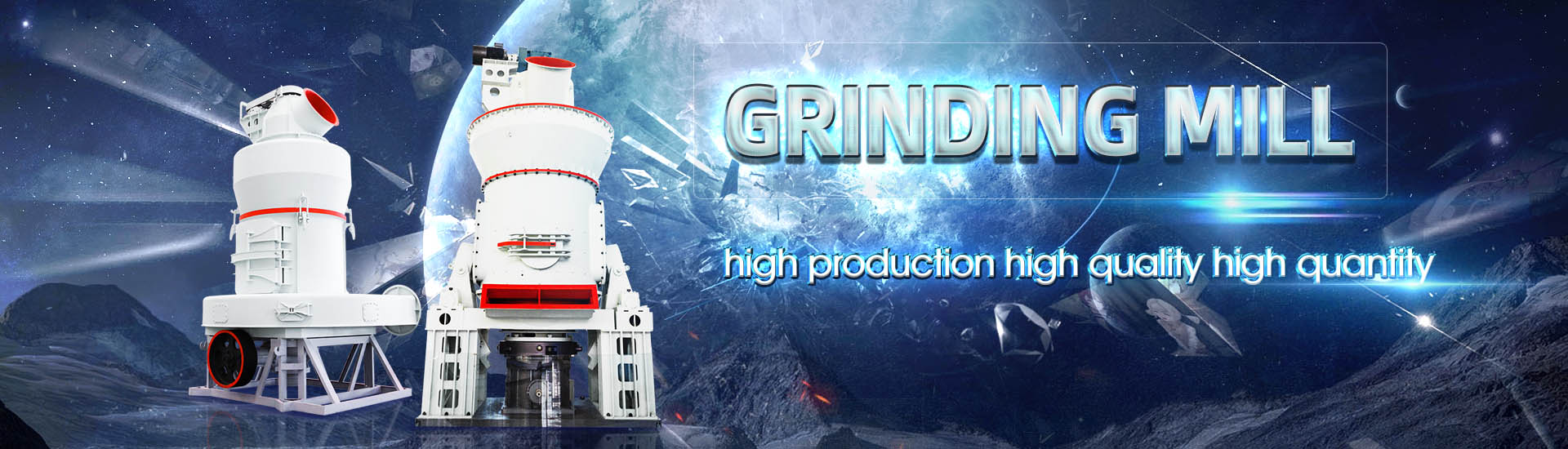
Vertical grinding layer calculation method
.jpg)
A simulation method for surface height distribution of endface
This paper proposes an analysis method for determining endface grinding workpieces' surface 2023年6月1日 In this paper, a numerical calculation method for internal particle–fluid coupling Operation parameters multiobjective optimization method of 2024年5月1日 Vertical surface grinding (VSG) is an effective method that can adapt to multiple machining tasks, including stock removal machining to get high productivity and finish machining to obtain highquality surfaces Force prediction can reveal some mechanisms in the VSG process, conducing to the improved machining quality and efficiencyForce modeling of vertical surface grinding considering wheel 2023年6月1日 This study aims to improve the output and production efficiency of a large vertical mill by optimizing its operational parameters This paper takes a large vertical mill in LGM as the object, a numerical calculation method of particle–fluid coupling system in large vertical mill based on CFDDPM theory, and a multiobjective optimization method of operating parameters of Operation parameters multiobjective optimization method of
.jpg)
Investigating grinding media dynamics inside a vertical stirred
Investigating grinding media dynamics inside a vertical stirred mill using the discrete element method The normal and tangential dumping forces were used in this work for the calculation of both the energy and the power dissipation Normalised angular velocity at the top layer of grinding media for 50 rpm highlighting the region Endface grinding has the characteristics of high processing efficiency [1], high shape accuracy [[2], [3], [4]], good parallelism [5], and slight damage to the machined surface [[6], [7], [8]], and is often used to thin workpieces [9, 10], or process large flat surfaces [11], or even manufacture ultrathin wafers [12]Considering the high quality of the processed surface [13], endface A simulation method for surface height distribution of endface 2022年1月23日 In this work, the discrete element method (DEM) was used to examine the effects of stirrer helix angle (α), stirrer diameter (d), and rotating speed (n) on the grinding performance in an Analysis and Optimization of Grinding Performance of Vertical Agarwal et alresearches show that crack formation ceramics grinding process in the optical hardbrittle materials microstructure the subsurface damage (SSD) in tiny cracks ceramic grinding [10]To overcome this challenge, a method for marking small surface damage with a single particle was described at material removal depth of grinding and 3–4 μm/h, which was the Investigation into the role of Si and SiC phases in RBSiC ceramics
.jpg)
An assessment method of rail corrugation based on wheel–rail vertical
2023年4月25日 In practice, the assessment and treatment of rail corrugation are quantitatively based on the corrugation depth Wheel–rail vertical forces (WRVF), as a direct reflection of wheel–rail interaction, can give expression to the corrugation depth and thus serve as a key parameter for assessing the corrugation In this paper, we propose an evaluation method for 2009年1月31日 Download Citation Grinding process within vertical roller mills: Experiment and simulation Based on screening analysis, laser size analysis, grindability and rigidity tests of samples Grinding process within vertical roller mills ResearchGate2023年4月25日 An assessment method of rail corrugation based on wheel–rail vertical force and its application for rail grinding April 2023 Journal of Civil Structural Health Monitoring 13(45)An assessment method of rail corrugation based on wheel–rail vertical 2019年8月7日 Aiming at the difficulties in accurate prediction of the dressing amount of monolayer electroplated grinding wheel, a new calculation method based on image processing was proposed(PDF) A Calculation Method for Dressing Amount of Monolayer
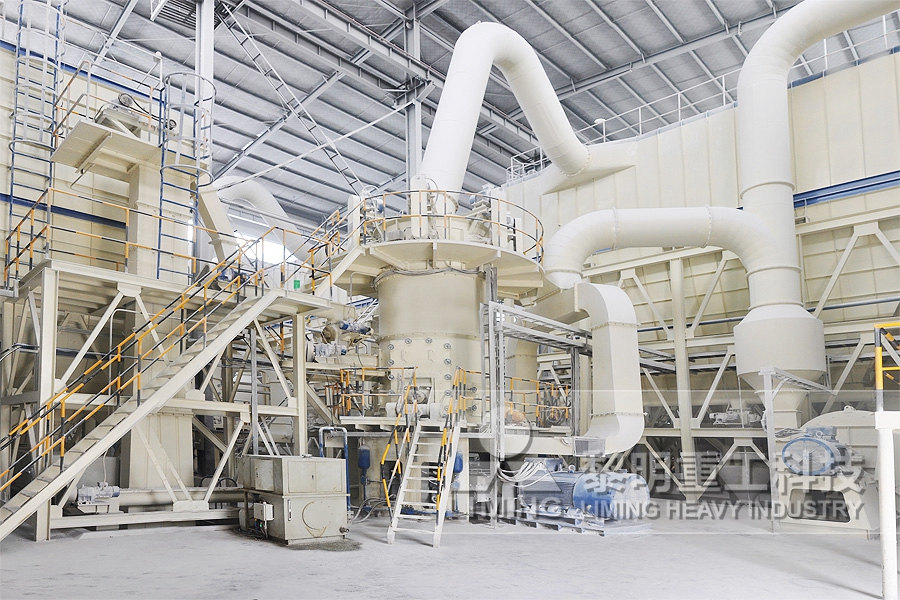
Calculation method and evaluation of surrounding rock pressure
deepwater bearing rock layer of the vertical sha Chehadeh, Turan, and Abed 14 reported that the maximum compressive stresses of the sha lining increased by a large margin, and signicant tensile 2020年3月15日 Investigating grinding media dynamics inside a vertical stirred mill using the discrete element method: Effect of impeller arm length Author links open overlay panel D Daraio a c, Normalised angular velocity at the top layer of grinding media for 50 rpm highlighting the region of maximum Investigating grinding media dynamics inside a vertical stirred methods, or others not yet tested, provides the strongest signals for intensity change It is not difficult to envision how changes in the SHIPS shear calculation method, with respect to the vertical levels and layers and/or the horizontal averaging domain, could lead to significantly different results from that model,On the Calculation of Vertical Shear: An Operational PerspectiveJune 2022; ARCHIVE Proceedings of the Institution of Mechanical Engineers Part C Journal of Mechanical Engineering Science 19891996 (vols 203210) 236(2):1107(PDF) A comprehensive review on the grinding process:
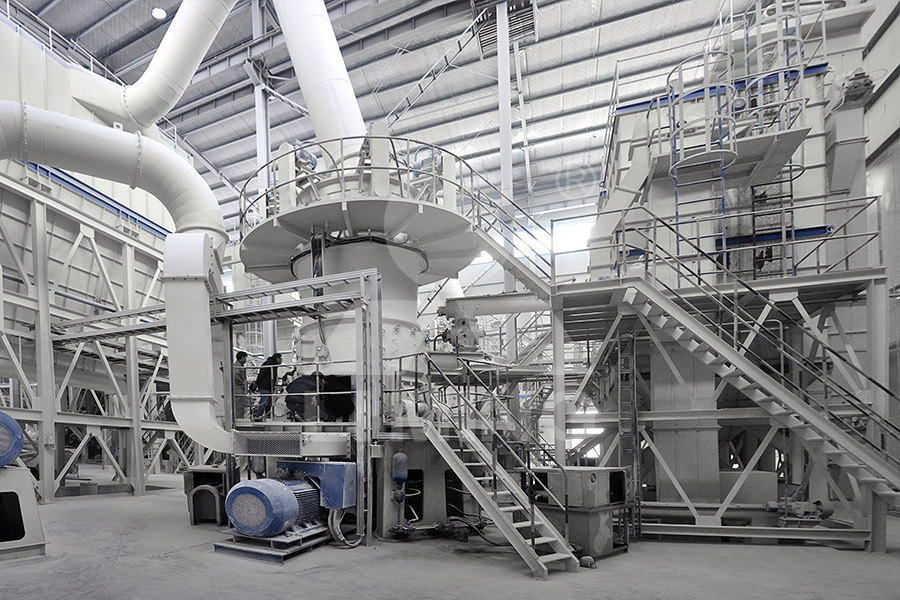
GRINDING METHOD, TRAJECTORY PLANNING AND SIMULATION
32 Robotassisted grinding method The main workflow of robotassisted grinding method is as follows: (1) Perform a layerbylayer CT scan of the knee joint and use mathematical methods and computer imaging to gather the 3D information of the knee joint2012年2月1日 Hydraulic system pressure, contact surface between grinding roller and materials and grinding roller force of roller mill are analyzed A new roller pressure calculation method named average Average surface roller pressure calculation method of roller mill2024年5月1日 In view of the parameter estimations for the hybrid method and other B ij functions to be presented in 43 The hybrid method and its comparison with the backcalculation method, 44 Comparison of different empirical B, we found that the exponents generally got closer to the microhydrodynamic predictions as the fitting SSR and SER were reduced, thus making PBM of an industrialscale vertical wet stirred media mill (HIGMill The slag grinding process is introduced The basic control forms of vertical mill are presented by analyzing the dynamic characteristics of material layer in slag vertical millMaterial layer control based on slag vertical mill's ResearchGate
.jpg)
Solid Edge’s Application in Vertical Mill Design Springer
link of the main components of vertical mill, carried out the antijamming analysis, and solved the problems in the assembly, overall design of vertical mill was completed well and achieved the expect of design Fig 6 Vertical roll grinding explosion Fig 7 Vertical grinding structure Solid Edge’s Application in Vertical Mill Design 年9月11日 Grinding and separation efficiency of vertical roller mill were evaluated In addition to these, performance figures of vertical roller mill and conventional closed ball mill circuit were comparedPerformance Evaluation of Vertical Roller Mill in Cement Grinding2022年8月1日 The paper investigates the effects of changing the particle–particle restitution and sliding friction coefficients of grinding media within a vertical stirred mill using the discrete element (PDF) A discrete element method investigation within 2024年5月1日 Vertical surface grinding (VSG) is an effective method that can adapt to multiple machining tasks, including stock removal machining to get high productivity and finish machining to obtain highquality surfaces Force prediction can reveal some mechanisms in the VSG process, conducing to the improved machining quality and efficiencyForce modeling of vertical surface grinding considering wheel
.jpg)
A New Fuzzy Comprehensive Evaluation Method for Priority
2016年5月1日 Considered to be the only grinding machine arranged for 3axis numerical control, the machine is designed for finishing operations on shafts in jet engine compressors2018年5月1日 The improved formula calculation of monitoring sections 1 and 6 in the sand layer equals approximately the measurement (the ratio of calculation to the measurements is 089 and 096, respectively), indicating that the vertical earth pressure agrees with the Gaussian distribution in the sand layer, due to the shear strength of the overburden soilAn improved method to calculate the vertical earth pressure 2023年10月15日 During hot rolling of rails, the carbon near the rail surface is oxidized and a layer of low carbon structure, called rail decarburized layer, as shown Fig 1, is formedThe rail decarburized layer changes the mechanical properties of the rail surface and affects the wheelrail contact and wear, thereby influencing the development rate of rail corrugationEffects of decarburized Layer's material property on the rail 2013年1月1日 PDF Principles of Modern Grinding Technology explains the principles that led to rapid improvements in modern grinding technology over recent decades Find, read and cite all the research Principles of Modern Grinding Technology ResearchGate
.jpg)
A general simple method for calculating consolidation settlements of
2022年8月1日 This method is then used to calculate consolidation settlements of clayey soils in three typical cases: Case 1 is a single soil layer without vertical drains under loading only; Case 2 is a two 2022年11月1日 This section introduces the modeling method, calculation principle of DEM and the experimental method verifying the simulation effectiveness In addition, the material treatment method and the experimental process of rice milling are also stated in this section 21 Simulation method and modeling211 DEM modelNumerical analysis of the rice transport uniformity in vertical Download scientific diagram Flowchart of grinding force calculation process from publication: Predictive modeling of grinding force in the inner thread grinding considering the effect of grains Flowchart of grinding force calculation process2023年3月1日 β [1 − α; p 2; n − p − 1 2] = (1–α) th quantile of β [p 2; n − p − 1 2] distribution For α = 005, the number of outliers is 44 among 280 data corresponding to an upper limit control U C L M a h a l a n o b i s = 455 as illustrated in Fig 3The results of these outliers have been carefully analyzed by a process expert from the cement plant Indeed, if an outlier carrying Efficient machine learning model to predict fineness, in a vertical
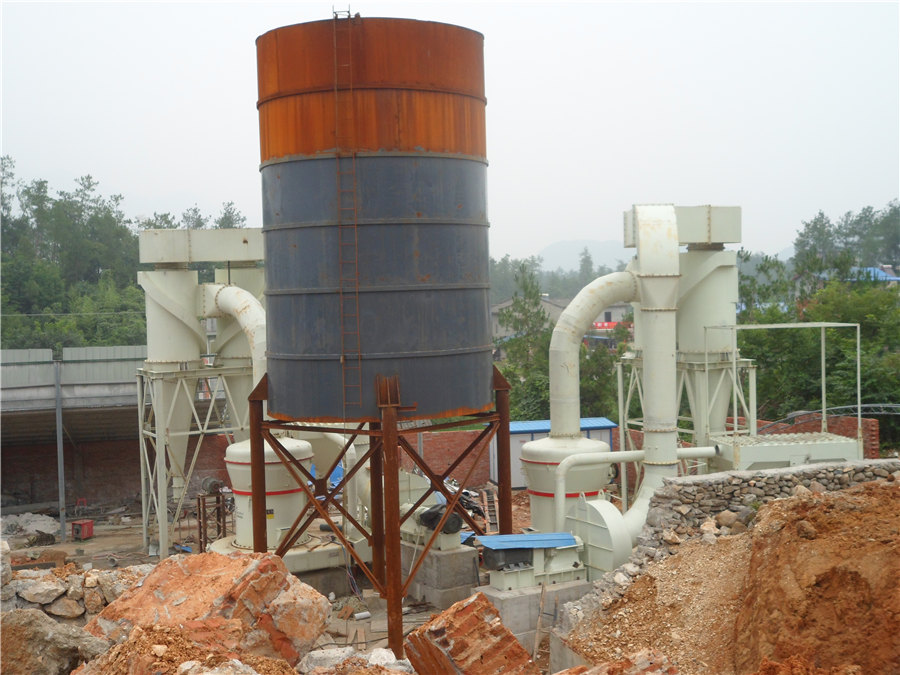
Force modeling of vertical surface grinding considering wheel
2024年5月1日 Vertical surface grinding (VSG) is an effective method that can adapt to multiple machining tasks, including stock removal machining to get high productivity and finish machining to obtain highquality surfaces Force prediction can reveal some mechanisms in the VSG process, conducing to the improved machining quality and efficiency2023年6月1日 This study aims to improve the output and production efficiency of a large vertical mill by optimizing its operational parameters This paper takes a large vertical mill in LGM as the object, a numerical calculation method of particle–fluid coupling system in large vertical mill based on CFDDPM theory, and a multiobjective optimization method of operating parameters of Operation parameters multiobjective optimization method of Investigating grinding media dynamics inside a vertical stirred mill using the discrete element method The normal and tangential dumping forces were used in this work for the calculation of both the energy and the power dissipation Normalised angular velocity at the top layer of grinding media for 50 rpm highlighting the region Investigating grinding media dynamics inside a vertical stirred Endface grinding has the characteristics of high processing efficiency [1], high shape accuracy [[2], [3], [4]], good parallelism [5], and slight damage to the machined surface [[6], [7], [8]], and is often used to thin workpieces [9, 10], or process large flat surfaces [11], or even manufacture ultrathin wafers [12]Considering the high quality of the processed surface [13], endface A simulation method for surface height distribution of endface
.jpg)
Analysis and Optimization of Grinding Performance of Vertical
2022年1月23日 In this work, the discrete element method (DEM) was used to examine the effects of stirrer helix angle (α), stirrer diameter (d), and rotating speed (n) on the grinding performance in an Agarwal et alresearches show that crack formation ceramics grinding process in the optical hardbrittle materials microstructure the subsurface damage (SSD) in tiny cracks ceramic grinding [10]To overcome this challenge, a method for marking small surface damage with a single particle was described at material removal depth of grinding and 3–4 μm/h, which was the Investigation into the role of Si and SiC phases in RBSiC ceramics 2023年4月25日 In practice, the assessment and treatment of rail corrugation are quantitatively based on the corrugation depth Wheel–rail vertical forces (WRVF), as a direct reflection of wheel–rail interaction, can give expression to the corrugation depth and thus serve as a key parameter for assessing the corrugation In this paper, we propose an evaluation method for An assessment method of rail corrugation based on wheel–rail vertical 2009年1月31日 Download Citation Grinding process within vertical roller mills: Experiment and simulation Based on screening analysis, laser size analysis, grindability and rigidity tests of samples Grinding process within vertical roller mills ResearchGate
.jpg)
An assessment method of rail corrugation based on wheel–rail vertical
2023年4月25日 An assessment method of rail corrugation based on wheel–rail vertical force and its application for rail grinding April 2023 Journal of Civil Structural Health Monitoring 13(45)2019年8月7日 Aiming at the difficulties in accurate prediction of the dressing amount of monolayer electroplated grinding wheel, a new calculation method based on image processing was proposed(PDF) A Calculation Method for Dressing Amount of Monolayer