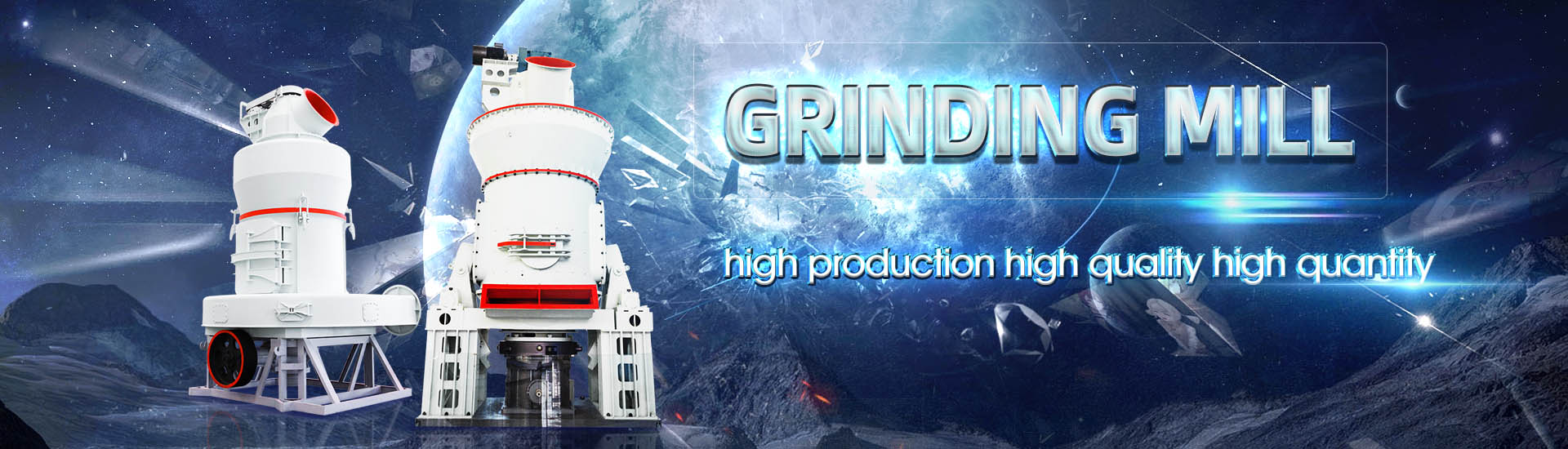
The impact of coal powder airflow ignition on the vertical mill
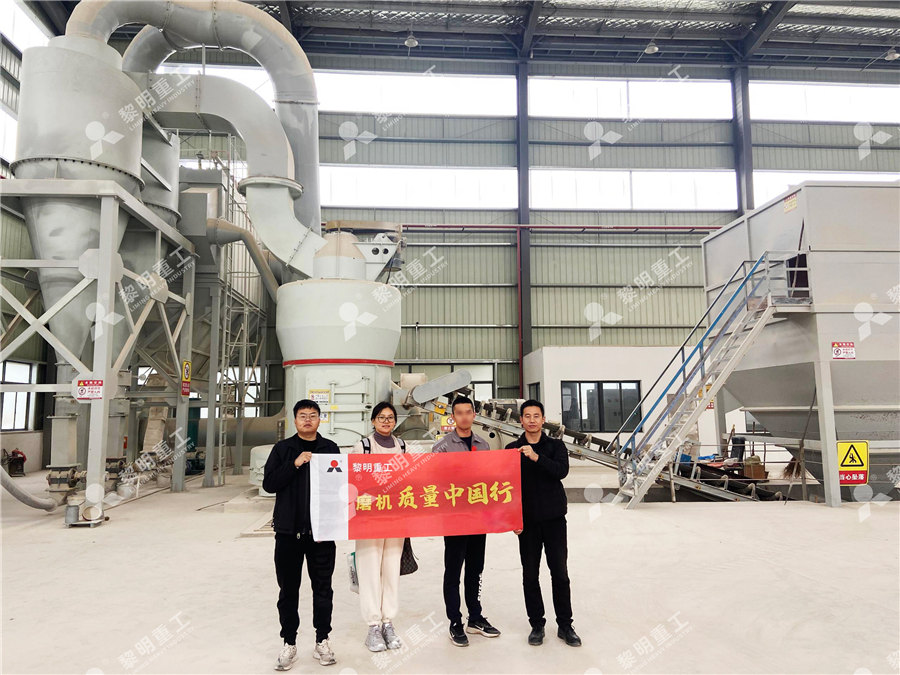
Numerical Study of Flow Field and Particle Motion Characteristics
2024年11月1日 Particle discharge from Raw Coal VRMs was improved In order to improve the motion characteristics of particles in vertical roller mills (VRMs), the assumption that different 2020年5月11日 The effect of mechanically activated coal grinding on the time of their ignition in a vertical tubular reactor is studied experimentally and numerically The experiments showed Ignition test for mechanically activated pulverized coal in a vertical this dissertation was to investigate the effect of coal feedstock property variation on the vertical spindle coal pulverising mill’s performance to facilitate optimal plant performance Plant design Performance optimisation of vertical spindle coal pulverisersImprovements in coal and airflow balance enhance combustion efficiency, leading to improvements in flyash loss on ignition (LOI) and unburned carbon (UBC), CO and NOx 13045 Coal Distributor Paper:Layout 1 Babcock Power
.jpg)
Coal Mill an overview ScienceDirect Topics
Coal mills or pulverizers play a very essential part in the coalfired power production system Coal mills grind the coal into fine powder, and the primary air entering the mill dries and drives the 2020年8月12日 To understand the performance of a vertical roller coal mill, the real operational tests have been performed considering three different coal sources Obtained results indicate An investigation of performance characteristics and energetic This study investigates the effect of changes in coal and airflow feed rates on the classification performance that occurs in an industrial scale ballandrace vertical spindle mill in which the Investigation of the Classification Operation in a Coal Pulverising 2020年8月12日 This study shows the performance of a currently running vertical roller coal mill (VRM) in an existing coalfired power plant In a power plant, the coal mill is the critical An investigation of performance characteristics and energetic
.jpg)
Influence of Grinding Methodology and Particle Size on Coal and
The results of the research showed that the joint grinding of coal and biomass contributes to the achievement of the minimum size of coal and wood and, as a result, leads to an increase in Abstract: The paper presents development and validation of coal mill model (including the action of classifier) to be used for improved coal mill control The model is developed by using the mass and heat balance equations of the coal mill Genetic Algorithm is used to estimate the unknown parameters that are used in the model validationModeling and Control of Coal MillThe paper presents development and validation of coal mill model (including the action of classifier) Powder Technology, 2009 Mill discharge temperature and differential pressure have a strong effect on efficiency and safety of a coal fired power INTRODUCTION A simplified design schematic of a vertical spindle mill is shown in Figure 1(PDF) Modeling and Control of Coal Mill AcademiaVertical Coal Mill (VCM) is equipment for grinding and pulverizing coal into micron size Rotary kilns then use the powders as fuel burners The VCM has a housing section equipped with a lining The layout of the coal mill with a rotary classifier
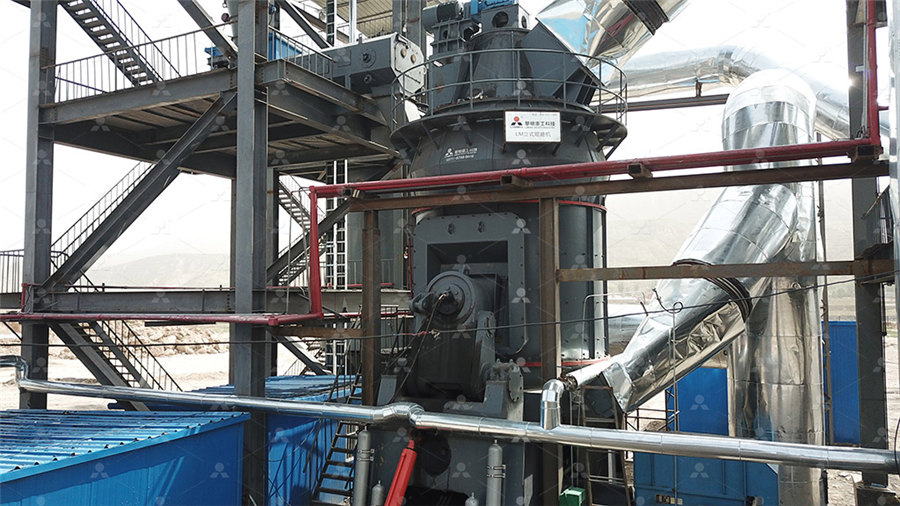
Modeling of Coal Mill System Used for Fault Simulation
2020年4月7日 Because the amount of raw coal and coal powder stored in the mill c annot be measured, there is no a ctual reference data in the model identification process So, t he dynamic characteristic of rawDownload scientific diagram Technical specifications of vertical roller coal mill from publication: An investigation of performance characteristics and energetic efficiency of vertical roller Technical specifications of vertical roller coal mill2020年1月1日 Combustion or gasification of coal in nitrogenfree environment (CO2H2OO2) is a promising technology contributing to reduce the carbon footprint in the energy industryThe effect of steam on air gasification of mechanically activated coal Mechanically pulverizing coal into a fine powder enables it to be burned like a gas, Combustion Engineering 783RP BowlMill Coal Pulverizer enclosed chamber with wear resistant plates The hammers impact on the coal, crushing it against the plates Further pulverization is achieved as the smaller coal particles areImproving Coal Pulverizer Performance and Reliability Pall
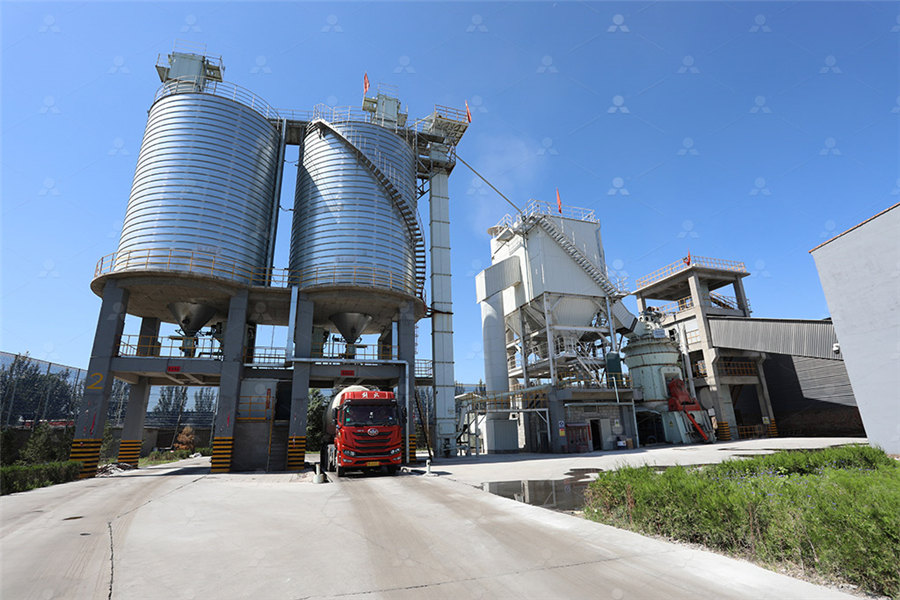
Analysis of the Coal Milling Operations to the Boiler Parameters
2020年4月2日 represent the temperature distribution in the boiler while PCs pipes at level 1 are not in service In the meanwhile, the others PC still in service and produced 700MWnett2021年10月10日 The influences of particle size and particle size dispersion of coal with different metamorphic degrees on the explosion severity have been studied 16,17 Researchers have analyzed the influences of particle size and concentration on the minimum ignition temperature of coal dust 18,19 From the perspective of experimental research and data analysis, 20,21 most Influence of Volatile Content on the Explosion Characteristics of Coal 2021年6月29日 The aim of this work was to observe the impact of the milling technique employed by the DESI 11 disintegrator on the properties of fly ash This type of mill is a highspeed pin mill with two Effects of Mill Speed and Air Classifier Speed on Performance of 2020年4月7日 Monitoring and diagnosis of coal mill systems are critical to the security operation of power plants The traditional datadriven fault diagnosis methods often result in low fault recognition rate or even misjudgment due to Modeling of Coal Mill System Used for Fault
.jpg)
Effect of ammonia on the characteristics of coal combustion
2023年8月1日 The ignition temperature of ammonia is 860 °C, which belongs to the extremely difficult ignition grade, and its ignition characteristics are worse than typical bituminous coal With the increase of ammonia blending ratios, the ignition temperature of the mixed fuel increases, which will bring challenges to the ignition of ammonia/coal cocombustion2020年8月1日 The ignition and combustion characteristics of anthraciterice husk (ACRH) and bituminous coalrice husk (BCRH) pellets were investigated in a vertical heating tube furnace under different experimental condition, for gas temperature (873 K–1073 K) and under air and different oxygen concentration (21–70%) in CO 2 /O 2 atmosphere The investigation of the Experimental study on ignition and combustion of coalrice husk 2023年2月25日 Moreover, the ignition and initial combustion of coal/air flow are highly dependent on the oxygen provided by primary air Hence, the variation of PAR will inevitably impact the infurnace air distribution patterns and coal combustion behavior [34], especially at Numerical study on the effects of primary air ratio on ultralow 2019年10月4日 A similar conclusion was reported in another study carried out based on numerical simulations 19 Li et al 20 investigated the impact of the particle size of coal dust on its spontaneous Effects of particle size on the selfignition behaviour of a coal
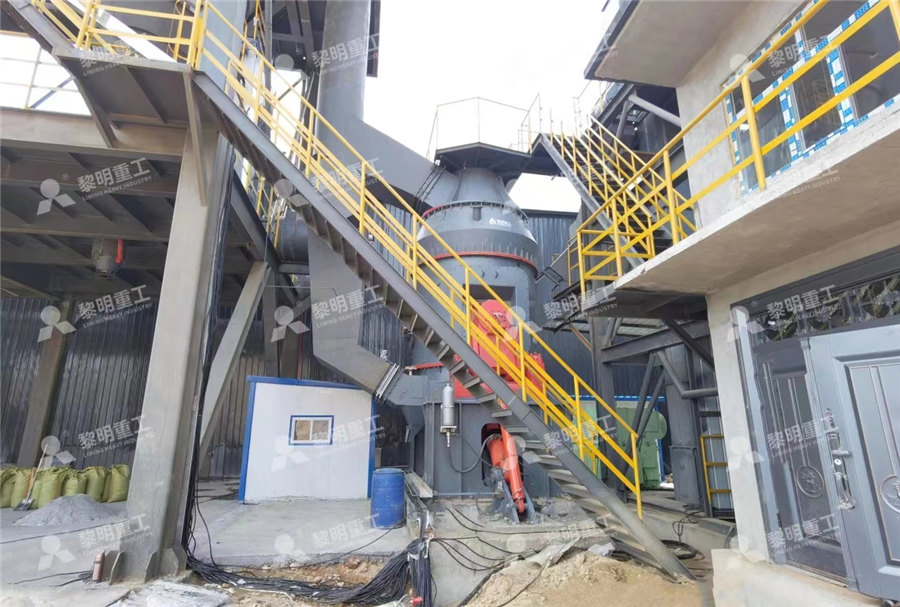
A Comparison of Three Types of Coal Pulverizers Babcock Power
The BTM is a lowspeed mill that primarily grinds coal by impact and attrition The VRM is a medium speed mill that grinds coal by compression and, because of the low coal inventory in the mill and flat grinding surfaces, develops shearing action as well For both mills a constant centrifugal force is maintained The speedA vertical roller mill, also known as a vertical grinding mill or vertical mill, is a comprehensive grinding equipment integrating crushing, drying, grinding, grading, and conveying Vertical grinding mills can be widely used in electric power, metallurgy, construction, chemical industry, and other industries to make powder, especially for materials such as cement clinker, coal Energysaving and Efficient Vertical Roller Mill Fote Machinery2024年11月1日 Numerical Study of Flow Field and Particle Motion Characteristics on Raw Coal Vertical Roller Mill Circuits Author links employed the Realizable k–ε model to simulate the rotational movement of airflow inside a coal mill According to the above literature the present study investigated the impact of different widths of Numerical Study of Flow Field and Particle Motion Characteristics 2016年4月5日 In PFboilers, coal is pulverised in a mill (or pulveriser) before being entrained by primary combustion air to burners, to form a high temperature flame in the furnace of the boiler (1000–1600 °C) [2]The fineness of the coal powder, as well as the uniformity of the coal flow sent to each burner fed by the same mill, are crucial parameters to achieve an effective combustion Online monitoring of coal particle size and flow distribution in coal

How to operate an air classifier mill to meet your fine grinding goals
shown in Figure 2a This makes the mill much taller than the vertical mill, but allows it to be closely coupled with a cyclone or filterreceiver when required This mill’s classifier wheel and impact rotor have independent drives, and the mill can handle the same grinding applications as the vertical mill Combined drive2020年11月25日 Dried coal of BRXL lignite emits a smaller amt of NOx than that of BRXL lignite However, the dried degree of BRXL lignite is closely related to R90 fineness Dried coal with optimal moisture content yields least NOx A Control Strategy of the Air Flow Rate of CoalFired 2019年8月1日 Numerical simulation study on the influences of the secondarytertiary air proportion on the airflow mixing effects and pulverized coal combustion characteristics in a 300MW downfired boilerNumerical simulation study on the influences of the secondary 2016年3月1日 Experimental data can be observed that feeding Berau coal having the characteristics of Subbituminous coal with total moisture of 2142% Wt and HGI 50, by setting MAFR is (1,8:1), and classifier Performance of the static air classifier in a Vertical Spindle Mill
.jpg)
The effects of particle size and reducingtooxidizing environment on
2018年9月1日 Coal particles experience a transition from a reducing to oxidizing environment in the nearburner region of pulverized coal (pc) boilers For the first time, we report a fundamental study of ignition of a coalparticle stream experiencing a flame environment that transitions from a reducing to an oxidizing environment (termed reducingtooxidizing environment)2012年1月13日 The vertical axis of Fig 9 is the reciprocal of the lean flammability limit concentration Example series of flame photos of pulverized coal ignition Coal particles were ignited by injecting high temperature gas flow The effects of diameter on ignition performances for the wood powder were examined in detailFundamental Experiments of Coal Ignition for Engineering Design of Coal 2020年8月12日 To understand the performance of a vertical roller coal mill, the real operational tests have been performed considering three different coal sources Obtained results indicate that grinding pressure, primary air (PA) temperature and mill motor current have a tendency to rise by increasing coal feeding mass flow rates for all used coalAn investigation of performance characteristics and energetic 2022年3月9日 MIKE III apparatus tests were conducted to investigate the minimum ignition energy (MIE) of coal dusts in air and O2/CO2 atmospheres with and without small amount of CH4/H2Effect of oxygen concentration, inert gas and CH4/H2 addition on
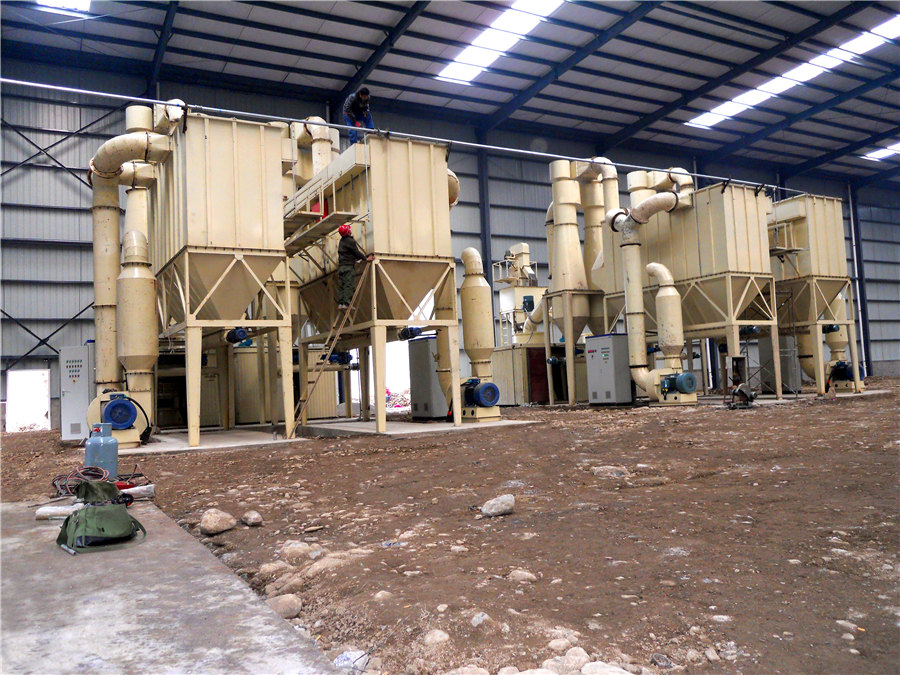
A unified thermomechanical model for coal mill operation
2015年11月1日 As presented by Andersen et al (2009) and Odgaard, Stoustrup, and Mataji (2007), coal moisture imposes limit on the maximum load at which a coal mill can be operated and the load gradient (how fast the mill may change its operating point), if it is desired that the pulverized coal entering the furnace has moisture content less than or equal to a certain value 1 The coal + air mixture at the ignition point is flammable 2 Coal particles are heated by high temp erature gas in the recirculation flow 3 Coal particles are also heated by radiant heat from the surroundings The conditions (1) and (3) were investigated by Fundamental Experiments of Coal Ignition for Engineering Design of Coal 2016年10月25日 The geometry of dust layers is cylindrical in hot plate tests and all the thermocouples are placed on a symmetry axis (or vertical centerline r = 0) of the dust layer in the experimental study [4]Therefore, the twodimensional timedependent conservation equations in this paper are sufficient to model the process for the axisymmetric dust layers as illustrated in Numerical study on the ignition behavior of coal dust layers in Abstract: The paper presents development and validation of coal mill model (including the action of classifier) to be used for improved coal mill control The model is developed by using the mass and heat balance equations of the coal mill Genetic Algorithm is used to estimate the unknown parameters that are used in the model validationModeling and Control of Coal Mill
.jpg)
(PDF) Modeling and Control of Coal Mill Academia
The paper presents development and validation of coal mill model (including the action of classifier) Powder Technology, 2009 Mill discharge temperature and differential pressure have a strong effect on efficiency and safety of a coal fired power INTRODUCTION A simplified design schematic of a vertical spindle mill is shown in Figure 1Vertical Coal Mill (VCM) is equipment for grinding and pulverizing coal into micron size Rotary kilns then use the powders as fuel burners The VCM has a housing section equipped with a lining The layout of the coal mill with a rotary classifier2020年4月7日 Because the amount of raw coal and coal powder stored in the mill c annot be measured, there is no a ctual reference data in the model identification process So, t he dynamic characteristic of rawModeling of Coal Mill System Used for Fault SimulationDownload scientific diagram Technical specifications of vertical roller coal mill from publication: An investigation of performance characteristics and energetic efficiency of vertical roller Technical specifications of vertical roller coal mill
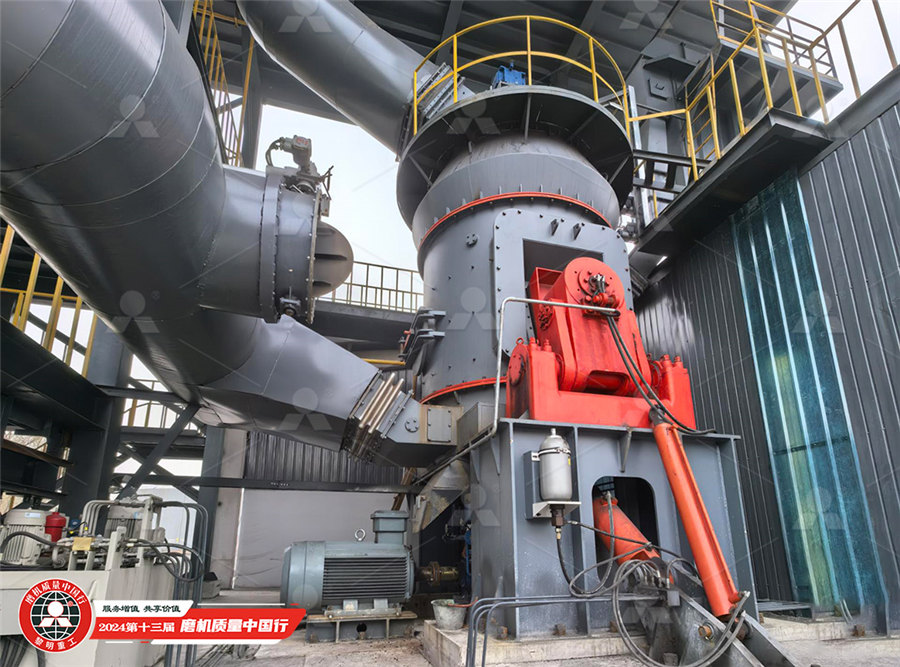
The effect of steam on air gasification of mechanically activated coal
2020年1月1日 Combustion or gasification of coal in nitrogenfree environment (CO2H2OO2) is a promising technology contributing to reduce the carbon footprint in the energy industryMechanically pulverizing coal into a fine powder enables it to be burned like a gas, Combustion Engineering 783RP BowlMill Coal Pulverizer enclosed chamber with wear resistant plates The hammers impact on the coal, crushing it against the plates Further pulverization is achieved as the smaller coal particles areImproving Coal Pulverizer Performance and Reliability Pall 2020年4月2日 represent the temperature distribution in the boiler while PCs pipes at level 1 are not in service In the meanwhile, the others PC still in service and produced 700MWnettAnalysis of the Coal Milling Operations to the Boiler Parameters2021年10月10日 The influences of particle size and particle size dispersion of coal with different metamorphic degrees on the explosion severity have been studied 16,17 Researchers have analyzed the influences of particle size and concentration on the minimum ignition temperature of coal dust 18,19 From the perspective of experimental research and data analysis, 20,21 most Influence of Volatile Content on the Explosion Characteristics of Coal

Effects of Mill Speed and Air Classifier Speed on Performance of
2021年6月29日 The aim of this work was to observe the impact of the milling technique employed by the DESI 11 disintegrator on the properties of fly ash This type of mill is a highspeed pin mill with two