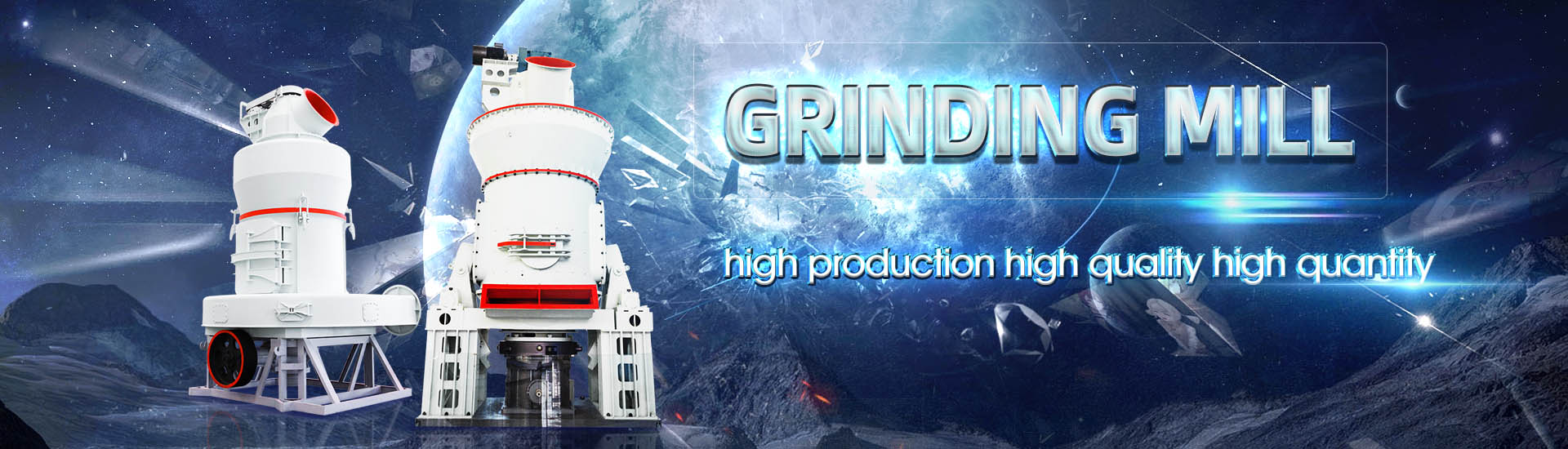
Vanadium titanium slag grinding production line process
.jpg)
Research progress of vanadium extraction processes from
2024年8月21日 The ion exchange method uses ion exchange resin as the separation medium to separate vanadium from the leaching solution In order to better extract vanadium in aqueous 2024年2月15日 The smelting process of vanadium and titanium magnetite produces vanadiumbearing steel slag, a key material for vanadium extraction Herein, vanadium production, Vanadium extraction from steel slag: Generation, recycling and 2022年7月13日 Vanadium slag is a strategic vanadium extracting source, which is produced from the hotmetal treatment prior to the basic oxygen steelmaking (BOS) or during the Mechanism on the Separation of Vanadium and Titanium from the vanadium slag system of the FeO–SiO 2–V 2O 3–TiO 2 have been successfully applied in industry due to the limitations of existing process for treating the complex system Therefore, Separation of Vanadium and Titanium Phase from the Vanadium
.jpg)
Study on Current Technology of Vanadium Extraction from
2024年10月1日 The iron in vanadium titanium magnetite enters the molten iron through the ironmaking process, while the vanadium in the ore is selectively reduced by converter blowing Fluxless smelting in a directcurrent openarc furnace is proposed as an opportunity to improve iron and vanadium recovery and potentially unlock the titanium as a slag product Slags Evaluation of TitaniaRich Slag Produced from Titaniferous In response to the problem of rich vanadium–titanium magnetite (VTM) resources in China contrasting with low blast furnace utilization, a HIsmelt process for smelting VTM is proposed Analysing the HIsmelt process for smelting vanadium–titanium 2020年11月19日 Hightitanium slag can be used as a highquality raw material to produce UGS for the chlorination process The traditional electric furnace smelting process is always HighTitanium Slag Preparation Process by Carbothermic
.jpg)
A review on vanadium extraction techniques from major vanadium
2024年6月1日 The critical role of vanadium in metallurgy and the increasing commercialization of vanadium redox flow batteries have contributed to a rise in market demand for vanadium, emphasizing the need to ensure the sustainability of vanadium production Converter vanadium slag and stone coal, generated during the smelting process of vanadium–titanium magnetite, 2020年11月19日 As the titanium industry rapidly develops, lowgrade ilmenite resources are drawing global attention The direct use of lowgrade ilmenite can result in low production efficiency and heavy pollution In addition, the production of hightitanium slag via electric furnace melting consumes significant energy and possesses low production efficiency Therefore, a HighTitanium Slag Preparation Process by CarbothermicOnline version ISSN 24119717 the main method of VTM utilization is in ironmaking via the blast furnace route and the basic oxygen furnace process for vanadium recovery However, the recovery ratios of Fe (into pig iron), V A new process for the recovery of iron, vanadium, and 2021年12月16日 For several decades, the metallurgical industry and the research community worldwide have been challenged to develop energyefficient and lowcost titanium production processes The expensive and energyconsuming Kroll process produces titanium metal commercially, which is highly matured and optimized Titanium’s strong affinity for oxygen Titanium: An Overview of Resources and Production Methods
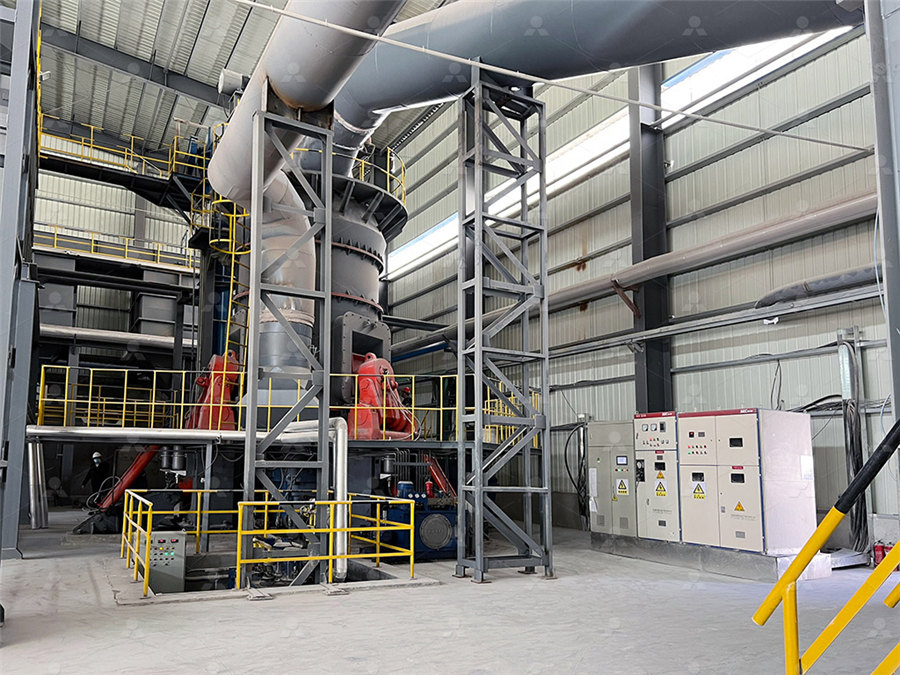
Technological research of process for producing titanium rich slag
2023年8月1日 For smelting of titanium rich slag, the lowash reducing agents were used, ie, some oxides (SiO 2, Al 2 O 3, CaО and MgO) convert into the slag and impoverish target product slag The low electrical conductivity and ash content of the reducing agent ensures a high electrical resistance of the charge, a deep fit of electrodes, a stable electrical mode and a removed for producing titanium slag via electric furnace smelting Titanium slag can be classified as ultragrade slag (UGS) and highgrade slag (HGS) UGS is preferred for producing titanium dioxide via chlorination, while HGS, with high impurities, is mostly used in the sulfuric acid process Both UGS and HGS are mainlyHighTitanium Slag Preparation Process by Carbothermic2020年8月3日 Titaniumbearing magnetite ore is generically defined as magnetite with > 1% titanium dioxide (TiO2) and is usually vanadiumbearing The iron and titanium occur as a mixture of magnetite (Fe3O4) and ilmenite (FeTiO3) with vanadium oxide usually occurring within the solid solution of the titaniumbearing magnetite phase These ores are currently widely processed in Evaluation of TitaniaRich Slag Produced from Titaniferous 2024年10月1日 The blast furnace method for treating vanadium titanium magnetite has the advantages of high production efficiency and largescale production, but there are also the following problems : (1) Due to the consumption of a large amount of precious metallurgical coke during the production process, it is not conducive to the sustainable development of blast Study on Current Technology of Vanadium Extraction from Vanadium
.jpg)
Nickel Slag Production Line Zoomjo Group
Nickel slag, manganese slag, vanadium and titanium slag, etc are industrial waste slags produced in the smelting process of nickeliron ore, vanadium and titanium ore, etc The stock is huge and the comprehensive utilization rate is low Nickel slag production line is to separate nickel and other useful metals from them by conveying nickel 2022年1月1日 The slag phase mainly consisted of spinel, silicates and wustite, in which the FeO content gradually decreased during the slag evolution process Anosovite and silicate were the main phases in the slag fraction at the dripping temperature of 1441 °C Titanium carbide (TiC) was also verified, which was an unfavorable product for the slag Phase transformation and slag evolution of vanadium–titanium 2014年6月1日 A new process comprising metallizing reduction, magnetic separation, and electroheat melting separation is proposed with the aim of achieving high recoveries of iron, vanadium, and titanium from A new process for the recovery of iron, vanadium, and 2023年1月1日 During the steelmaking process, a great amount of slag is generated as a byproduct Vanadiumbearing steelmaking slags are classified as hazardous and require special handling and storage due to High efficient vanadium extraction from vanadium slag using an
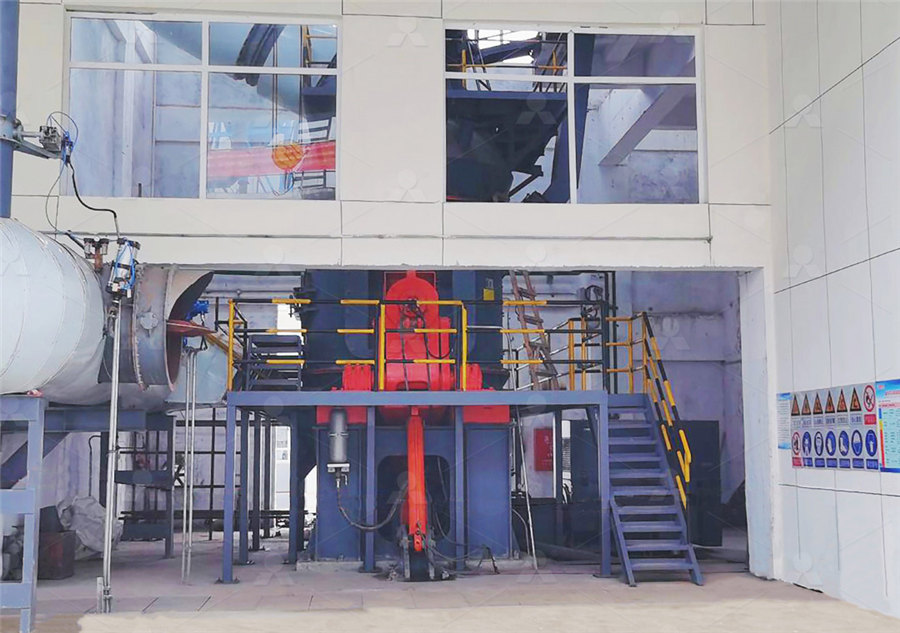
Upgrading of raw vanadium titanomagnetite concentrate SAIMM
content in titanium slag is above 50%, it can be recovered by acid leaching methods (Zheng et al, 2016) Therefore, to improve the TiO 2 grade in titanium slag, a reductionmelting process was pursued by Panzhihua Iron and Steel Group In this process, the reduction of vanadium titanomagnetite concentrate (containing approximately 54% Fe)2022年9月20日 As for the utilization of vanadium slag, calcification roasting process is a newly developed and clean method compared with sodium roasting process (Cao, 2012; Jiang et al, 2018; Wang et al, 2021; Wen et al, 2020b; Xiang et al, 2018; Zhang et al, 2015)Calcium salts such as CaO and CaCO 3 oxidize and calcify vanadiumspinel selectively into acidsoluble or Clean and efficient extraction of vanadium from vanadium slag: Titanium Dioxide Production Line,Titanium Dioxide Processing Uranium Ore Separation Machinery and Equipment; Gulin machinery titanium dioxide production line is made up of Titanium for titanium recovery from slag » More detailed summary of the tio2 slag plant process – Crusher South Africa Mining Equipment; Production Line; Ore Crushing; Mobile titanium slag production line equipment – Grinding Mill China2003年10月1日 Besides the slag, also pig iron is produced, but the slag is the main product of the process Because the subsequent fluidizedbed chlorination, used to manufacture pigment from the slag, can only (PDF) Physicochemical Aspects of Titanium Slag Production
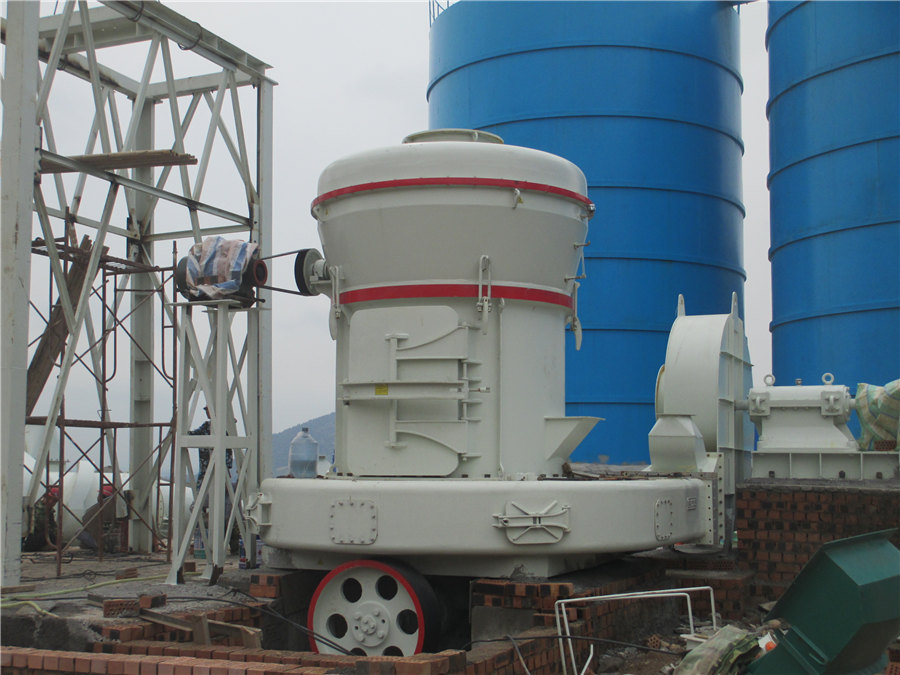
Titaniferous Magnetites as a Source of Vanadium, Titanium and
Titanium Production (Optional) Titanium is often lost to waste streams at various stages of the process; however, modern processing technologies have enabled the extraction of titanium from the titania slag as a saleable product The slag can be leached to recover the titanium by several different lixiviants2023年2月22日 Vanadium titanomagnetite (VTM) is a valuable multielement symbiotic ore mainly composed of iron, vanadium, and titanium, as well as small amounts of chromium, nickel and cobalt [1,2,3]The global resource reserves of the VTM ore are extremely rich (over 40 billion tons) and are mainly distributed in Russia, South Africa, China, the United States, Canada, Process Mineralogy of Vanadium Titanomagnetite Ore in content in titanium slag is above 50%, it can be recovered by acid leaching methods (Zheng et al, 2016) Therefore, to improve the TiO 2 grade in titanium slag, a reductionmelting process was pursued by Panzhihua Iron and Steel Group In this process, the reduction of vanadium titanomagnetite concentrate (containing approximately 54% Fe)Upgrading of raw vanadium titanomagnetite concentratevanadium oxide usually occurring within the solid solution of the titaniumbearing magnetite phase These ores are currently widely processed in blast furnaces via modified ironmaking processes Typically, vanadium is recovered as a byproduct from the ironmaking process, while the diluted titania slag is stockpiledEvaluation of TitaniaRich Slag Produced from Titaniferous
.jpg)
Research progress of vanadium extraction processes from vanadium slag
2024年8月21日 Fig 2 shows the distribution of vanadium ore in the world The world's vanadium ore reserves are about 24165 × 10 7 t, which represents the portion that meets requirements of current extraction and production The reserves of vanadium in China, Russia, South Africa and Australia account for 99 % of the world's reserves, and China's vanadium ore reserves are the 21 Roasting of Vanadium Steel Slag The original vanadium steel slag, obtained from a converter steelmaking plant, Kunming Iron and Steel Corporation in Yunnan Province, China, was crushed and ground to less than 150 μm The obtained vanadium steel slag was mixed with sodium carbonate and calcium fluoridewith a mass ratio of 80:20:312Rapid Vanadium Extraction from Roasted Vanadium Steel Slag 2020年8月3日 Titaniumbearing magnetite ore is generically defined as magnetite with > 1% titanium dioxide (TiO2) and is usually vanadiumbearing The iron and titanium occur as a mixture of magnetite (Fe3O4 (PDF) Evaluation of TitaniaRich Slag Produced from this scenario is the production of steel using vanadiumtitanium magnetite (VTM) as the raw material through the blastconverter furnace process [36,37] This process yields vanadium slag, characterized by elevated quantities of iron, vanadium, titanium and manganese oxides, but with lower CaO, Al2O3 and MgO contents [38]The influence of vanadium and titanium oxides in slag on the
.jpg)
A novel process for the recovery of iron, titanium, and vanadium
2017年5月1日 Request PDF A novel process for the recovery of iron, titanium, and vanadium from vanadiumbearing titanomagnetite: sodium modification–direct reduction coupled process A sodium modification 2020年5月1日 A novel process featuring pressurized pyrolysis of ammonium chlorideacid leachingsolvent extraction was carried out to separate vanadium, titanium and iron from vanadiumbearing titanomagnetite Efficient separation of vanadium, titanium and iron from vanadium 2018年4月25日 In China, vanadium slag, a byproduct of vanadiumtitanium magnetite in the converter steelmaking process, is a typical vanadium metallurgical raw material, Oxidation process of lowgrade vanadium slag in presence of Na 2 CO 3 Trans Nonferrous Met Soc China, 21 (2011), pp 18601867 View PDF View article View in Scopus Simultaneous extraction of vanadium and titanium from vanadium slag 2022年2月26日 Vanadium slag (VS) is a byproduct of vanadium titanium magnetite BOF steelmaking process and becomes an important material for vanadium products preparation(PDF) A Novel Method of Recovery Vanadium from Vanadium Slag
.jpg)
A review on the extraction of vanadium pentoxide from primary
2022年5月27日 Vanadium, like titanium, can be recovered from coproduct slag, derived from iron processing for steel production during the smelting of titanomagnetite ores [4]content in titanium slag is above 50%, it can be recovered by acid leaching methods (Zheng et al, 2016) Therefore, to improve the TiO 2 grade in titanium slag, a reductionmelting process was pursued by Panzhihua Iron and Steel Group In this process, the reduction of vanadium titanomagnetite concentrate (containing approximately 54% Fe)Upgrading of raw vanadium titanomagnetite concentrate2024年6月1日 The critical role of vanadium in metallurgy and the increasing commercialization of vanadium redox flow batteries have contributed to a rise in market demand for vanadium, emphasizing the need to ensure the sustainability of vanadium production Converter vanadium slag and stone coal, generated during the smelting process of vanadium–titanium magnetite, A review on vanadium extraction techniques from major vanadium 2020年11月19日 As the titanium industry rapidly develops, lowgrade ilmenite resources are drawing global attention The direct use of lowgrade ilmenite can result in low production efficiency and heavy pollution In addition, the production of hightitanium slag via electric furnace melting consumes significant energy and possesses low production efficiency Therefore, a HighTitanium Slag Preparation Process by Carbothermic
.jpg)
A new process for the recovery of iron, vanadium, and
Online version ISSN 24119717 the main method of VTM utilization is in ironmaking via the blast furnace route and the basic oxygen furnace process for vanadium recovery However, the recovery ratios of Fe (into pig iron), V 2021年12月16日 For several decades, the metallurgical industry and the research community worldwide have been challenged to develop energyefficient and lowcost titanium production processes The expensive and energyconsuming Kroll process produces titanium metal commercially, which is highly matured and optimized Titanium’s strong affinity for oxygen Titanium: An Overview of Resources and Production Methods2023年8月1日 For smelting of titanium rich slag, the lowash reducing agents were used, ie, some oxides (SiO 2, Al 2 O 3, CaО and MgO) convert into the slag and impoverish target product slag The low electrical conductivity and ash content of the reducing agent ensures a high electrical resistance of the charge, a deep fit of electrodes, a stable electrical mode and a Technological research of process for producing titanium rich slag removed for producing titanium slag via electric furnace smelting Titanium slag can be classified as ultragrade slag (UGS) and highgrade slag (HGS) UGS is preferred for producing titanium dioxide via chlorination, while HGS, with high impurities, is mostly used in the sulfuric acid process Both UGS and HGS are mainlyHighTitanium Slag Preparation Process by Carbothermic

Evaluation of TitaniaRich Slag Produced from Titaniferous
2020年8月3日 Titaniumbearing magnetite ore is generically defined as magnetite with > 1% titanium dioxide (TiO2) and is usually vanadiumbearing The iron and titanium occur as a mixture of magnetite (Fe3O4) and ilmenite (FeTiO3) with vanadium oxide usually occurring within the solid solution of the titaniumbearing magnetite phase These ores are currently widely processed in 2024年10月1日 The blast furnace method for treating vanadium titanium magnetite has the advantages of high production efficiency and largescale production, but there are also the following problems : (1) Due to the consumption of a large amount of precious metallurgical coke during the production process, it is not conducive to the sustainable development of blast Study on Current Technology of Vanadium Extraction from Vanadium Nickel slag, manganese slag, vanadium and titanium slag, etc are industrial waste slags produced in the smelting process of nickeliron ore, vanadium and titanium ore, etc The stock is huge and the comprehensive utilization rate is low Nickel slag production line is to separate nickel and other useful metals from them by conveying nickel Nickel Slag Production Line Zoomjo Group2022年1月1日 The slag phase mainly consisted of spinel, silicates and wustite, in which the FeO content gradually decreased during the slag evolution process Anosovite and silicate were the main phases in the slag fraction at the dripping temperature of 1441 °C Titanium carbide (TiC) was also verified, which was an unfavorable product for the slag Phase transformation and slag evolution of vanadium–titanium