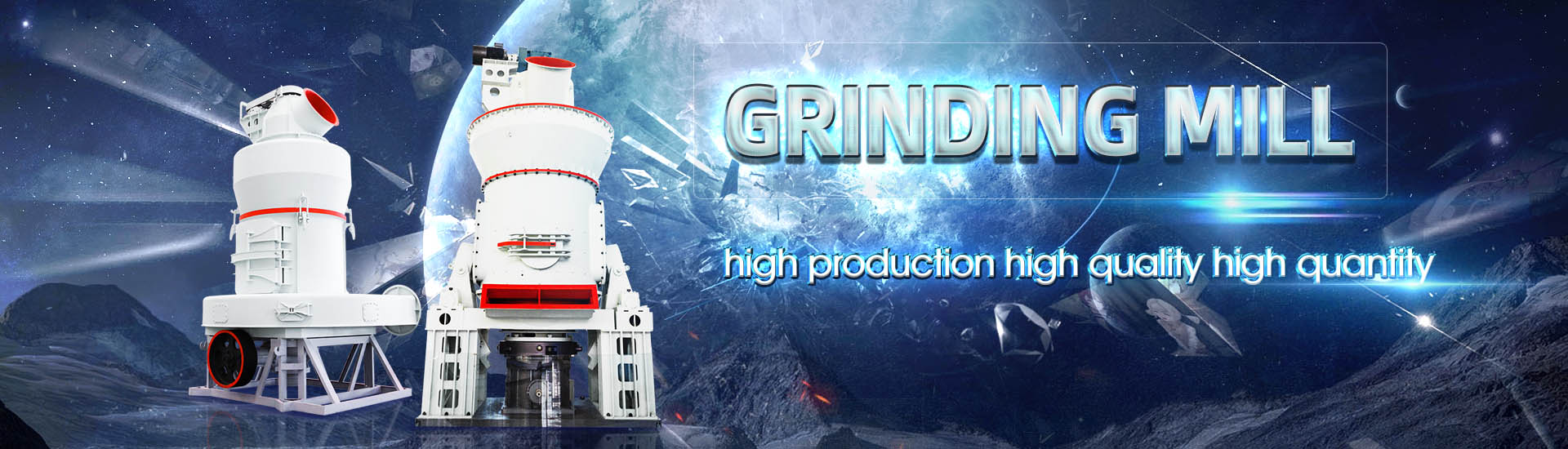
Antiwear roller of coal mill
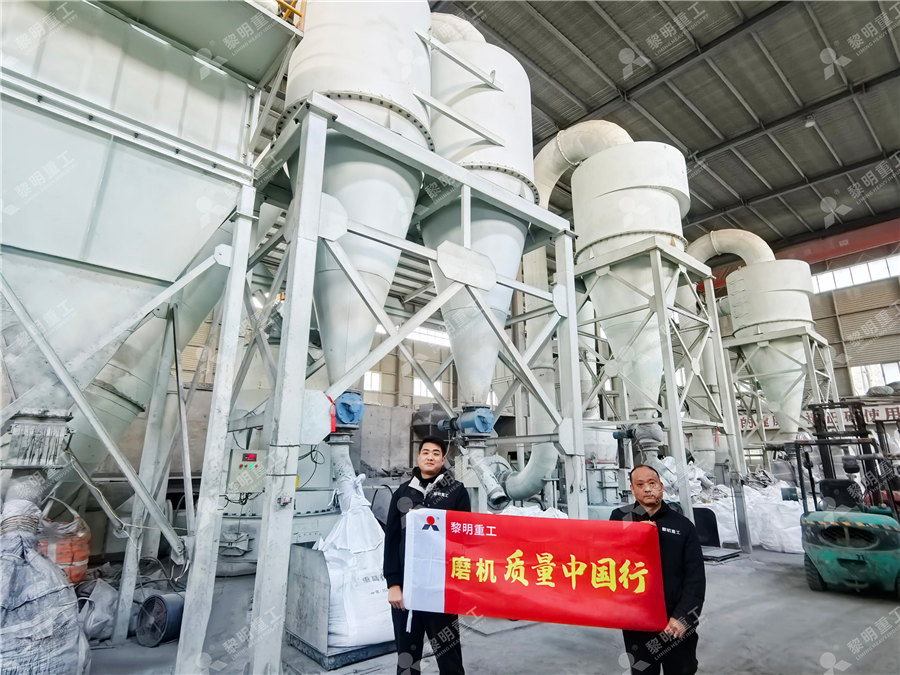
A Wear Condition Monitoring Model of Coal Mill Grinding Roller
2020年12月21日 In order to realize the monitoring of grinding roller wear state of coal mill in power plant as well as improve the reliability and safety of equipment, it is essential to build a To realize the wear condition of grinding roller of coal mill in power plant and improve the reliability of the equipment, it is essential to build a monitoring model with high accuracy for grinding A State Monitoring Method for Coal Mill Grinding Roller Base On The utility model relates to the technical field of coal mill protection, in particular to a roller frame antiwear structure for a coal mill, which aims to solve the problems thatCNU Roller frame wearresistant structure for coal mill Abstract: In order to solve the problem to directly measure the wear of roller of HP coal mill in thermal power plant, this paper proposes a new design scheme of wear monitoring and Design Scheme of Fault Diagnosis System for Rollers of Coal Mills
.jpg)
A Wear Condition Monitoring Model of Coal Mill Grinding Roller
2020年10月14日 Based on the extracted root mean square and kurtosis features, the tool wear monitoring is realized by MSPCA and PCA respectively The analysis and comparison results 2011年9月1日 Both a macroscopic and a microscopic analysis of the wear parts has been conducted A laboratory scale vertical roller mill with a transparent roller/table has been Wear mechanism of abrasion resistant wear parts in raw material Abstract: In order to monitor the wear condition of grinding roller of coal mill in power plant and improve the reliability of production equipment, it is necessary to establish a state monitoring Monitoring Model of Coal Mill in Power Plant Based on Big Data 2000年9月1日 Vertical roller mills are used in the cement industry for grinding cement raw material, coal, pozzolana and blastfurnace slag and for the finish grinding of cement This Wear protection in vertical roller mills ResearchGate
46.jpg)
Roller Mill Springer
Roller mill is a type of grinding equipment for crushing materials by pressure between two or more rolling surfaces or between rolling grinding bodies (balls, rollers) and a track (plane, ring, and refinement of the ATOX coal mill over the years, today’s leading airswept vertical roller mill is the compact ATOX Offering high reliability, low installation costs and a wide range of sizes, the ATOX COAL MILL FLSmidth CementFoster Wheeler provides replacement parts and maintenance services for vertical spindle roller mills used to pulverize coal Their parts and upgrades help reduce maintenance costs and improve mill performance They offer rotating airports, MBF Coal Pulverizers Foster Wheeler PDF Scribd2012年5月1日 Coal fired power plants are heavily used due to large and long lasting coal resources compared with oil or natural gas An important bottleneck in the operation of this particular kind of plants, however, is the coal pulverization process, which gives rise to slow takeup rates and frequent plant shutdowns (Rees Fan, 2003)In typical coal fired power plants, Derivation and validation of a coal mill model for control
.jpg)
A Wear Condition Monitoring Model of Coal Mill Grinding Roller
2020年10月14日 In order to realize the monitoring of grinding roller wear state of coal mill in power plant as well as improve the reliability and safety of equipment, it is essential to build a high accuracy model for monitoring wear state of grinding roller Previous studies have shown that the mill power can represent the wear degree of the grinding roller Assuming that the voltage of The document provides installation and operation instructions for the HRM1700M Vertical Roller Coal Mill It describes the mill's technical parameters, components, structure, working principles, and installation process Key aspects include grinding rollers that can be removed for maintenance, a hydraulic system that controls grinding pressure, and a separator that Operation Manual: HRM1700M Vertical Roller Coal MillDOI: 101145/ Corpus ID: ; A Wear Condition Monitoring Model of Coal Mill Grinding Roller Based on LSTM @article{Li2020AWC, title={A Wear Condition Monitoring Model of Coal Mill Grinding Roller Based on LSTM}, author={Yanping Li and Liang Tian and Yongping Li and Yaokui Gao}, journal={Proceedings of the 2020 International A Wear Condition Monitoring Model of Coal Mill Grinding Roller 2021年8月5日 Types Of Coal Pulveriser Slow speed mills like ball mill; Medium speed mills like bowl mill; High speed impact mill; The slow speed and medium speed mills are selected for coals ranging from subbituminous to anthracite The highspeed mills are used mainly for lignite Operation Of Bowl Mill PulveriserPulveriser in Thermal Power Plant Bowl Mill Ball Mill

Coal Mill in Cement Plant Vertical Roller Mill AirSwept Ball Mill
The most used coal mills in cement plants are airswept ball mills and vertical roller mills At present, most cement plants use coal as the main fuel in the clinker production process The standard coal consumed by the new dry process for producing 1 ton of cement clinker is usually between 100 kg and 130 kg, and the fuel cost accounts for about 15% of the cement Atox Vertical Roller Mill, Maintenance and Repair Free download as Powerpoint Presentation (ppt), PDF File (pdf), Text File (txt) or view presentation slides online The document discusses maintenance and repair of an ATOX Vertical Mill It describes systematic and conditionbased maintenance approaches Systematic maintenance consists of regular cleaning, lubrication Atox Vertical Roller Mill, Maintenance and RepairOur ATOX® Coal Mill has large rollers with great grinding capability of virtually all types of raw coal The rollers work harmoniously with a highlyefficient separator and feed sluice to consistently and reliably deliver coal meal to your desired fineness and moisture levelATOX® Coal Mill FLSmidth Cement2022年8月10日 After years of experience summarizing, KINGCERA has designed different antiwear solutions for the coal mill barrel and coal mill casing according to the operating characteristics of the coal mill Mediumspeed coal mill wearresistant ceramic plate Composite
.jpg)
Coal and Mill PDF Mill (Grinding) Mechanical
The document discusses pulverized coal mills used in power plants It describes different types of mills including tube mills, ball mills, and bowl mills Tube mills are low speed while bowl mills are medium speed The document explains the Thanks to low specific wear rates, different wear materials are used on our vertical roller mills The grinding elements are primarily made of alloy cast iron as per DIN 1695, MPS 200 BK coal mill, Krimzement Bakhchisarayski, Coal mill, gypsum mill, clay mill, etc Pfeiffer MPS millsATOX Coal Mill Free download as PDF File (pdf), Text File (txt) or read online for free The ATOX Coal Mill is a compact, versatile system suitable for grinding any type of coal with a long service life It uses proven roller mill technology to ATOX Coal Mill PDF Mill (Grinding) Bearing These extremely level replicable carbides are very easy to use and can be replaced in a very short period of time Zuper MMCC Rollers are the most cost effective VRM and Coal Mill grinding rollers in the whole world Our planted innovations in the metallurgy segmented make these rollers more resistant to wear as compared to traditional rollersGrinding Roller Tires Imcoalloys
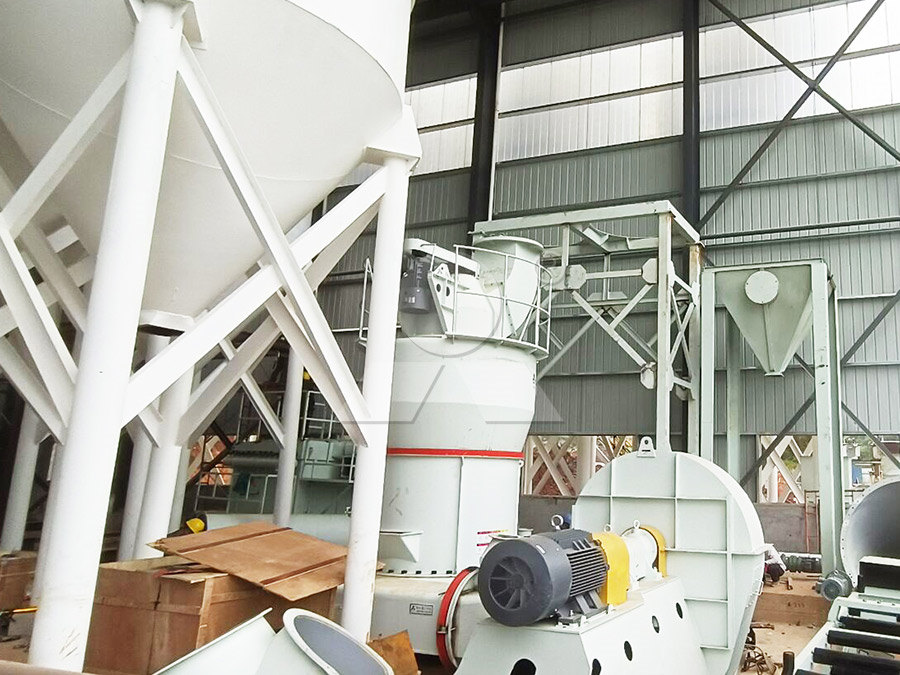
Wear protection in vertical roller mills ResearchGate
2000年9月1日 Vertical roller mills are used in the cement industry for grinding cement raw material, coal, pozzolana and blastfurnace slag and for the finish grinding of cementThis study shows the performance of a currently running vertical roller coal mill (VRM) in an existing coalfired power plant In a power plant, the coal mill is the critical equipment, whose Effect of mill outlet temperature on the coal moisture contentThe document contains measurements of wear on grinding parts from a coal mill taken on July 19, 2014 It records the diameters and dimensions of the roller tires and table liner, and calculates the wear rates based on production data Measurements were taken at various points along the roller tires and grinding plate, recording wear in millimeters The average wear rates for the roller Coal Mill Wear Measurement 29092014 PDF Nature ScribdCoal Mill PPT Free download as Powerpoint Presentation (ppt / pptx), PDF File (pdf), Text File (txt) or view presentation slides online The document provides an overview of coal mill operation, protections, and interlocks It discusses coal combustion theory, coal properties, coal mill components and operation, and troubleshooting The coal mill grinds coal into fine particles for Coal Mill PDF Combustion Chemistry
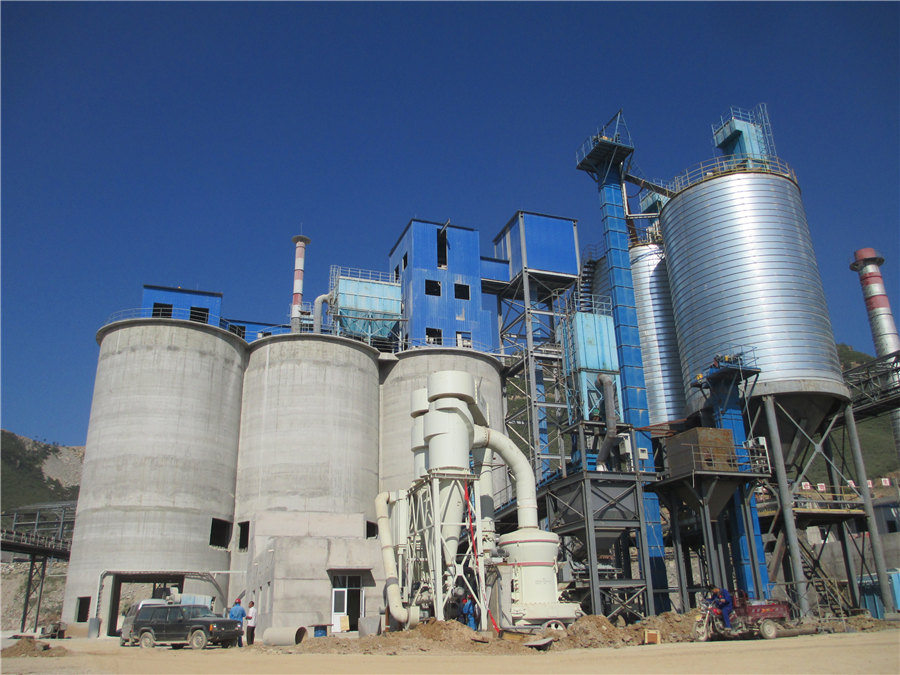
Wearresisting roller shell for coal mill Google Patents
The utility model discloses a wearresisting roller shell for coal pulverizer, including the roller shell main part, the roller shell main part comprises abrasionproof skin, wearresisting inlayer, grained layer, and the upper and lower both ends mouth of roller shell main part all is provided with wearresisting inner ring, and wearresisting inner ring can be for wearresisting welding 2001年10月1日 Associated minerals in the raw coal increase the energy consumption and abrasion of grinding media of vertical spindle pulverizer (VSP) Moreover, the low separating efficiency of classifier in VSP leads to the return of fines to grinding table, worsens the grinding phenomenon and make the energysize reduction of coal complexLoesche vertical roller mills for the comminution of ores and minerals 2009年1月1日 This book details advances in the production of steam and the utilization of all types of fuels Section 1 covers Steam Fundamentals including thermodynamics, fluid mechanics, heat transfer CFD Modeling of MPS Coal Mill for Improved The MPS mill is classified as an airswept, pressurized, vertical spindle, table/roller mill It contains an integral classifier, a grinding section, a windbox (plenum), and auxiliary components (Figure 1) Frequency converted electric drive Turret Louvre Return hopper Pendulum joints Housing Hot air inlet duct Grinding track carrier MotorCoal Pulverizer Design Upgrades to Meet the Demands of Low
.jpg)
A State Monitoring Method for Coal Mill Grinding Roller Base On
decomposition, which can well characterize the wear state of coal mill grinding roller, thus guiding power plant operation management personnel to realize predictive maintenance After decomposition at level 8, the original signal can be decomposed 2014年1月1日 Two mill systems are employed for most coal grinding applications in the cement industry These are, on the one hand, vertical roller mills (VRM) that have achieved a share of almost 90% and, on (PDF) MPS mills for coal grinding ResearchGate2022年11月1日 This study shows the performance of a currently running vertical roller coal mill (VRM) in an existing coalfired power plant In a power plant, the coal mill is the critical equipment, whose WEAR ANALYSIS OF VERTICAL COAL MILL PLATE ResearchGateIt includes two parts, high wear resistance boltless plates, and highly expandable riveting plates, which are selffastened and strengthened to withstand impact from mill balls With more than 20year application in coal mills of power plants, ball mills of cement plants and mining mills, boltless lining system proves to be much more stable and reliable than traditional bolted lining systemBoltless Mill LinersWuxi Orient Antiwear Co, Ltd
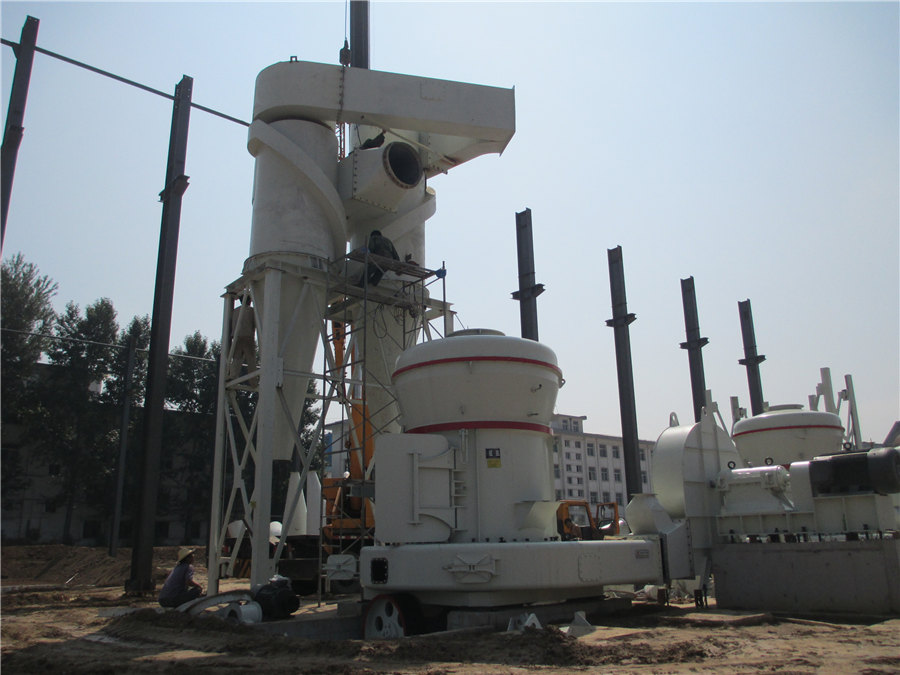
132 Loesche Mills For Solid Fuels Coal Mill E 2016
Loesche has been involved in processing solid fuels since 1925 Some key events include delivering their first coal mill in 1927 and introducing hydraulic systems in 1961 Their mills are distinguished by grinding without metal contact, suitability for combustible dust, and low vibration even at partial load Loesche designs complete grinding plants that operate efficiently and Erection of a LOESCHE Mill46 Free download as PDF File (pdf), Text File (txt) or view presentation slides online The document details the stepbystep erection process of a LOESCHE vertical roller mill Some of the key steps include pouring the mill foundation, erecting the pedestals and mill body, lifting and installing the grinding rollers and table, mounting the Erection of A LOESCHE Mill46 PDF Scribd2013年2月1日 Wear mechanisms in a coal pulveriser Compression, abrasion and impact are the three wear mechanisms that act upon the grinding elements and the pulveriser internals Compression is a wear component that results from the crushing of the material upon itself (attrition) between the grinding elements, ie between the tyres/rolls and the tableCoal pulverisation with vertical roller mills Engineer LiveCrack repair of Ball Mill Crusher with PTA wear facing Onsite repair of Roller Press Our applications Based upon hundreds of successful applications approved by our clients across the globe, Castolin Eutectic can provide optimized solutions with a wide range of products and technologies to combat wear in VRM (Vertical Roller Mill) and many moreKey Industry Program Castolin Eutectic
.jpg)
MBF Coal Pulverizers Foster Wheeler PDF Scribd
Foster Wheeler provides replacement parts and maintenance services for vertical spindle roller mills used to pulverize coal Their parts and upgrades help reduce maintenance costs and improve mill performance They offer rotating airports, 2012年5月1日 Coal fired power plants are heavily used due to large and long lasting coal resources compared with oil or natural gas An important bottleneck in the operation of this particular kind of plants, however, is the coal pulverization process, which gives rise to slow takeup rates and frequent plant shutdowns (Rees Fan, 2003)In typical coal fired power plants, Derivation and validation of a coal mill model for control2020年10月14日 In order to realize the monitoring of grinding roller wear state of coal mill in power plant as well as improve the reliability and safety of equipment, it is essential to build a high accuracy model for monitoring wear state of grinding roller Previous studies have shown that the mill power can represent the wear degree of the grinding roller Assuming that the voltage of A Wear Condition Monitoring Model of Coal Mill Grinding Roller The document provides installation and operation instructions for the HRM1700M Vertical Roller Coal Mill It describes the mill's technical parameters, components, structure, working principles, and installation process Key aspects include grinding rollers that can be removed for maintenance, a hydraulic system that controls grinding pressure, and a separator that Operation Manual: HRM1700M Vertical Roller Coal Mill
.jpg)
A Wear Condition Monitoring Model of Coal Mill Grinding Roller
DOI: 101145/ Corpus ID: ; A Wear Condition Monitoring Model of Coal Mill Grinding Roller Based on LSTM @article{Li2020AWC, title={A Wear Condition Monitoring Model of Coal Mill Grinding Roller Based on LSTM}, author={Yanping Li and Liang Tian and Yongping Li and Yaokui Gao}, journal={Proceedings of the 2020 International 2021年8月5日 Types Of Coal Pulveriser Slow speed mills like ball mill; Medium speed mills like bowl mill; High speed impact mill; The slow speed and medium speed mills are selected for coals ranging from subbituminous to anthracite The highspeed mills are used mainly for lignite Operation Of Bowl Mill PulveriserPulveriser in Thermal Power Plant Bowl Mill Ball MillThe most used coal mills in cement plants are airswept ball mills and vertical roller mills At present, most cement plants use coal as the main fuel in the clinker production process The standard coal consumed by the new dry process for producing 1 ton of cement clinker is usually between 100 kg and 130 kg, and the fuel cost accounts for about 15% of the cement Coal Mill in Cement Plant Vertical Roller Mill AirSwept Ball MillAtox Vertical Roller Mill, Maintenance and Repair Free download as Powerpoint Presentation (ppt), PDF File (pdf), Text File (txt) or view presentation slides online The document discusses maintenance and repair of an ATOX Vertical Mill It describes systematic and conditionbased maintenance approaches Systematic maintenance consists of regular cleaning, lubrication Atox Vertical Roller Mill, Maintenance and Repair
.jpg)
ATOX® Coal Mill FLSmidth Cement
Our ATOX® Coal Mill has large rollers with great grinding capability of virtually all types of raw coal The rollers work harmoniously with a highlyefficient separator and feed sluice to consistently and reliably deliver coal meal to your desired fineness and moisture level2022年8月10日 After years of experience summarizing, KINGCERA has designed different antiwear solutions for the coal mill barrel and coal mill casing according to the operating characteristics of the coal mill Mediumspeed coal mill wearresistant ceramic plate Composite