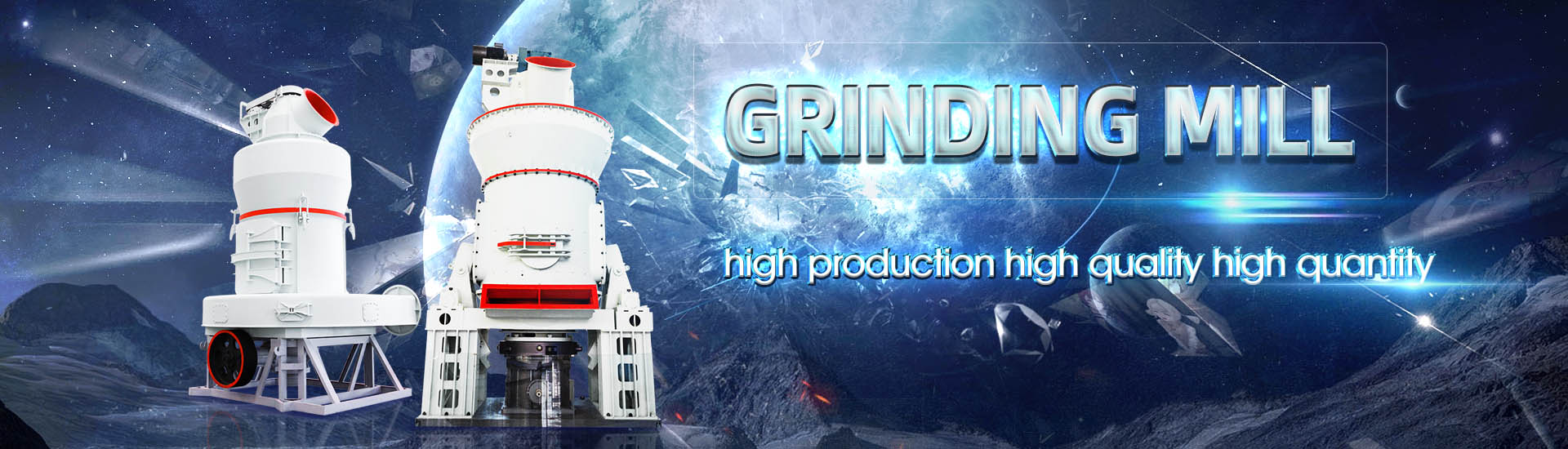
Ore mill speed
.jpg)
Mill Speed an overview ScienceDirect Topics
2011年8月1日 Milling speed is one of the most important milling parameters that controls the milling process because it provides the mill with the energy required for (1) powder particles 2023年4月23日 flow inside the mill, showed that the collision energy of grinding media increased with mill speed from 22 to 45 rpm giving more undersized pr oduct of 152mm, 112mm and 86mm and sudde nly(PDF) Grinding Media in Ball MillsA Review2021年1月22日 They found that the stirred mill was more beneficial for grinding P80 10–30 μm minerals to liberate more valuable minerals and the grade of iron concentrate was 52% higher Impact of ball filling rate and stirrer tip speed on milling iron ore 2012年6月1日 The speed of rotation of the mill dete rmines three basic types of operation modes: slow rotation (cascading), fast rotation (cataracting) and very fast rotation (centrifugation)Grinding in Ball Mills: Modeling and Process Control ResearchGate
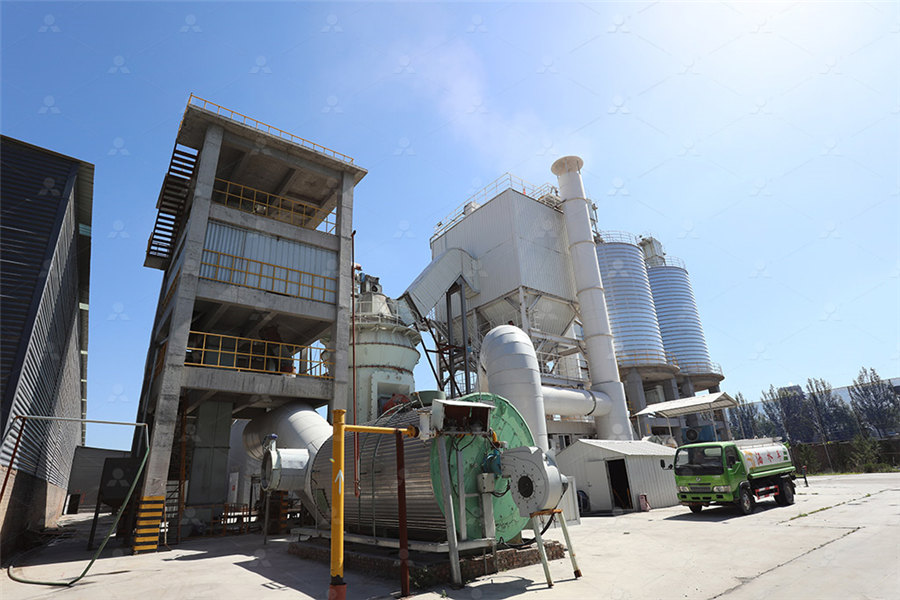
Optimal Speed Control for a SemiAutogenous Mill
2019年12月9日 The rotation speed of a mill is an important factor related to its operation and grinding efficiency Analysis and regulation of the optimal speed under different working conditions can effectively reduce energy loss, improve 2020年7月2日 When the mills charge comprising 60% of small balls and 40% of big balls, mill speed has the greatest influence on power consumption When the mill charge is more (PDF) Effects of Ball Size Distribution and Mill Speed and Their 2024年7月31日 This study addresses the gap in the literature concerning the collective impact of key parameters, including ball size, feed rate, and mill speed, on grinding efficiency Nine spherical balls, ranging from 15–65 mm, were Effect of Grinding Conditions on Clinker Grinding Milling time and speed are two important factors that affect ore grinding performance in ball mills The longer the milling time, the more fines will be processed, which will lead to a lower grind Factors affecting ores grinding performance in ball mills
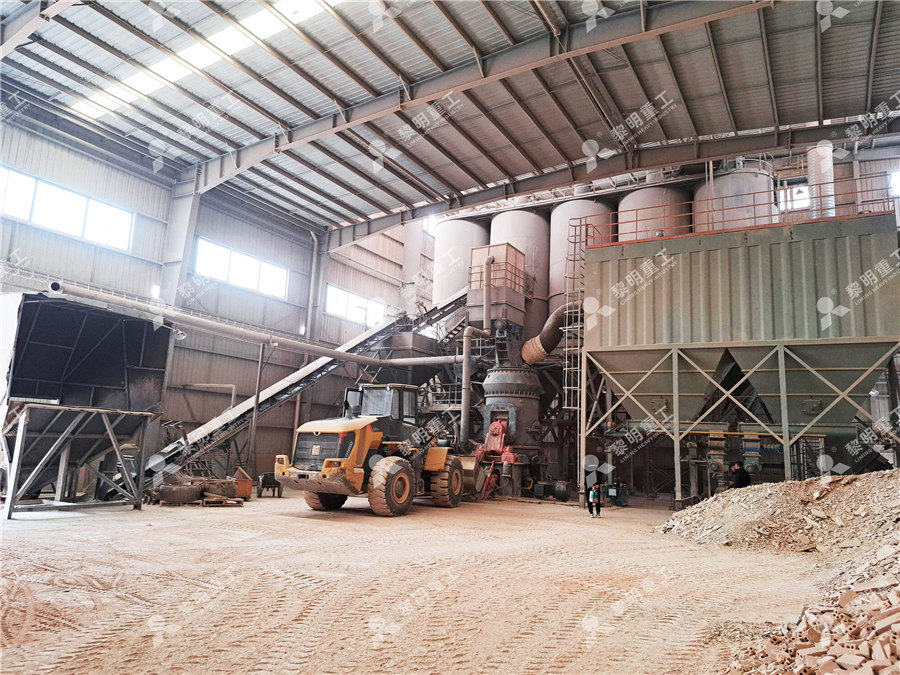
Effect of lifters and mill speed on particle behaviour, torque, and
In this paper, simulation results of particle behaviour, mill torque, and power consumption obtained from DEM simulation are compared with experimental results in detail to validate the However, the grinding media diameter d is normally negligible compared to the mill diameter D and is not accounted for in the calculations below To use: Enter the effective mill diameter (m) to calculate the actual critical speed (in RPM) Enter a given mill speed (in RPM) to convert to percent critical speed Click on "Calculate"Metallurgical Apps Mill Critical Speed2018年9月22日 For variable speed mills, the operating range for mill speed has to be defined so that mill power/torque requirement can be matched by the motor power/torque capability This paper will describe how this relationship can be influenced by ore grindabilityVariable Speed SAG Mill 911Metallurgistpinion is set on an output shaft of the gearbox The nominal mill efficiency, at optimum speed, is 80 Mg/h The dimensions and the high mass of the rotating elements cause the drive system to be overloaded when the mill filled with copper ore is started For this reason, the mill is stopped only in the case of a failure or planned maintenance Energy Efficiency Analysis of Copper Ore Ball Mill Drive Systems
.jpg)
Factors affecting ores grinding performance in ball mills
Ore grinding is one of the key stages in the mining process It's where the ore is reduced to a fine powder, which can then be used in other stages of the extraction process Grinding performance is a critical parameter for this stage, as it affects both the speed and quality of the final product The parts of a ball mill2022年12月15日 In the present study, size reduction experiments were performed on HighPressure Grinding Rolls (HPGR), ball mill and stirred mill of PGE bearing chromite oreSize reduction performance evaluation of HPGR/ball mill and 2024年7月31日 The production of cement, an essential material in civil engineering, requires a substantial energy input, with a significant portion of this energy consumed during the grinding stage This study addresses the gap in the literature concerning the collective impact of key parameters, including ball size, feed rate, and mill speed, on grinding efficiency Nine spherical Effect of Grinding Conditions on Clinker Grinding Efficiency MDPI2021年1月22日 Impact of ball filling rate and stirrer tip speed on milling iron ore by wet stirred mill: Analysis and prediction of the particle size distribution Author links open overlay panel Wang Guo a b, Yuexin Han a b, Batch grinding studies by a ball mill for hematite ore Materials Today: Proceedings, Volume 26, Part 2, 2020, pp 825832Impact of ball filling rate and stirrer tip speed on milling iron ore
.jpg)
SAG Mill Design and Benchmarking Using Trends in the JKTech
Figure 3(a)—Pilot SAG mill Ecs vs Ball Load, Reproduced from Morrell (2006a); (b) SAG Mill Ecs vs Ball Load for ‘OpenCircuit’ SAG Mills in JKTech Database 0 2 4 6 8 10 12 14 16 18 20 0 2 4 6 8 10 12 14 SAG mill Ecs (kWh/t) Ball load (%) 0 5 10 15 20 SAG mill Ecs (kWh/t) Ball load (%) Coarse feed, uncrushed pebbles Very soft ores, Axb >年5月1日 Crushing and grinding consume most of the energy in mineral processing Ball mill is an important kind of grinding equipment used to decrease the size of ore particles The power consumption of a ball mill is one of the most important parameters to consider in the design of a ball mill because it determines its economic efficiencyEffect of lifters and mill speed on particle behaviour, torque, and density, ball mill speed and grinding media consumption rate, water spray rate on the highfrequency screen, and feed pulp density to the screen The performance of the ball mill varied with the ore properties The effect of process parameters on ultrafines generation and power consumption in the ball mill is explained furtherv117n1a11 Performance optimization of an industrial ball mill for 2015年10月8日 Mill Critical Speed; Example Mill Metallurgy Summary/Report; Rod Mill Power Draw; Wet Grinding Overflow Ball Mill Power Draw; Rod Mill Design – Wet open circuit grinding 31; Ball Mill Design Calculations (Rod Mill Mineral Processing Equations EQ 911Metallurgist
.jpg)
Energy Efficiency Analysis of Copper Ore Ball Mill Drive Systems
Energies 2021, 14, 1786 4 of 14 (a) (b) Figure 2 Ball mill drive system with low‐speed SAS motor without intermediate gearbox: (a) prior to modernization, (b) after modernization on the right [34]2019年8月14日 • Central discharge ball mill: the inlet of medium unloading ball mill is at both ends, and the outlet is in the middle of the ball mill 4 According to the ore discharge of ball mill: • Overflow ball mill: Discharge the ore through hollow shaft • Grid ball mill: Discharge the ore through the plaid plateThe Ultimate Guide to Ball Mills Miningpedia2018年4月17日 Mill Power required at pinionshaft = (240 x 165 x 1025) ÷ 0746 = 5440 Hp; Speed reducer efficiency: 98%; 5440 Hp ÷ 098 = 5550 HP (required minimum motor output power) Therefore select a mill to draw at least 5440 Hp at the pinionshaft Based upon the pilot plant test results, the volumetric loading for the mill can be determinedAutogenous and SAG SemiAutogenous Mill Design Calculations2018年7月18日 A variable speed primary mill provides a method of compensating for variations in ore hardness and gives a much more flexible grinding circuit Although there is no such circuit on hand today, we think it is within our grasp the technology is there to make big mills, to use sophisticated control schemes and to vary the speed of huge hp millsSAG Mill Variable Speed Drive 911Metallurgist
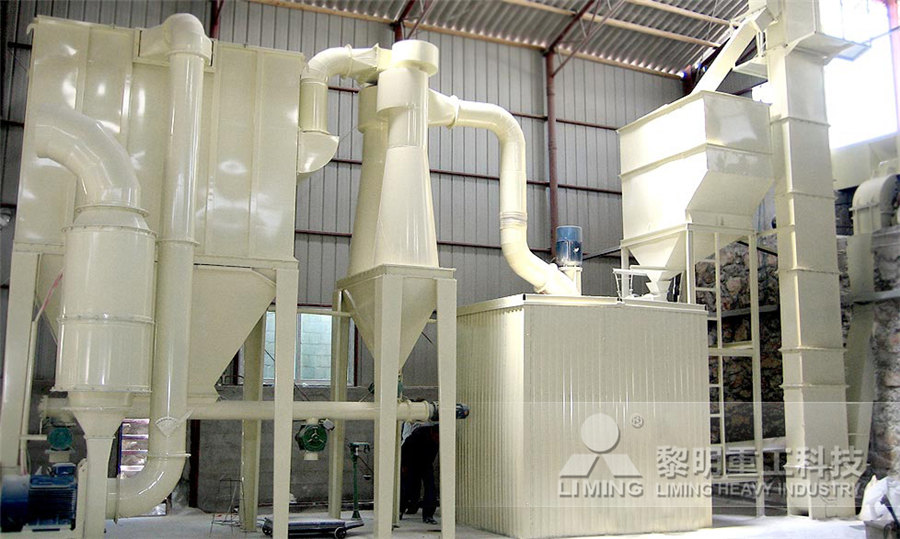
(PDF) Control of ball mill operation depending on ball load and ore
2023年12月12日 of the ball mill Ore can have various properties, su ch as hardness, density, moisture u 3 – percentage of the critical speed of the mill, u 4 – pulp water consumption a nd u 5 – mill 2018年2月1日 In another study to investigate ball size distribution on ball mill efficiency by Hlabangana et al [50] using the attainable region technique on a silica ore by dry milling, a threeball mix of Effect of ball and feed particle size distribution on the milling 2017年10月25日 For fine grinding (normal rod mill product) mill efficiency and rotational speed are less interdependent (Gow et al, 1934), and therefore slightly reduced speeds may be desirable in order to provide a suitable balance between maximum power rating for a given size of equipment, and provision for future speed up to accomodate a capacity increase or longrange Recommended Ball Mill Speed Liner Configuration2024年11月10日 Generally, the smaller the value, the more difficult the ore is to break According to the ore characteristic classification principle, the ore's crushing ability at the SAG mill belongs to the medium range (Zhou, Han, Sun, Yang, Ma, 2019; Zuo Shi, 2016) By fitting EqResearch on discrete element parameter calibration of ore
.jpg)
Optimal Speed Control for a SemiAutogenous Mill Based on
2019年12月9日 The rotation speed of a mill is an important factor related to its operation and grinding efficiency Analysis and regulation of the optimal speed under different working conditions can effectively reduce energy loss, improve productivity, and extend the service life of the equipment However, the relationship between the optimal speed and different operating 2024年10月1日 A 1097 m × 594 m SAG mill was selected for the wear sensor trial in this study The mill is part of a typical semiautogenous ball mill crushing (SABC) circuit (Zhang, 2016) (as shown in Fig 3 a) and is processing a typical copper porphyry deposit Feed ore properties and the mill operating conditions are shown in Table 1A novel IoT sensor and evolution model for grinding mill liner 2016年4月1日 An experimental study on the ultrafine grinding of gypsum ore in a dry ball mill Author links open overlay panel Bilge Öksüzoğlu a, Metin Uçurum b Show more Add to the objective of this study was to examine how grinding parameters such as mill speed, ball filling ratio, ball size distribution, powder filling ratio An experimental study on the ultrafine grinding of gypsum ore in 2024年7月31日 Conversely, elevating mill speed generally diminishes grinding efficiency, In a silica ore grinding study conducted by Danha et al [13], balls with a diameter of 10–50 mm were used It was(PDF) Effect of Grinding Conditions on Clinker Grinding Efficiency
.jpg)
SAG Mill Official Feed The Beast Wiki
The SAG Mill is a machine added by Ender IO It uses Micro Infinity (µI) to grind (or mill) items into their crushed variants, like Ores into Dusts The SAG Mill has four output slots; recipes can have 14 different outputs, with different chances of obtaining those outputs Uniquely, the SAG Mill can use Grinding Balls made from various materials to increase energy efficiency 2023年4月23日 ciency include mill design, liner design, mill speed, charge ratio, and grinding media properties The authors also indi cated that circuit efficiency is determined by how well the power applied (PDF) Grinding Media in Ball MillsA Review ResearchGate2024年6月1日 between the mill charge and the liners, and to evaluate the liner profile over the life of the liner,” Hearn said “The analysis considers a range of variables, such as the ore’s bond work index, its specific gravity, the size of the grinding media, the mill speed, and the slurry density, allowing us to accuratelyTHE FUTURE OF SAG MILLS Ausencodistribution and mill speed The feed in the mill contains fractions of ore that serves as the grinding media Larger ore fractions break the smaller particles but also breakdown themselves and exit the mill as a product In due course, the ore competency can change as fresher, harder ore is mined at deeper levels ThisSTEPPING FORWARD: USING VARIABLE SPEED DRIVES FOR OPTIMIZING
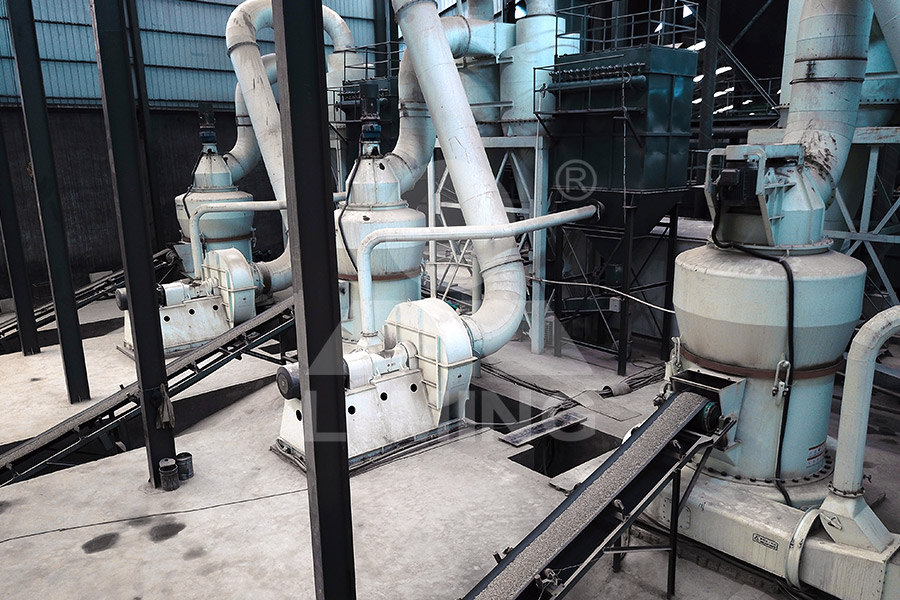
MILLING CURVES AS A TOOL FOR CHARACTERISING SAG MILL
b,ore V mill) (2) The For a fixed speed mill with only one speed to be tested, it can most probably be done within one day Table 1 Specifications of the South Deep SAG Milloperating mill speed of 74% of critical SAG mill availability was expected to be 94%, giving an annual processing rate of 17Mtpa of monzonite ore As the deposit contains around 9 percent of a harder volcanoclastic ore (Allowances for slower throughput were made when volcanics are present in the feed) Following an extensive testing andØ Effect of SAG Mill Feed Size Distribution and Ore Variability 2021年2月26日 The nominal mill efficiency, at optimum speed, is 80 Mg/h The dimensions and the high mass of the rotating elements cause the drive system to be overloaded when the mill filled with copper ore is started For this reason, the mill is stopped only in the case of a failure or planned maintenance workEnergy Efficiency Analysis of Copper Ore Ball Mill Drive However, the grinding media diameter d is normally negligible compared to the mill diameter D and is not accounted for in the calculations below To use: Enter the effective mill diameter (m) to calculate the actual critical speed (in RPM) Enter a given mill speed (in RPM) to convert to percent critical speed Click on "Calculate"Metallurgical Apps Mill Critical Speed
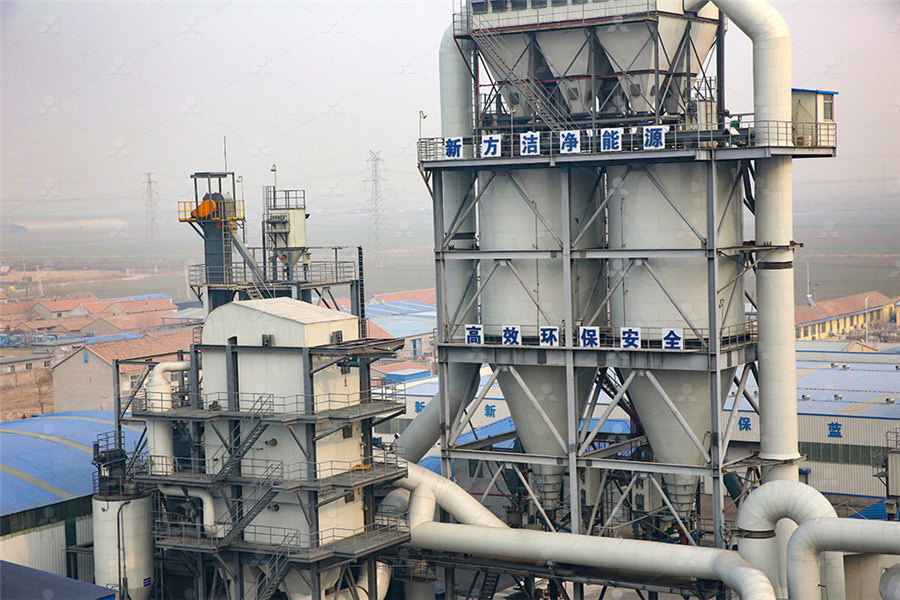
Variable Speed SAG Mill 911Metallurgist
2018年9月22日 For variable speed mills, the operating range for mill speed has to be defined so that mill power/torque requirement can be matched by the motor power/torque capability This paper will describe how this relationship can be influenced by ore grindabilitypinion is set on an output shaft of the gearbox The nominal mill efficiency, at optimum speed, is 80 Mg/h The dimensions and the high mass of the rotating elements cause the drive system to be overloaded when the mill filled with copper ore is started For this reason, the mill is stopped only in the case of a failure or planned maintenance Energy Efficiency Analysis of Copper Ore Ball Mill Drive SystemsOre grinding is one of the key stages in the mining process It's where the ore is reduced to a fine powder, which can then be used in other stages of the extraction process Grinding performance is a critical parameter for this stage, as it affects both the speed and quality of the final product The parts of a ball millFactors affecting ores grinding performance in ball mills2022年12月15日 In the present study, size reduction experiments were performed on HighPressure Grinding Rolls (HPGR), ball mill and stirred mill of PGE bearing chromite oreSize reduction performance evaluation of HPGR/ball mill and
.jpg)
Effect of Grinding Conditions on Clinker Grinding Efficiency MDPI
2024年7月31日 The production of cement, an essential material in civil engineering, requires a substantial energy input, with a significant portion of this energy consumed during the grinding stage This study addresses the gap in the literature concerning the collective impact of key parameters, including ball size, feed rate, and mill speed, on grinding efficiency Nine spherical 2021年1月22日 Impact of ball filling rate and stirrer tip speed on milling iron ore by wet stirred mill: Analysis and prediction of the particle size distribution Author links open overlay panel Wang Guo a b, Yuexin Han a b, Batch grinding studies by a ball mill for hematite ore Materials Today: Proceedings, Volume 26, Part 2, 2020, pp 825832Impact of ball filling rate and stirrer tip speed on milling iron ore Figure 3(a)—Pilot SAG mill Ecs vs Ball Load, Reproduced from Morrell (2006a); (b) SAG Mill Ecs vs Ball Load for ‘OpenCircuit’ SAG Mills in JKTech Database 0 2 4 6 8 10 12 14 16 18 20 0 2 4 6 8 10 12 14 SAG mill Ecs (kWh/t) Ball load (%) 0 5 10 15 20 SAG mill Ecs (kWh/t) Ball load (%) Coarse feed, uncrushed pebbles Very soft ores, Axb >80SAG Mill Design and Benchmarking Using Trends in the JKTech 2017年5月1日 Crushing and grinding consume most of the energy in mineral processing Ball mill is an important kind of grinding equipment used to decrease the size of ore particles The power consumption of a ball mill is one of the most important parameters to consider in the design of a ball mill because it determines its economic efficiencyEffect of lifters and mill speed on particle behaviour, torque, and
.jpg)
v117n1a11 Performance optimization of an industrial ball mill for
density, ball mill speed and grinding media consumption rate, water spray rate on the highfrequency screen, and feed pulp density to the screen The performance of the ball mill varied with the ore properties The effect of process parameters on ultrafines generation and power consumption in the ball mill is explained further