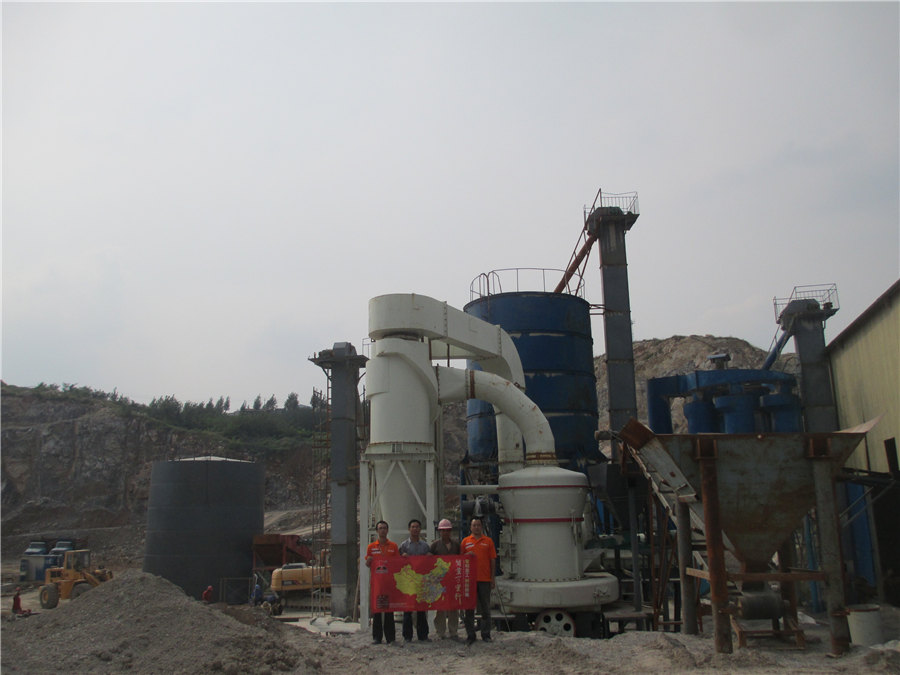
Effect of moisture in coal on station heat rate and fuel
2015年12月1日 TM is increased by 10 % the weight of coal will be only 90 % If the coal of GCV of 3500 Units tripping on mill choke up, load hunting due to insuf cient ow from bunkers, raw coal feeder 2021年11月9日 Introduction Replacing some of the coal by biomass is an effective way to reduce CO 2 emissions from pulverizedcoalfired power plants and integrated coal gasificationcombined cycle power plants However, compared with coal, biomass has lower grindability in the existing roller mills 1 and a lower calorific value per weight 2,3 The maximum biomass co Milling Characteristics of Coal and Torrefied Biomass Blends in a As one of the three major forces of coal mills, the grinding force exerts a significant impact on the working process of coal mills and parameters like mill current and outlet temperatureEffect of mill outlet temperature on the coal moisture content2016年9月1日 Furthermore, VRM separator speed (rpm) is one of the key operational parameters that determines product particle size Increasing the classi er rotor speed from 60 to 80 rpm decreases the particle Operational parameters affecting the vertical roller mill
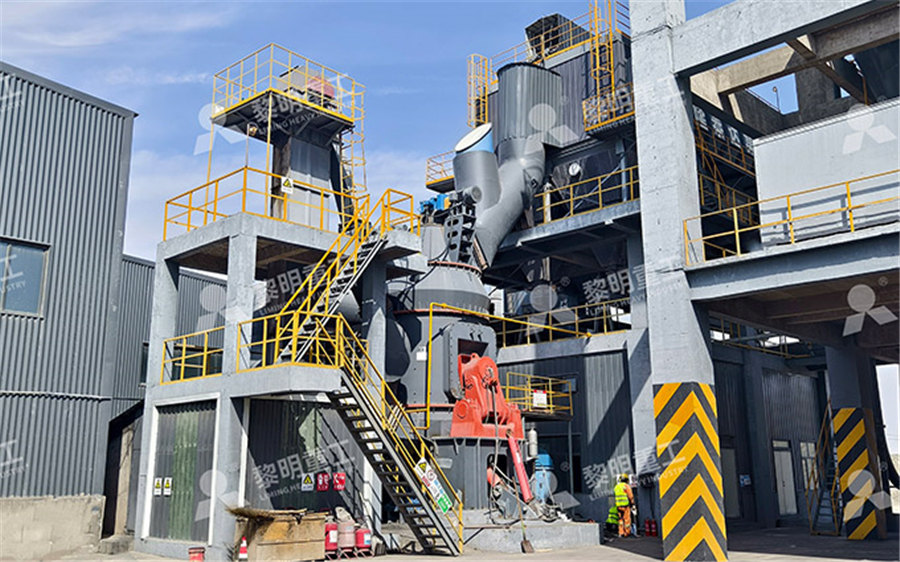
Vertical Grinding Mill (Coal Pulverizer) Explained saVRee
Introduction This article concerns itself with vertical grinding mills used for coal pulverization only (coal pulverizers), although vertical grinding mills can and are used for other purposes The 3D model in the saVRee database represents a vertical grinding bowl millOther grinding mill types include the ball tube mill, hammer mill, ball and race mill, and , roll and ring mill6 The K St value, which represents the pressure rise velocity, or ∆P/∆t, can vary between 40 and 200 barms1This unit may look a little confusing, as one would rather expect a unit like bar/s, which would be easier to understand The reason for using the unit barms1 is that there is a need to classify fuels independently from the volumes of the enclosures in which they are Explosion protection for coal grinding plants What should2020年8月12日 In a power plant, the coal mill is the critical equipment, whose effectiveness impacts the overall power plant efficiency Uniform coal feeding mass flow rate and required particle size and temperature at the outlet channel throughout with better classifier performance are crucial indicators that characterize the coal mill performanceAn investigation of performance characteristics and energetic 1985年3月1日 The higher the mill speed, the shorter the residence time in the mill and the larger the breaking forcesThus, for easiarrobreak materials, like coal, higher feed rates and lower mill speeds, which cause long residence times, produce finerproduct, while for hardertobreak materials, like wheat, the opposite is true The feed size was found not to affect the product Performance of the Szego mill in dry grinding coal and wheat
.jpg)
classifications and working of mills in a power plant
2020年6月29日 6 TYPES OF COAL PULVERIZER • Tube or ball mills: Lowspeed machines that grind the coal with steel balls in a rotating horizontal cylinder If the diameter of the cylinder is greater than the length of the et al 2017) In a coalfired power plant, one of the main equipment is the coal mill, whose effectiveness influences mainly the whole power plant performance (Shah, Vuthaluru, andAn investigation of performance characteristics and energetic weight2,3 The maximum biomass cofiring ratio for stable operation is limited by the design of the coal mill and the grindability of the feed biomass Researchers have recentlyMilling Characteristics of Coal and Torrefied Biomass Blends in a 2012年5月1日 Coal fired power plants are heavily used due to large and long lasting coal resources compared with oil or natural gas An important bottleneck in the operation of this particular kind of plants, however, is the coal pulverization process, which gives rise to slow takeup rates and frequent plant shutdowns (Rees Fan, 2003)In typical coal fired power plants, Derivation and validation of a coal mill model for control
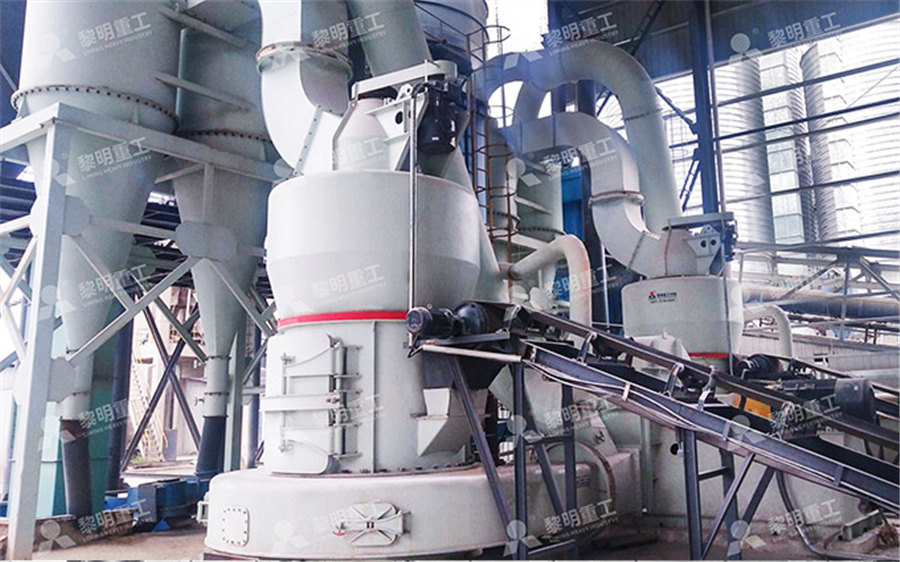
Effect of Biomass Carbonization on the Grinding of Coal/Biomass
2020年9月9日 In the HGI test, 50 g of airdried coal containing particle sizes ranging from 600 μm to 118 mm is pulverized using an HGI mill, and the weight (W) of the pulverized product passing through a 75 μm sieve is quantified (HGI index = 13 + 691W)2023年5月17日 coal hammer mill is a type of industrial equipment used to grind or pulverize coal into fine particles for combustion in furnaces or other industrial processes It is a machine that utilizes highspeed rotating hammers or blades to impact What Is Coal Hammer Mill? SBM Mill CrusherAir Swept Coal Mill Working Principle First, the raw coal is fed into the feed chute by the feeding device Then, the hot air with a temperature of about 300 ℃ enters through the air intake pipe and begins to dry the raw coal while they are fallingAir Swept Coal Mill Coal Mill In Cement Plant AGICO GROUP2020年1月1日 Direct reduction is the most accepted process in which reduction takes place below the melting point in solid state at the presence of suitable reducing agents to convert mill scale into valuable products like sponge iron or iron powder [3], [8], [9]It is mainly carried out in two ways: one is by means of a solid reductant where the reduction is carried out by coal and An experimental study and regression analysis to estimate the
.jpg)
Technique to Investigate Pulverizing and Abrasive Performance of Coals
2021年11月4日 Test methods for grindability and abrasion testing: Full scale ring and ball mill, Hardgrove mill [30,31], BCURAroll mill, Rotating electrode ball wear tester [32], Dropweight test machine [28 The exact volume of anthracite coal by weight varies The two main variables why this cannot be calculated precisely based on it's weight is the density of the coal and the size of the coal Coal from different sources will have different densities therefore the volume per ton can change from one source to anotherThe Volume of Anthracite Coal by Weight Coalpail2015年10月1日 This paper focuses on the flow control of pulverized fuel (pf flow) of the coal mill The control performance given by the conventional PID, The light weight particles are dra wn (PDF) Control for pulverized fuel coal mill2014年4月1日 The first stage of coal beneficiation is comminution, a process of breaking a large mass into fine particles Comminution is one of the most energy intensive unit operations in coal processing During crusher or mill operation, only a small fraction of the energy is used for actual breakage and the rest is absorbed into the machine and lostInvestigation of breakage characteristics of low rank coals in a

Modeling of Coal Mill System Used for Fault
2020年4月7日 The main task of a coal mill system is to prov ide qualified fuel for the pulverized coal boiler In i s the weight coefficient; N is data length The superscript ^ indic ates the (2012) is used to develop the coal mill model The following assumptions are made to develop the coal mill model: (1) Coal in the mill is either pulverised or unpulverised, ie different particle sizes are not considered Variations of the mass of coal particles (eg depending on th e moistureModeling and Control of Coal Millproblems in the plant, while the coal yard processed the coal through hammer mills as usual When these crushers were by passed the plants situation improved considerably The purpose for crushing the coal in the first place was to assist the pulverizers in their job Unfortunately, the mills never saw the coal because the feeder was pluggedWorld Coal “Sticky When Wet” Coal CombustionThe BTM is a lowspeed mill that primarily grinds coal by impact and attrition The VRM is a medium speed mill that grinds coal by compression and, because of the low coal inventory in the mill and flat grinding surfaces, develops shearing action as well For both mills a constant centrifugal force is maintained The speedA Comparison of Three Types of Coal Pulverizers Babcock Power

The structure of MPS mediumspeed coal mill system
Download scientific diagram The structure of MPS mediumspeed coal mill system from publication: Modeling of Coal Mill System Used for Fault Simulation 2013年1月1日 As it rotates it lifts the coal charge, which then falls and impacts the shell of the mill, as shown in Fig 91 The shell is constructed from screen plates that also function as a peripheral discharge Coal lumps break until they are small enough to fit through the openings in the breaker’s shellCoal comminution and sizing ScienceDirectAll coal pipes (and flows to all of the burners from each respective pulverizer) should be balanced and within +/ 2% of the mean flow Perform a seal air check Begin the normal pulverizer start sequence Once normal coal flow is applied to the mill, a full mill test should be conducted This should include isokinetic coal sampling and dirty The Storm Approach to Coal Pulverizer OptimizationCoal strength will also increase with increased confining pressure (Hobbs, 1964), as shown in Figure 32At atmospheric pressure or unconfined conditions, dull coals can be two to three times stronger than brighterbanded lithotypes from the same seam with the same rank (Medhurst and Brown, 1998, and Lawrence, 1978), and low rank coals can be up to 14 times stronger than Coal Strength an overview ScienceDirect Topics
.jpg)
Study the reduction of mill scale with lean grade coal through
2021年1月29日 Lower mill scale size (300 µm) particles, higher reduction temperature (1100 °C), higher reduction time (240 mins), and mill scale to coal ratio (1:3) yielded higher percentage of metallic iron 2015年11月1日 As presented by Andersen et al (2009) and Odgaard, Stoustrup, and Mataji (2007), coal moisture imposes limit on the maximum load at which a coal mill can be operated and the load gradient (how fast the mill may change its operating point), if it is desired that the pulverized coal entering the furnace has moisture content less than or equal to a certain value A unified thermomechanical model for coal mill operation2015年12月1日 TM is increased by 10 % the weight of coal will be only 90 % If the coal of GCV of 3500 Units tripping on mill choke up, load hunting due to insuf cient ow from bunkers, raw coal feeder Effect of moisture in coal on station heat rate and fuel 2021年11月9日 Introduction Replacing some of the coal by biomass is an effective way to reduce CO 2 emissions from pulverizedcoalfired power plants and integrated coal gasificationcombined cycle power plants However, compared with coal, biomass has lower grindability in the existing roller mills 1 and a lower calorific value per weight 2,3 The maximum biomass co Milling Characteristics of Coal and Torrefied Biomass Blends in a
.jpg)
Effect of mill outlet temperature on the coal moisture content
As one of the three major forces of coal mills, the grinding force exerts a significant impact on the working process of coal mills and parameters like mill current and outlet temperature2016年9月1日 Furthermore, VRM separator speed (rpm) is one of the key operational parameters that determines product particle size Increasing the classi er rotor speed from 60 to 80 rpm decreases the particle Operational parameters affecting the vertical roller mill Introduction This article concerns itself with vertical grinding mills used for coal pulverization only (coal pulverizers), although vertical grinding mills can and are used for other purposes The 3D model in the saVRee database represents a vertical grinding bowl millOther grinding mill types include the ball tube mill, hammer mill, ball and race mill, and , roll and ring millVertical Grinding Mill (Coal Pulverizer) Explained saVRee6 The K St value, which represents the pressure rise velocity, or ∆P/∆t, can vary between 40 and 200 barms1This unit may look a little confusing, as one would rather expect a unit like bar/s, which would be easier to understand The reason for using the unit barms1 is that there is a need to classify fuels independently from the volumes of the enclosures in which they are Explosion protection for coal grinding plants What should
.jpg)
An investigation of performance characteristics and energetic
2020年8月12日 In a power plant, the coal mill is the critical equipment, whose effectiveness impacts the overall power plant efficiency Uniform coal feeding mass flow rate and required particle size and temperature at the outlet channel throughout with better classifier performance are crucial indicators that characterize the coal mill performance1985年3月1日 The higher the mill speed, the shorter the residence time in the mill and the larger the breaking forcesThus, for easiarrobreak materials, like coal, higher feed rates and lower mill speeds, which cause long residence times, produce finerproduct, while for hardertobreak materials, like wheat, the opposite is true The feed size was found not to affect the product Performance of the Szego mill in dry grinding coal and wheat